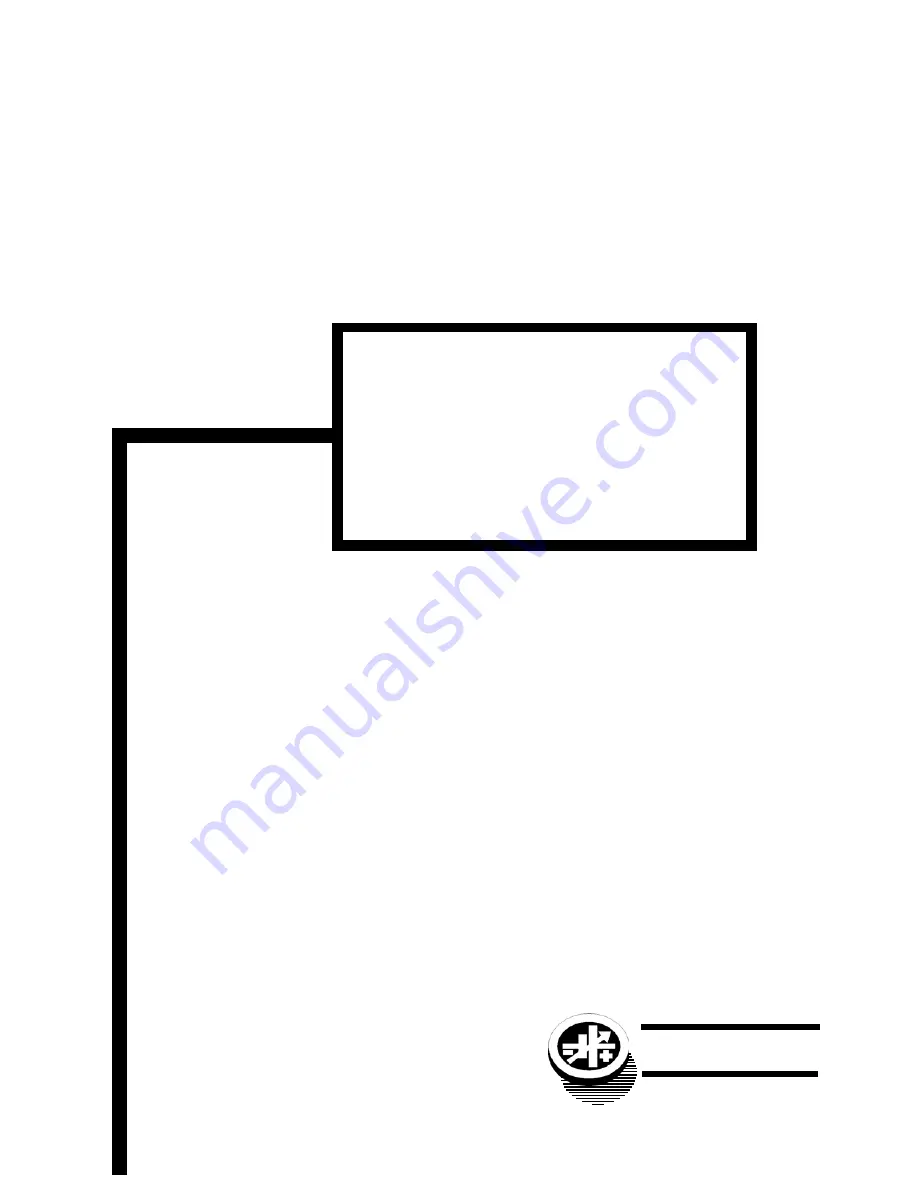
IMPORTANT NOTES:
1)
This manual is valid for the following Model and associated serial numbers:
MODEL
SERIAL NO.
REV. NO.
2)
A Change Page may be included at the end of the manual. All applicable changes and
revision number changes are documented with reference to the equipment serial num-
bers. Before using this Instruction Manual, check your equipment serial number to identify
your model. If in doubt, contact your nearest Kepco Representative, or the Kepco Docu-
mentation Office in New York, (718) 461-7000, requesting the correct revision for your
particular model and serial number.
3)
The contents of this manual are protected by copyright. Reproduction of any part can be
made only with the specific written permission of Kepco, Inc.
Data subject to change without notice.
KEPCO
®
THE POWER SUPPLIER™
MODEL
OPERATOR’S MANUAL
KEPCO INC.
KEPCO, INC.
z
131-38 SANFORD AVENUE
z
FLUSHING, NY. 11355 U.S.A.
z
TEL (718) 461-7000
z
FAX (718) 767-1102
email: [email protected]
z
World Wide Web: http://www.kepcopower.com
An ISO 9001 Company.
©2012, KEPCO, INC
P/N 243-0850b
HSM SERIES
1000 AND 1500 WATT SWITCHING POWER SUPPLY
VOLTAGE/CURRENT-STABILIZED DC SOURCE
HSM SERIES
POWER SUPPLY
Summary of Contents for HSM 12-84
Page 2: ......
Page 5: ......
Page 6: ...iii Blank iv HSMSERIES OPR 052912 FIGURE 1 1 HSM SERIES POWER SUPPLY...
Page 10: ...1 4 HSMSERIES OPR 052912 FIGURE 1 3 OUTLINE DRAWING...