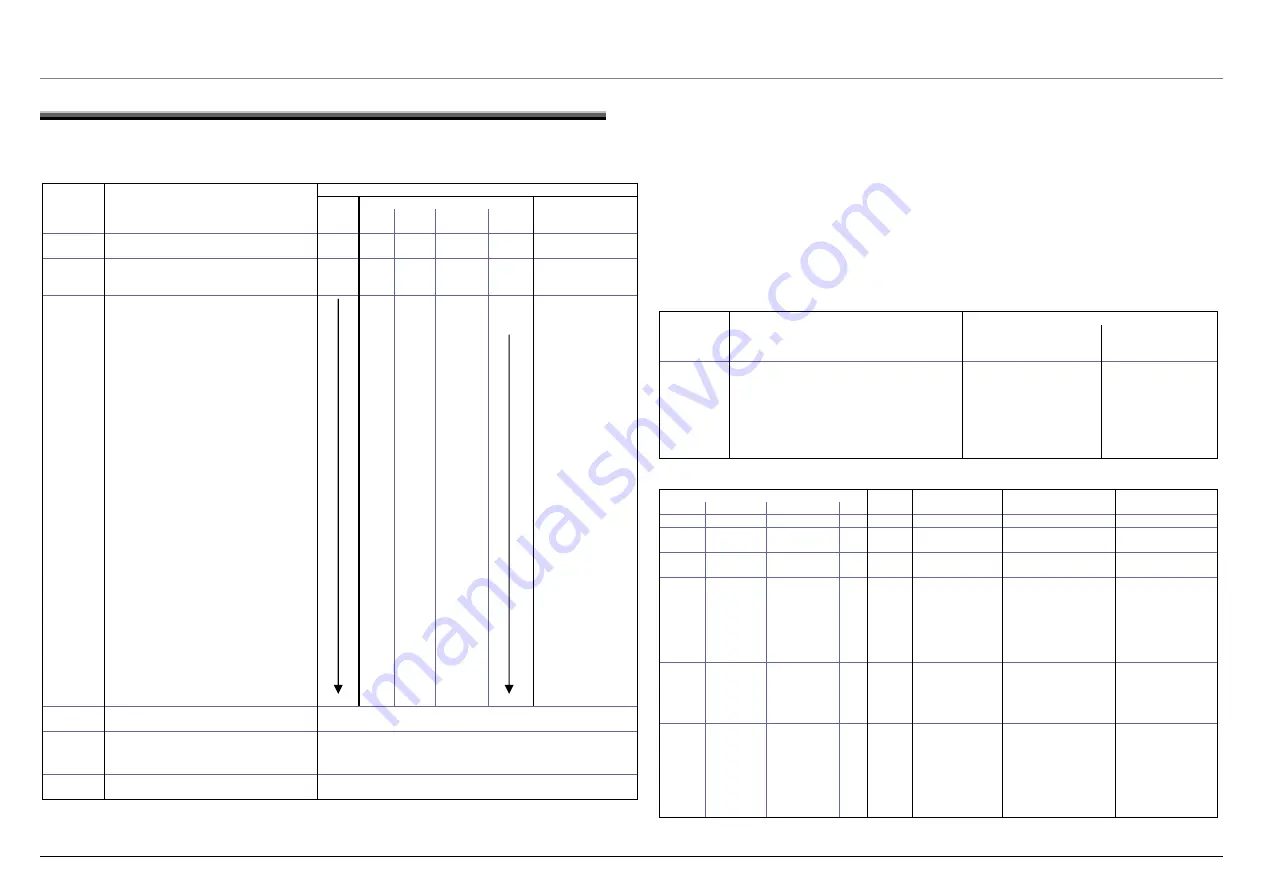
6 FAULT
DIAGNOSTICS
2. S
c
Obs
c
Display
ele ting the test program
erve orrect method for setting program selector!
LEDs(Indicator)
y Cupboard
dry
End
Display
Button
LED Drying Iron
dr
Activ
e
men
ate t st Program selector switch to OFF position
Off
u:
One time last error
Turn the appliance on by pressing the Start
and Delicates button simultaneously and
Start is
flashing
turning the selector switch (either direction). quick
Activ
e
is
flashing
quick
ate t st In test menu set program selector switch to
program:
a test program:
Read out error storage
1st position to the right
2nd position to the right
Test program for safety test
3rd position to the right
Display test (LED/LCD)
4th position to the right
Control elements test
5th position to the right
Consumer test
6th position to the right
Laundry resistance measurement test
7th position to the right
Demo program
8th position to the right
Changeover 10A/16A (208V/240V)
operation
1st position to the left
Automatic end-of-line program
Start test
program:
Press START button
LED Start is illuminating
Abort test
program:
Adjust program selector switch or press
START button
LED Start is flashing
Switch off appliance
Leave test
program:
Switch off appliance
t on one side with the phase ) switch on. The test must be done using
For this propose the following Inspection Process is adaptive
Connect app
ine
tton Extra dry
4.
The current consumption on tester (Motor and Heater Elements must be switch on)
1. Safety test
For the safety test must Heater Element (at leas
different current method.
1.
liance with tester and power l
2.
Choose program with Heater; example Co
3. Program
start
The Maximal Different Current must be under allowable limit while checking procedures is running.
Annotation:
Depending on used tester (for example Meratester 5-f) can be necessary inspection process with 180° twisted power
connector ones again do.
Inspection Process must be done with cold Appliance to prevent that Heater Element is switch on.
2.1 Fault display
Display
Test: Sequence:
Standard Indicator
Display
E: failure number
C: numbers of failure
Last fault
- the last fault is displayed at first
Start and finished LED’s are E:XX is displayed
flashing
Fault history - after further operation the START button, the
content of the error register (of the last 8 cycles)
is indicated
LED Start is illuminating
Status-LED’s: failure code
E:XX is displayed
C:XX is displayed
Or blank if no failure
Last fault
- if all register were indicated, the first fault is
Filter- outflow hose LEDs
E:XX is displayed
displayed again by operation the START button are flashing
C:XX is displayed
Or blank if no failure
LEDs (Indicator)
Drying
Iron dry
Cupboard dry End
description
cause
Display
Fault / fault
Remarks, possible
Results
No
fault
is
flashing
E:11
Fluffing level 1
- Fluff filter, container
or air routes blocked
- Clean components
and air routes
is flashing
E:12
Fluffing level 2
- Fluff filter, container
or air routes blocked
- Clean components
and air routes
is
flashing
is flashing
E:13
Maximum drying
time exceeded
- Heater or heater
control damaged
- Bimetal switch was
triggered
- Laundry load (to
heavy or to wet)
- Check heating
circuit and bimetal
switch, replace
damaged parts
- Reduce laundry
load or select
adequate program
is
fl
ashing
is flashing
E:15
Fault in heating
circuit
- Excess temperature
of the heater is
detected
- Check air routes,
heater function and
heater control;
replace damaged
parts
is
fl
ashing
is flashing is flashing
E:17
Door-NTC fault
(TD)
- Damaged sensor
- Short circuit in sensor
wire
- Open sensor circuit
- Control interpretation
fault
- Check wires and
connectors, replace
damaged parts
- Short circuits and
breaks are detected
by control after
switch-on
702_58300000121945_ara_en_a
Page 17 of 21