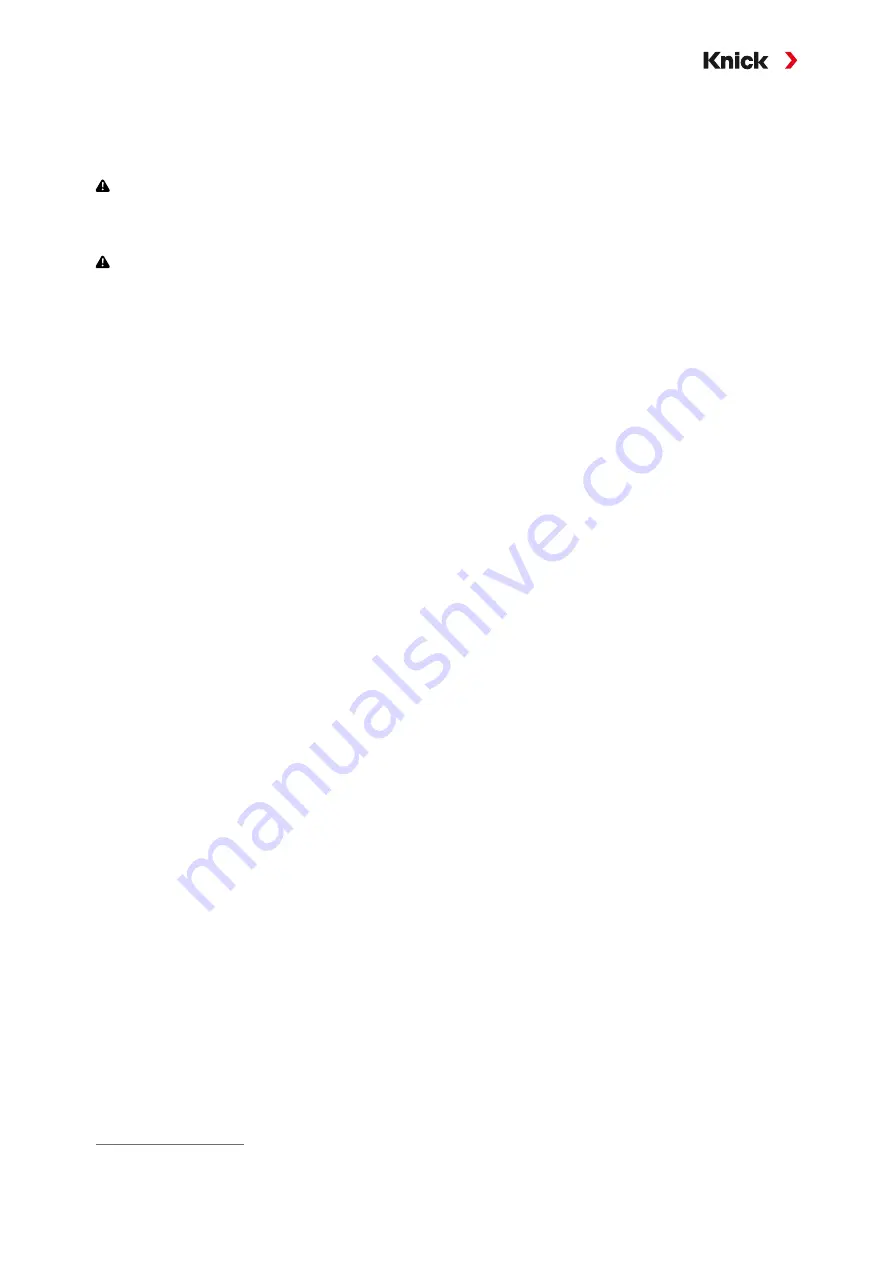
SensoGate WA131MH
39
8 Removal from Operation
8.1 Retractable Fitting: Removal
WARNING! Risk of explosion from mechanically generated sparks when used in explosive at-
mospheres.
Take measures to prevent sparking. Follow the safety instructions.
Operation in Explosive Atmospheres, p. 8
WARNING! Process or rinse medium, possibly containing hazardous substances, can escape
from the SensoGate WA131MH or the process port.
Follow the safety instructions.
01.
Depressurize the process.
02.
Move the SensoGate WA131MH into the SERVICE position.
Moving into the SERVICE Position, p. 24
03.
Remove the outlet hose.
04.
Optional: Remove the inlet hose
1)
.
05.
Optional: Remove installed safety accessories (e.g., ZU0818 retainer clamp).
06.
Loosen the process connection.
07.
Remove the SensoGate WA131MH from the customer’s process port.
08.
Close off the process port appropriately.
8.2 Returns
If required, send the SensoGate WA131MH in a clean condition and securely packed to Knick
Elektronische Messgeräte GmbH & Co. KG.
If the SensoGate WA131MH has been in contact with hazardous substances, it must be decontaminated/
disinfected prior to being shipped. The consignment must always be accompanied by a corresponding
return form to prevent service employees being exposed to potential hazards.
Further information can be found at www.knick.de.
8.3 Disposal
The local codes and regulations must be observed when disposing of the product.
The SensoGate WA131MH can contain various materials, depending on the version concerned.
1)
Availability is dependent on the ordered version.