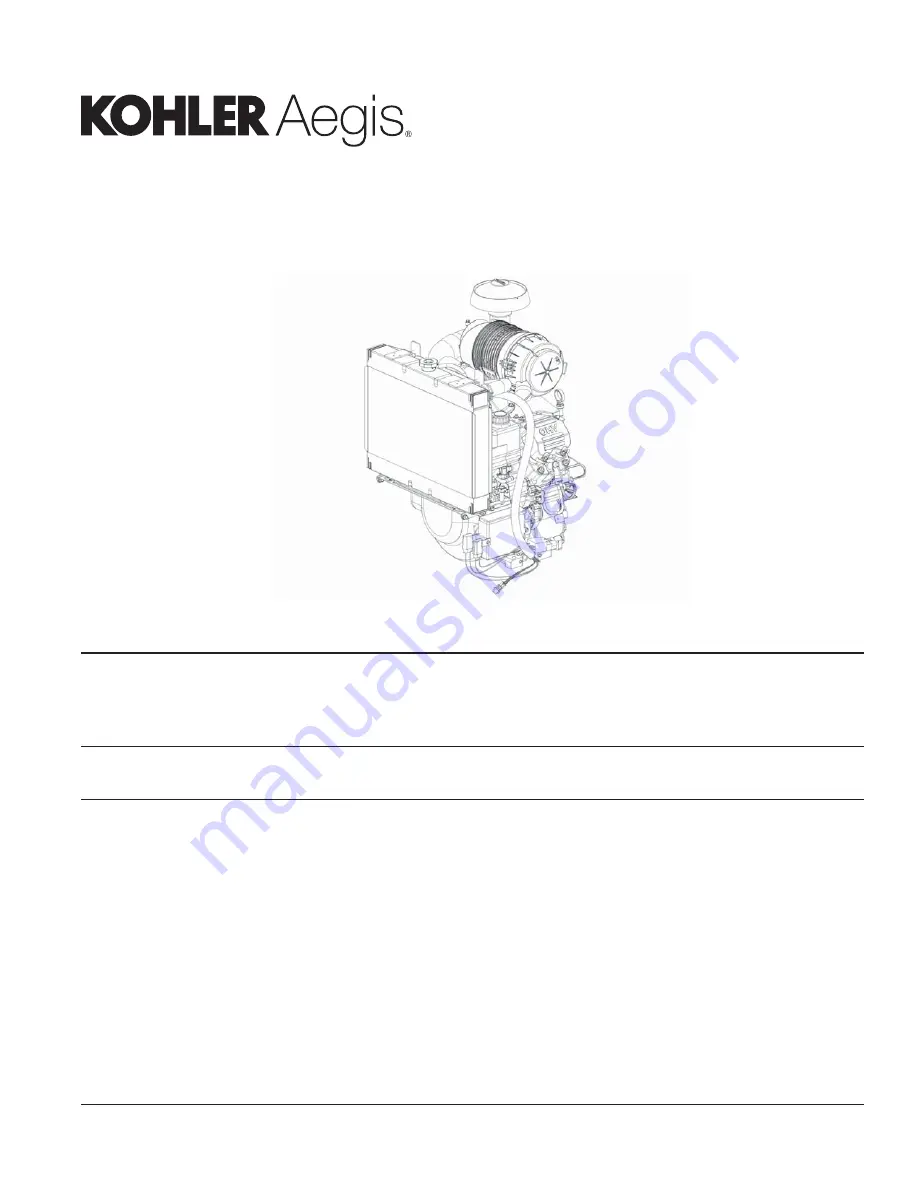
LH775
Service Manual
IMPORTANT: Read all safety precautions and instructions carefully before operating equipment. Refer to operating
instruction of equipment that this engine powers.
Ensure engine is stopped and level before performing any maintenance or service.
2
Safety
3
Maintenance
5
Speci
fi
cations
11
Tools and Aids
14
Troubleshooting
18
Air Cleaner/Intake
19
Electronic Fuel Injection (EFI) System
45
Lubrication System
47
Electrical System
51
Starter System
55
Cooling System
59
Disassembly/Inspection and Service
75
Reassembly
66 690 07 Rev. --
KohlerEngines.com
1