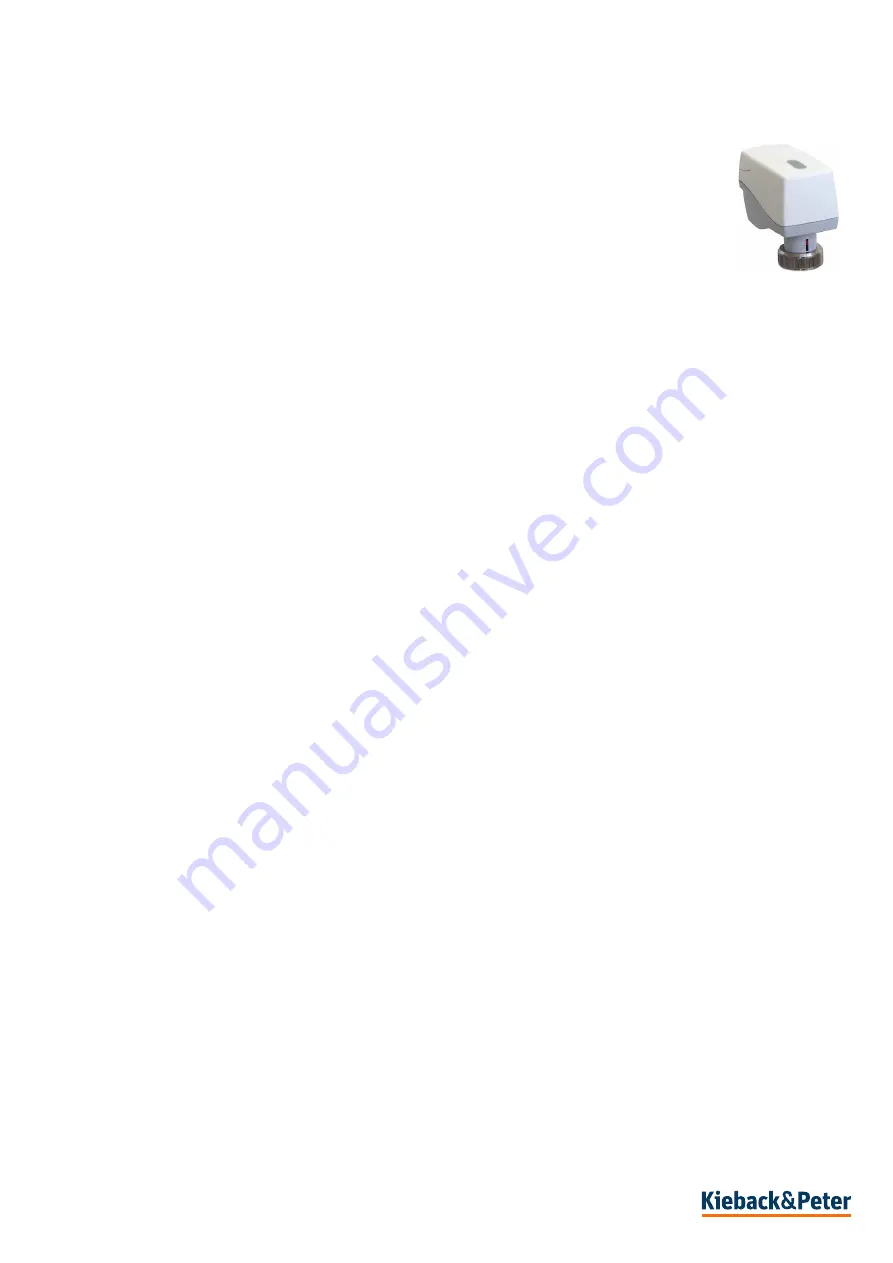
Page 3 / 14
MD15-C, MD15-HR, MD15-DA
Product Description
3.09-20.115-01-EN | 2019-08-12
Q
MD15-C, MD15-HR and MD15-DA Actuators
Technical Data
MD15-DA
Small actuator for radiator valves that were
manufactured by Danfoss of the RA-N, RA-FN
or RA-U series
MD15-C
Small actuator for valve series D15xx and
W15xx (manufacturer Controlli, series VST and
VMT) that were discontinued in 2003
MD15-HR
Small actuator for valve series R15/x and
RW15/x (manufacturer Hora, series 216Z and
316Z) that were discontinued in 11-2015
Nominal voltage
AC 24 V ± 10%; 50/60 Hz; DC 24 V ± 10%
Power consumption Dimensioning: 3.7 VA (AC 24 V); 1.7 W (DC 24 V)
Nominal: 2.5 VA (AC 24 V); 1.3 W (DC 24 V)
Switch-on current
Max. 10 A for a short time
Control
Three-point signal (open/stop/close), two-point signal (open/close) or
Continuous control DC 0(2)..10 V, < 0.5 mA, invertible
Connection
Built-in cable
1.5 m; 3 x 0.5 mm
2
Motor switch-off
Actuator spindle: when extending = load-dependent, when retracting =
path-dependent
Display
LED display for operating voltage and status
Actuating noise
< 28 dB (A)
Positioning stroke
MD15-C 6 mm; MD15-HR 9 mm and MD15-DA 3 mm
Positioning time
22 s/mm
Positioning force
MD15-C and MD15-HR: nominal 200 N
MD15-DA: nominal 100 N
Position indicator
Stroke range scale
Manual adjustment
Only when disconnected from the power supply
Socket for hexagon key under the cover nipple on the actuator cover, 4 mm
key socket
Valve exercise
Can be switched on
Permissible medium
temperature in the
valve
0..120° C
Ambient temperature 0..50° C
Ambient humidity
During operation: 0..85% r.h., non-condensing
Out of operation: 0..85% r.h., non-condensing
Overvoltage category III
Level of contamina-
tion
2
Degree of protection IP54 only with the appropriate installation position (see page 12)
Protection class
III