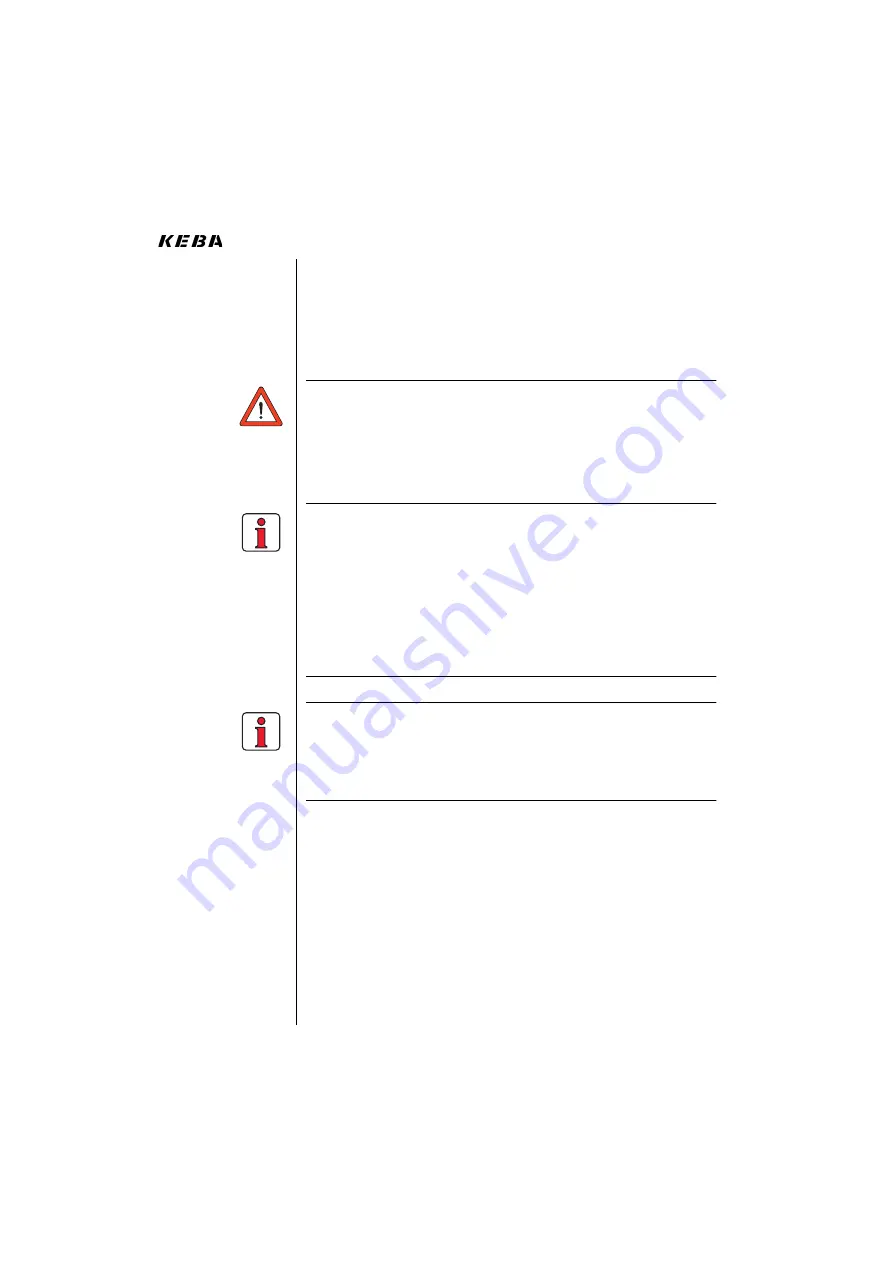
3-28
Operating Instructions CDF3000
3 Installation
3.10.9 Function test
STO
The applied control signals "ISDSH" and "ENPO" must always be
checked by the operator or a higher-level control for plausibility to the
feedback (RSH).
The occurrence of an implausible status is a sign of a system fault (instal-
lation or servocontroller). In this case the drive must be switched off and
the fault rectified.
Attention:
The "STO" (Safe Torque Off) function must generally be
checked for correct functionality after:
• initial commissioning
• any modification of the system wiring
replacing one or several appliances in the system.
Note:
There is no protection against unexpected restarting after re-
establishing the electrical power supply in the illustrated
example circuit, unless an external circuit is used. If, on the
restoration of the supply of power, ENPO and ISDSH are
high (see truth table) and Autostart is programmed, the axis
may start, particularly in the case the control electronics are sup-
plied with 24V from an external source in event of power failure.
The connected safety circuit on the machine must ensure that the
servocontroller (the SRP/CS) can attain and maintain the safe
state of the machine.
Note:
Where the switch and drive controller are installed in different
locations, it must be ensured that the cables from NC contact
1 to ENPO (STO) and from NC contact 2 to ISDSH (STO) are
wired separately, or that possible faults are ruled out by using
a protective tube for example.
In order to cancel the STO safety function and deactivate the restart
inhibit, the ISDSH signal must be set to High before the ENPO signal, or
simultaneously with it.
Summary of Contents for CDF3000
Page 1: ...Positioning controller Rated current 8 A Power supply 24 48 V DC CDF3000 Operation Manual...
Page 12: ...Operating Instructions CDF3000...
Page 16: ...1 4 Operating Instructions CDF3000 1 Safety...
Page 54: ...3 34 Operating Instructions CDF3000 3 Installation...
Page 78: ...4 24 Operating Instructions CDF3000 4 Commissioning...
Page 84: ...5 6 Operating Instructions CDF3000 5 Troubleshooting...