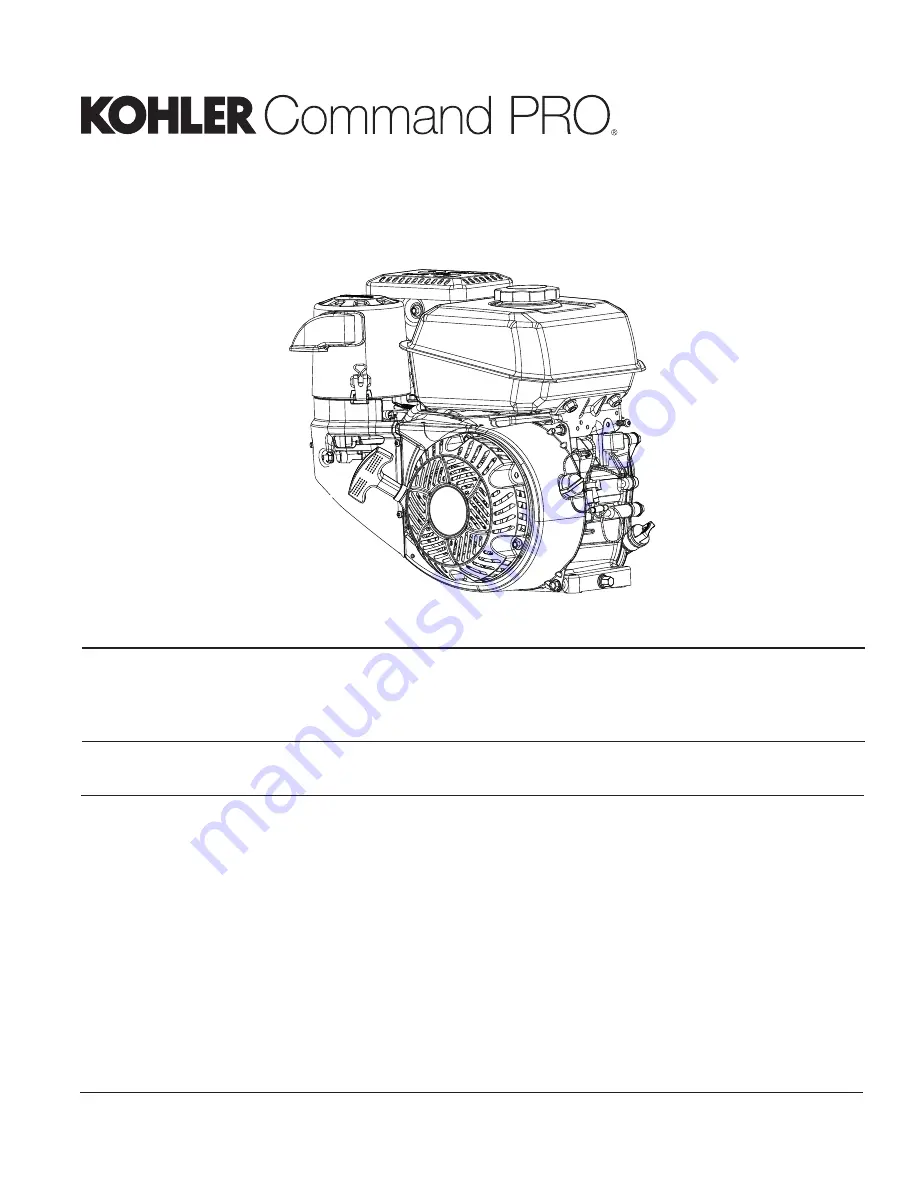
1
17 690 01 Rev. F
KohlerEngines.com
CH260-CH440
Service Manual
2
Safety
3
Maintenance
5
Speci
fi
cations
18
Tools and Aids
21
Troubleshooting
25
Air Cleaner/Intake
26
Fuel System
30
Governor System
31
Lubrication System
32
Electrical System
39
Starter System
44
Disassembly/Inspection and Service
59
Reassembly
IMPORTANT: Read all safety precautions and instructions carefully before operating equipment. Refer to operating
instruction of equipment that this engine powers.
Ensure engine is stopped and level before performing any maintenance or service.