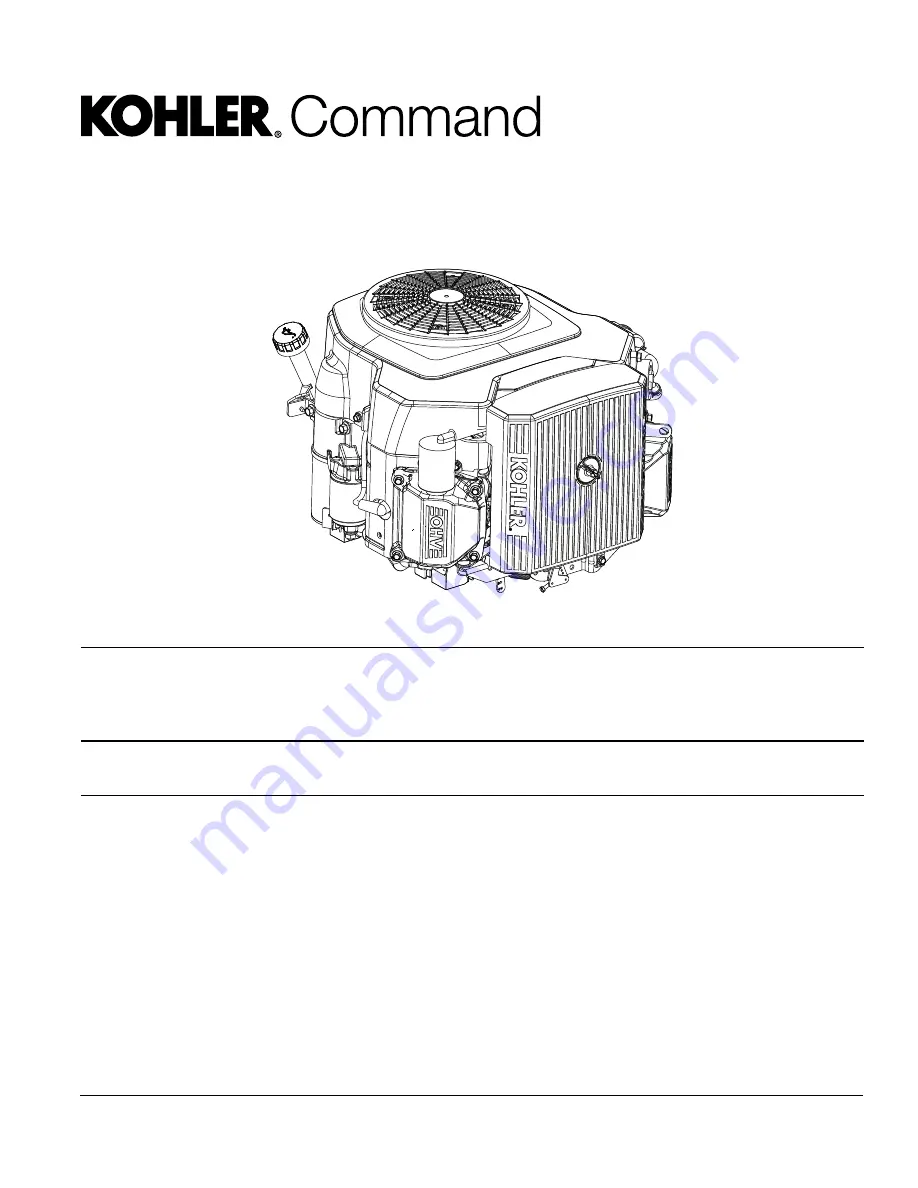
1
24 690 07 Rev. H
KohlerEngines.com
CV17-CV25, CV620-CV730, CV740, CV750
S
ervice Manual
2
Safety
3
Maintenance
5
Specifications
16
Tools and Aids
19
Troubleshooting
23
Air Cleaner/Intake
24
Fuel System
30
Governor System
31
Lubrication System
33
Electrical System
49
Starter System
58
Disassembly/Inspection and Service
75
Reassembly
IMPORTANT: Read all safety precautions and instructions carefully before operating equipment. Refer to operating
instruction of equipment that this engine powers.
Ensure engine is stopped and level before performing any maintenance or service.