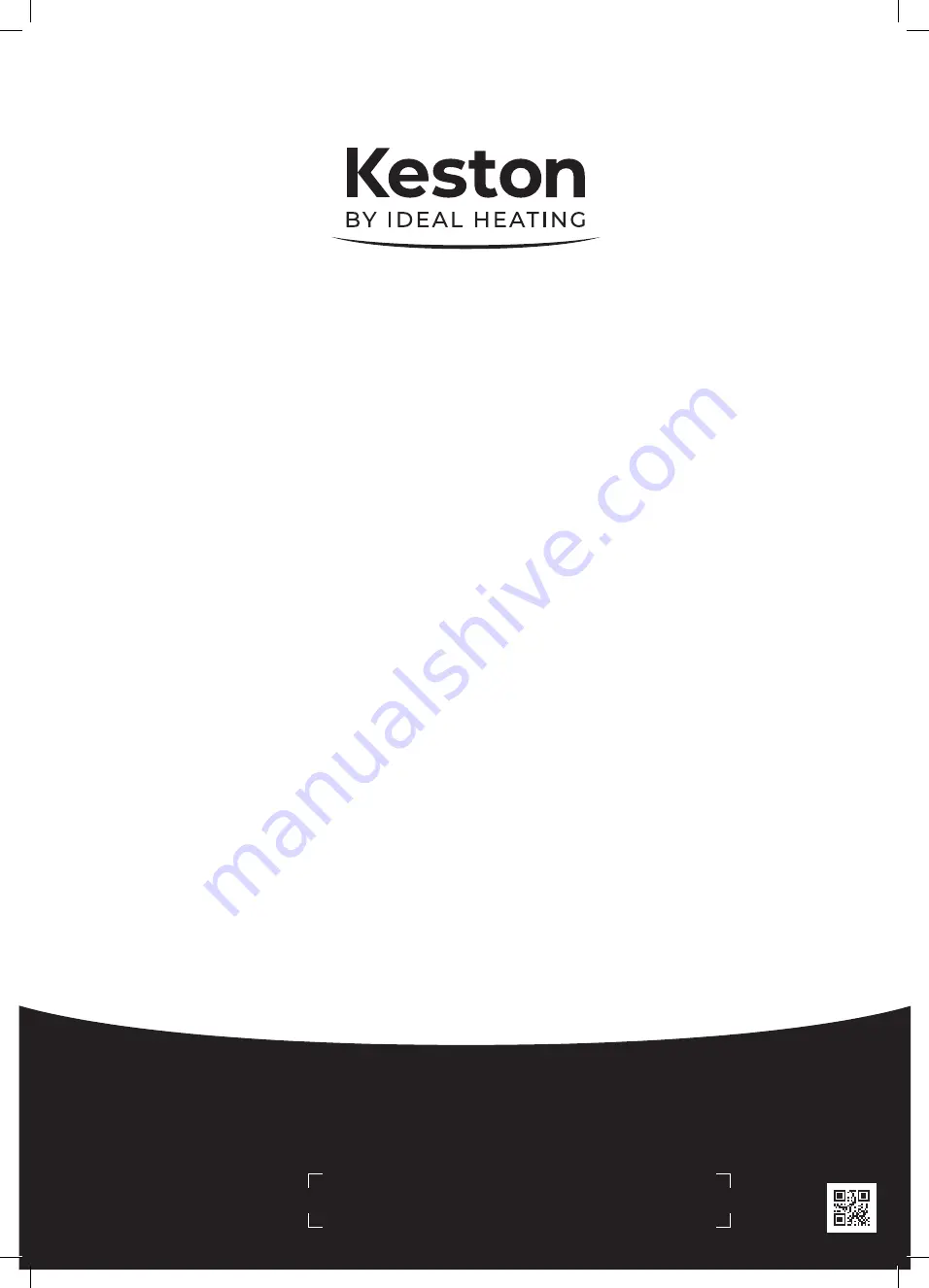
When replacing any part on this appliance, use only spare parts that you can be assured conform to the safety and
performance
specification that we require. Do not use reconditioned or copy parts that have not been clearly authorised by
Keston.
For the very latest copy of literature for specification and maintenance practices visit our website www.keston.co.uk
where you can download the relevant information in PDF format.
August 2020
UIN 220446 A01
INSTALLATION
& SERVICING
HEAT 2
45 55 45P 55P
Summary of Contents for HEAT 2 45
Page 4: ...4 Installation Servicing ...
Page 78: ...78 Installation Servicing NOTES ...