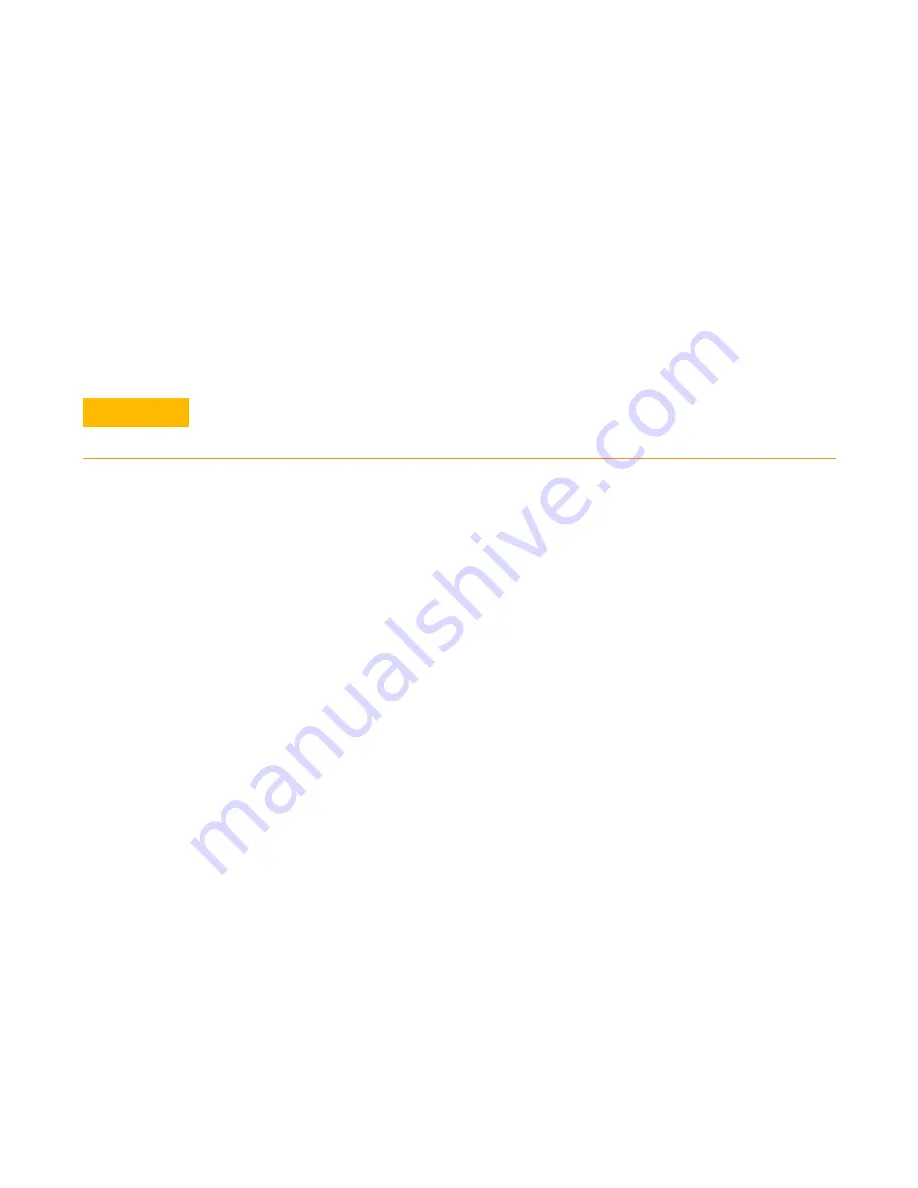
3
Making Connections
30
Keysight V281C/D and W281C/D Operating and Service Manual
Making a Connection
Connection procedure
1
Ground yourself and all devices (wear a grounded wrist strap and work on an antistatic mat).
2
Visually inspect the connectors (refer to “Visual Inspection” on page 3-2).
3
If necessary, clean the connectors (refer to “Cleaning Connectors” on page 3-8).
4
Carefully align the connectors. The male connector center pin must slip concentrically into the
contact fingers of the female connector (see Figure 3-5 and Figure 3-6).
5
Push the connectors straight together. Do not twist or screw them together. As the center
conductors mate, there is usually a slight resistance.
6
Initial tightening can be done by hand, or with a 6 mm open-end wrench. Tighten until “snug”
or where the connectors are first making contact. The preliminary connection is tight enough
when the mating plane surfaces make uniform, light contact.
Do not overtighten
this
connection.
At this point, all you want is for the outer conductors to make gentle contact on both mating
surfaces. Use very light finger pressure (no more than 2 in-lbs of torque).
7
Relieve any side pressure on the connection from long or heavy devices or cables. This assures
consistent torque (refer to
Connecting waveguides
The waveguide mating planes are precision flanges that you must
carefully
screw together. Flat
contact between the connectors at
all
points on their mating plane surface is required for a good
connection. Inspect the mating surfaces for any gaps, or any condition that will not allow the
surfaces to lay flat.
Always
connect waveguide in the same flange orientation using an X pattern
(for equal compression).
CAUTION
Do
not
twist one connector into the other (like inserting a light bulb). This happens when
you turn the device body, rather than the connector nut. Major
damage
to the center
conductor and the outer conductor can occur if the device body is twisted.