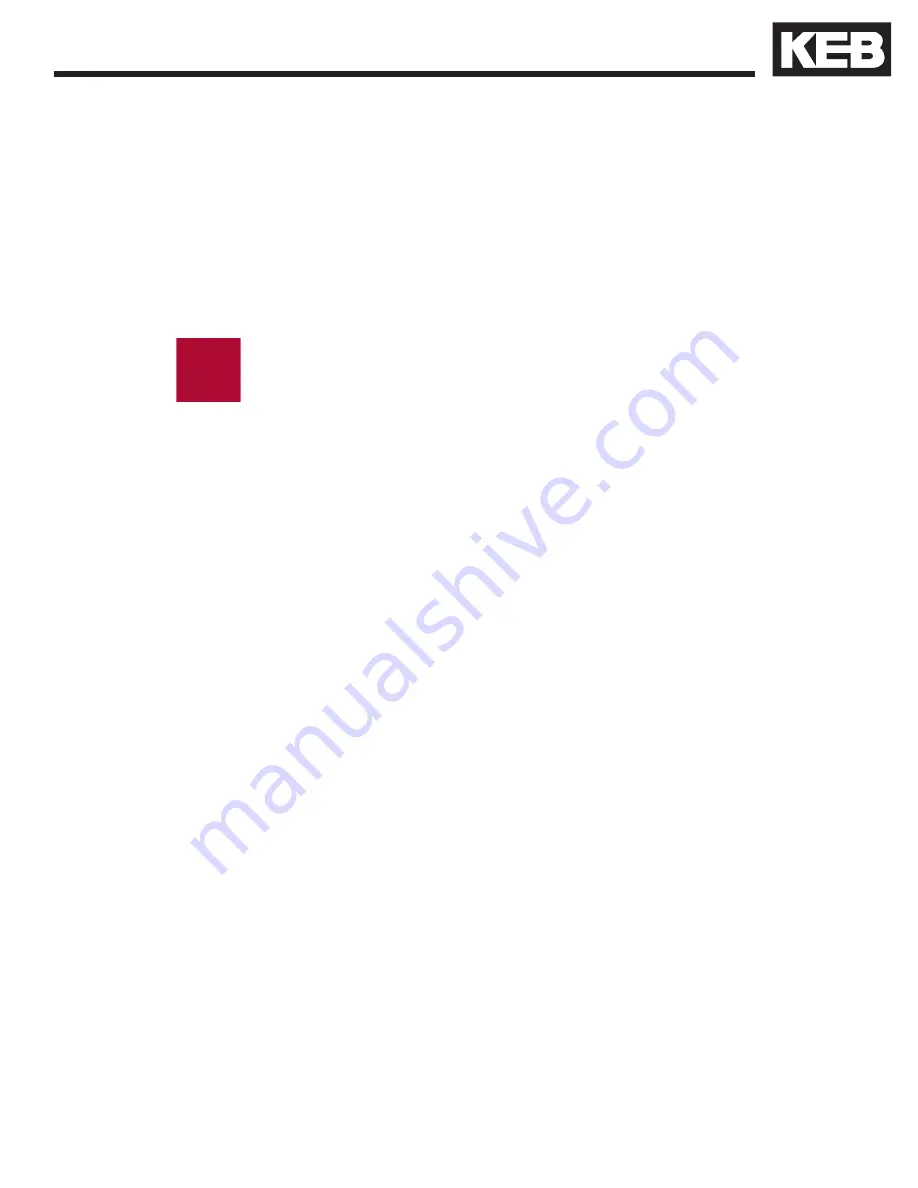
67
Hiperface - Encoder Connections
3.3.6 Hiperface
Encoder Interface X3A
The Hiperface encoder provides two differential analog channels for
incremental position and one serial data channel for communication
with the encoder. This serial data channel can provide the drive with the
absolute position of the motor as well as other operating data.
The analog cosine and sine wave signals of tracks A and B have a voltage
of 1 Vpp with an Offset of 2.5 V. This analog voltage is measured, and a
high-resolution position value is determined as a result. This high-resolution
position value is very important for good speed control of a gearless motor.
Therefore, it is absolutely necessary to ensure these signals are well
shielded! Noise on the analog signals resulting from breaks in the
shield or improper shield termination will result in vibration in the
motor and poor ride quality.
The internally stored ppr value is compared to the adjusted value in LE02. If
the two are not the same, the drive will trigger the ‘Error Encoder Interface’
fault. Refer to parameter LE12 for more information.
During start-up and then every 100 ms a request is transmitted to the
encoder and the absolute position is read out via serial communication.
This initial readout of the absolute position provides the drive with the
commutation angle for permanent magnet motors. On the very first
operation of a permanent magnet motor, it is necessary to synchronize the
encoder position to one of the pole pairs of the motor. See parameter LE06
for more information and section 5.10.
During normal operation, the difference between the internal absolute
position of the encoder and the measured position value in the drive is
compared. If the two deviate by more than 2.8 degrees, the drive will
trigger the ‘Error Encoder Interface’ fault. Refer to parameter LE12 for more
information.
If there is an excess length of cable (10 feet or less), it is OK to coil it into a
loop in the controller. Maintain a minimum diameter of 1 foot and keep the
cable at least 8 inches away from all high voltage power wires.
i
Summary of Contents for COMBIVERT F5
Page 1: ...COMBIVERT F5 ELEVATOR DRIVE Reference Manual Version 3 34 0F5LUB K334...
Page 203: ...203 LP Positioning Parameters LS02 LS01 LP03 LS02 LS01 LP03...
Page 347: ...Notes...
Page 348: ......