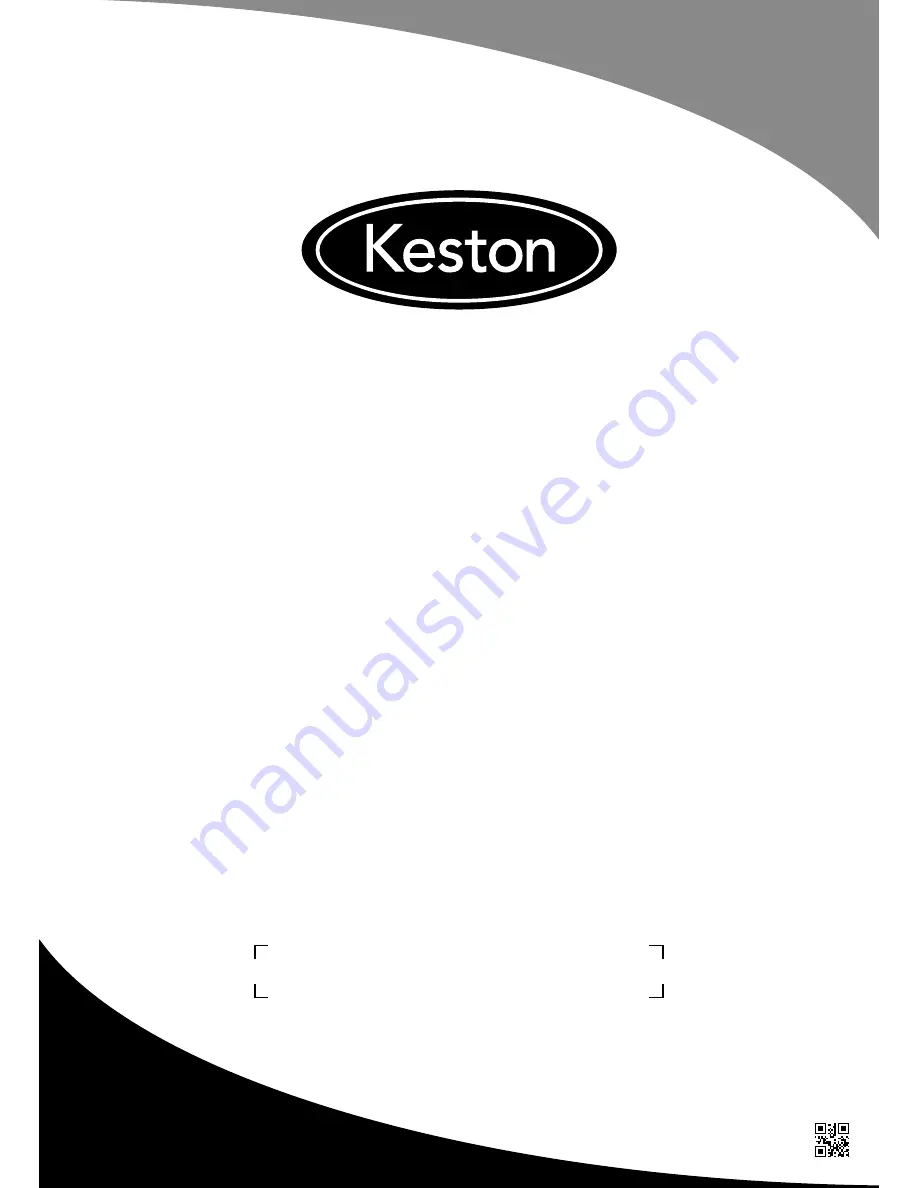
July 2016
UIN 215348 A01
Combi C30 & C35
When replacing any part on this appliance, use only spare parts that you can be
assured conform to the safety and performance specification that we require.
Do not use reconditioned or copy parts that have not been clearly authorised by Keston.
For the very latest copy of literature for specification and maintenance practices visit our website
www.keston.co.uk where you can download the relevant information in PDF format.
FAN POWERED HIGH EFFICIENCY
MODULATING DOMESTIC CONDENSING
GAS COMBINATION BOILER
Installation and Servicing Instructions