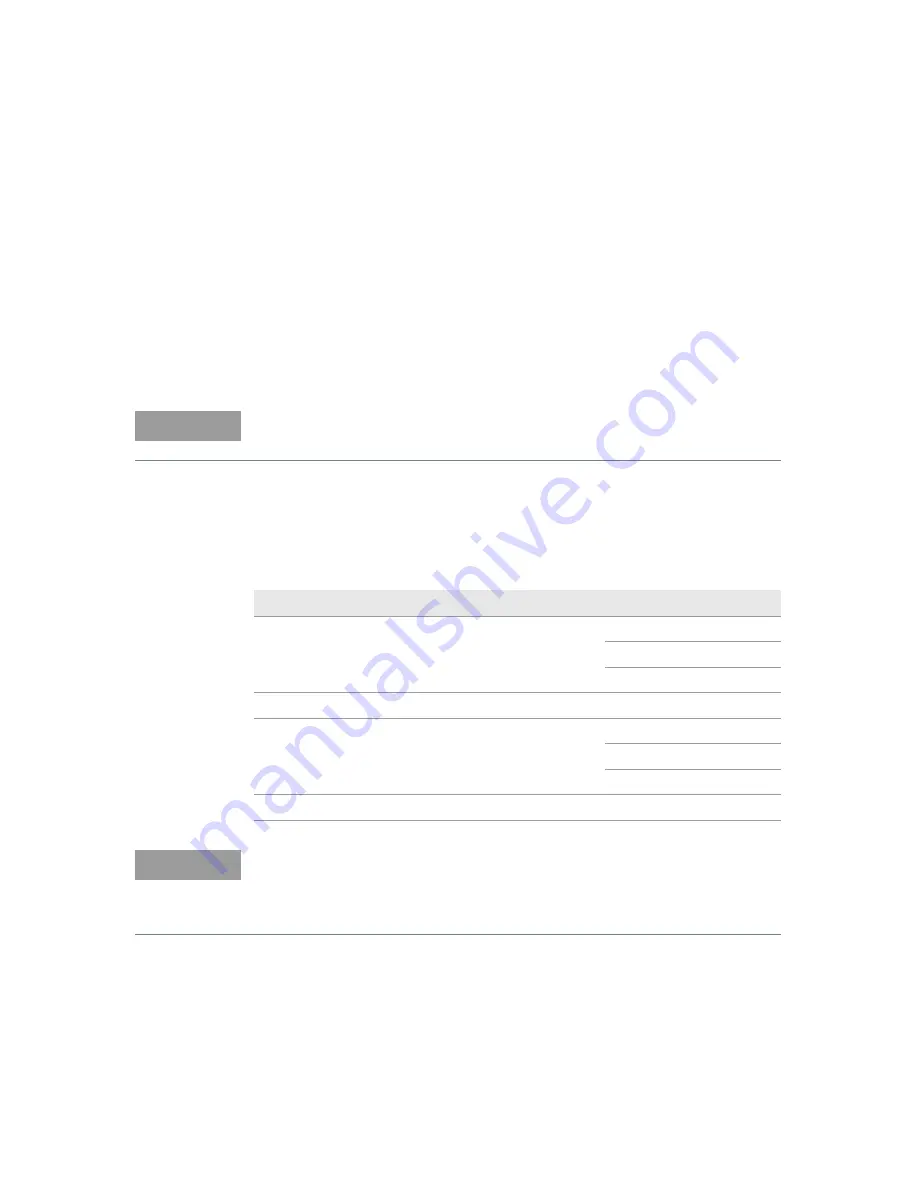
Calibration Procedures
1
Keysight E3632A Service Guide
43
General Calibration/Adjustment Procedure
The calibration procedures from the front panel are described in this section. For
voltage calibration, disconnect all loads from the power supply and connect a
DVM across the output terminals. For current calibration, disconnect all loads
from the power supply, connect an appropriate current monitoring resistor
(0.01
Ω
) across the output terminals, and connect a DVM across the terminals of
the monitoring resistor.
The following table shows calibration parameters and points which should be
used to calibrate the output voltage and current.
Table 1-4
Parameters for calibration
NOTE
The power supply should be calibrated after 1-hour warm-up with no load
connected.
Calibration parameter
Voltage/current
Calibration point mnemonic
CAL SETUP 1
Voltage
V LO
V MI
V HI
CAL SETUP 2
OVP
None
CAL SETUP 3
Current
I LO
I MI
I HI
CAL SETUP 4
OCP
None
NOTE
– You can terminate any CAL SETUP without changing its calibration constants
by turning off power.
– Perform the voltage calibration prior to the OVP calibration and the current
calibration prior to the OCP calibration.
Summary of Contents for E3632A
Page 1: ...Keysight E3632A DC Power Supply Service Guide ...
Page 12: ...Keysight E3631A Service Guide 14 THIS PAGE HAS BEEN INTENTIONALLY LEFT BLANK ...
Page 14: ...16 Keysight E3631A Service Guide THIS PAGE HAS BEEN INTENTIONALLY LEFT BLANK ...
Page 16: ...18 Keysight E3631A Service Guide THIS PAGE HAS BEEN INTENTIONALLY LEFT BLANK ...
Page 68: ...2 Service 70 Keysight E3632A Service Guide ...
Page 70: ...72 Keysight E3632A Service Guide Component locator diagram for the front panel top ...