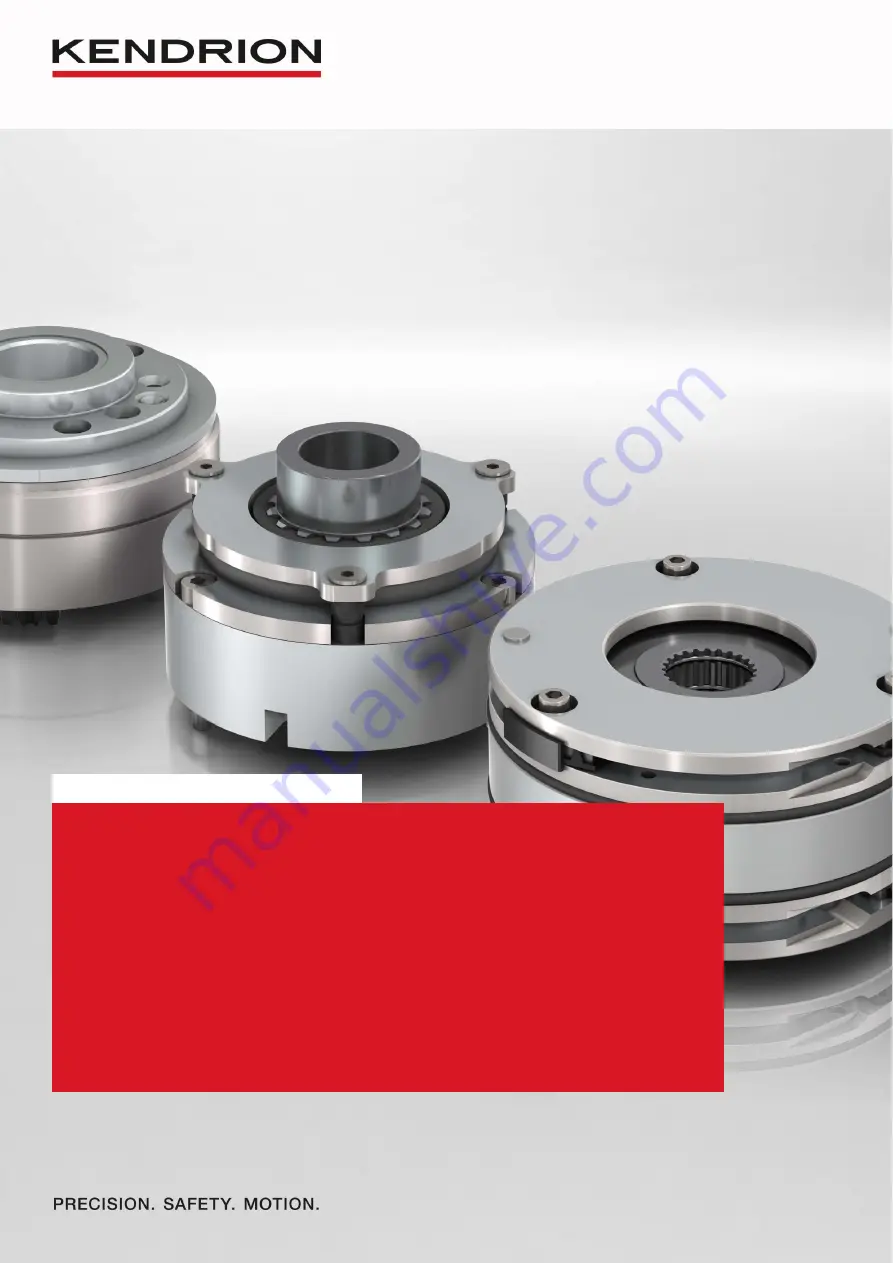
KENDRION
INDUSTRIAL BRAKES
EEX Line
Spring-applied single-disc brake
Operating Instructions 76..G..B00
Types: 76 14G10B00 76 16G10B00 76 24G10B00 76 26G10B00
76 14G11B00 7616G11B00 76 24G11B00 76 26G11B00
76 14G13B00 76 16G13B00 76 24G13B00 76 26G13B00
76 14G16B00 76 16G16B00 76 24G16B00 76 26G16B00
76 14G19B00 76 16G19B00 76 24G19B00 76 26G19B00
76 14G24B00 76 16G24B00 76 24G24B00 76 26G24B00