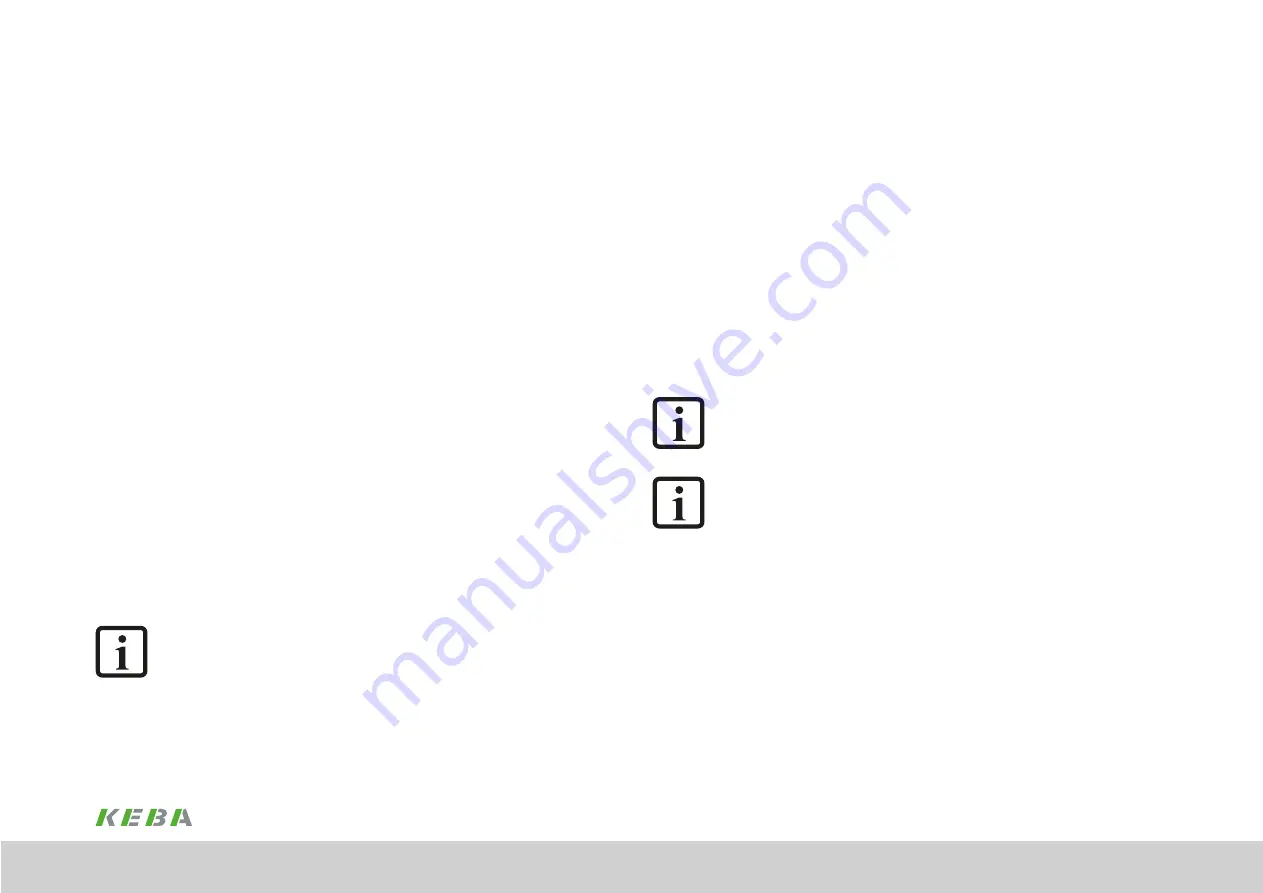
3
Mechanical installation
3.1 Notes for installation
During the installation work
it is imperative you avoid ...
− Drill chippings, screws or other foreign objects falling into the device
− Moisture entering the device
Switch cabinet
− The device is designed only for installation in a stationary switch cabinet. The switch cabinet
must as a minimum provide the degree of protection IP4X. According to EN ISO 13849-2 the
switch cabinet must have degree of protection IP54 or higher when using the safety functions
(STO and SBC) in the axis controller.
Environment
− The axis controllers must not be installed in areas where they would be permanently exposed
to vibration. You will find more information in the appendix A.4
Soiling
− Maximum pollution degree 2 in accordance with EN 60664-1. You will find further information
about ambient conditions in the appendix A.4
Effective EMC installation
− To obtain the best result for effective EMC installation you should use a conductive, well-
earthed, chromated or galvanised backing plate.
− If backing plates are varnished, remove the coating from the contact area! The devices
themselves have a chromated zinc frame.
NOTE:
If the axis controller is installed in the axis group it is imperative the operation
manuals for the other devices (supply unit, controller, etc.) are also followed.
3.1.1
Order and arrangement
The following basic guidelines apply to the arrangement and installation of the axis
controller or supply unit:
Butt mounting and alignment
y
The devices can be mounted directly beside each other without any spacing.
They are fastened to the backing plate using screw joints.
y
The 24 V DC control supply must be provided by an external power supply
unit. All devices in the axis group are connected together using the 24 V
busbars. Given the same cooling concept, these connections can be made
without additional compensation measures in relation to device depth.
y
DC link busbars are available for the power supply.
y
The devices must be mounted in the stipulated order and one against the
other, see Figure 3.1. A different order is not allowed, as otherwise there
will be problems with the busbars and the thermal interaction between the
devices.
NOTE:
A maximum of 8 communication bus users can be connected to and operated
on a supply unit. A communication group is allowed to consist of a maximum
of 9 bus users.
NOTE:
In the overall axis group, the following DC link capacitance, referred to the total
active power, must be provided:
− 3 x 400 V: ≥ 100 μF/kW
− 3 x 480 V: ≥ 85 μF/kW
− 3 x 230 V: ≥ 170 μF/kW
− 1 x 230 V: ≥ 900 μF/kW
The DC link capacitance is determined by adding together the capacitances
of the supply unit, capacitance module and DC-supplied axis controllers
(see Table A.1). The root mean square of the active power for a load cycle is
defined as the total active power.
15
1 Mechanical installation
Operation Manual KeDrive D3-DA BG3 and BG4
1804.200B.1-01 Date: 03/2023
Mechanical installation
Summary of Contents for KeDrive D3-DA BG3
Page 14: ...14 1 Safety Operation Manual KeDrive D3 DA BG3 and BG4 1804 200B 1 01 Date 03 2023 Safety...
Page 24: ...24 1 Operation Manual KeDrive D3 DA BG3 and BG4 1804 200B 1 01 Date 03 2023...
Page 66: ...66 1 Operation Manual KeDrive D3 DA BG3 and BG4 1804 200B 1 01 Date 03 2023...
Page 78: ...78 1 Appendix Operation Manual KeDrive D3 DA BG3 and BG4 1804 200B 1 01 Date 03 2023 Appendix...
Page 82: ...82 1 Glossary Operation Manual KeDrive D3 DA BG3 and BG4 1804 200B 1 01 Date 03 2023 Glossary...
Page 83: ...83 1 Operation Manual KeDrive D3 DA BG3 and BG4 1804 200B 1 01 Date 03 2023...