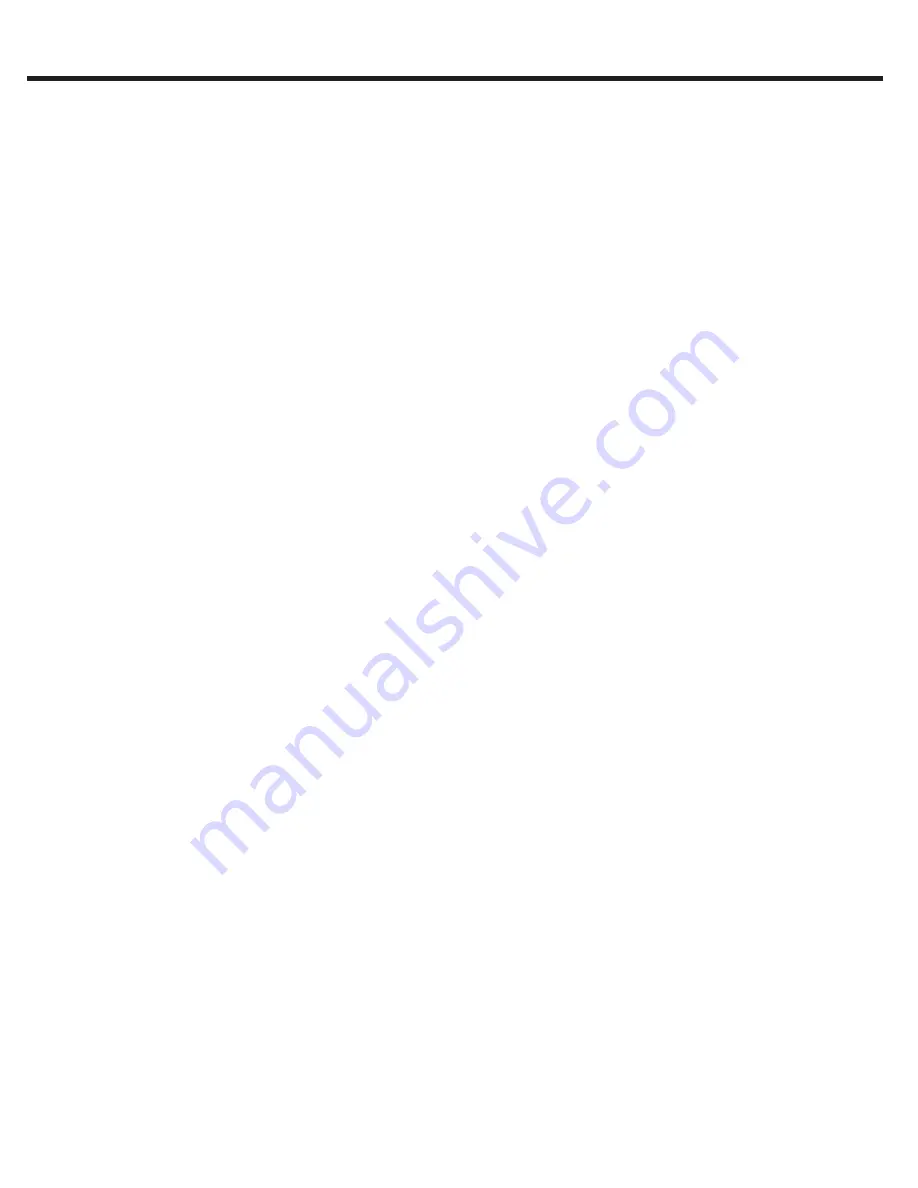
A line choke with a minimum 3% impedance is required for all 230 V
inverters 50hp (size 20) and greater. A line choke with a minimum 3%
impedance is required for all 480V inverters 100hp (size 23) and greater.
Alternately, an isolation transformer installed between the main line and
the elevator drive will satisfy the same requirement.
The line choke (or transformer) prevents nuisance errors and damage caused
by voltage spikes. Additionally, the use of a line choke will double the operational
lifetime of the DC bus capacitors in the unit. At the same time, the choke will
reduce the harmonic distortion of the line current from very high values of
80-100% THiD to around 45% THiD.
If lower values of line current distortion are required, contact KEB regarding
an applicable harmonic filter. With such a device, it is possible to reduce the
harmonic distortion below 8% THiD.
The F5 series elevator drive is UL approved as a solid-state motor overload
protection device. It is necessary to adjust the current trip level in the parameter
LM09 Electric Motor Protection Current (IM) or LM03 Motor Current (PM).
The function assumes the use of a non-ventilated motor. The function meets
the requirements outlined in VDE 0660 Part 104, UL508C section 42, NFPA
70 Article 430 part C. See the description for parameter LM08 Electric Motor
Protection for the trip characteristics.
A motor winding sensor can also be used for additional safety and the highest
level of protection. A normally closed contact (rating: 15V / 6mA) or a PTC
(positive temperature coefficient) resistor can be connected to the T1, and T2
terminals on the inverter. The thermal device should be connected as indicated
in Sections 2.7 and 2.8.
The F5 Elevator drive can also accept a KTY-type temperature sensor. This
sensor will give an analog temperature reading which can be displayed directly
in the diagnostic parameters. Additionally, a temperature level can be set to
give a warning signal to the controller to indicate the motor is becoming too
hot. This allows the controller to stop taking calls or adjust door open time in
an effort to reduce motor temp. A KTY sensor is standard on drive sizes with
R-housing and above or as an added option to drive sizes in housings H and
below.
The KTY device is a solid-state device. The approved model number is KTY-
84 (1000Ω at 100° C).
2.2.5 Line Chokes
2.2.6 Motor Thermal
Protection
Technical Information
14
Summary of Contents for COMBIVERT F5
Page 1: ...COMBIVERT F5 ELEVATOR DRIVE Reference Manual Version 3 34 0F5LUB K334...
Page 203: ...203 LP Positioning Parameters LS02 LS01 LP03 LS02 LS01 LP03...
Page 347: ...Notes...
Page 348: ......