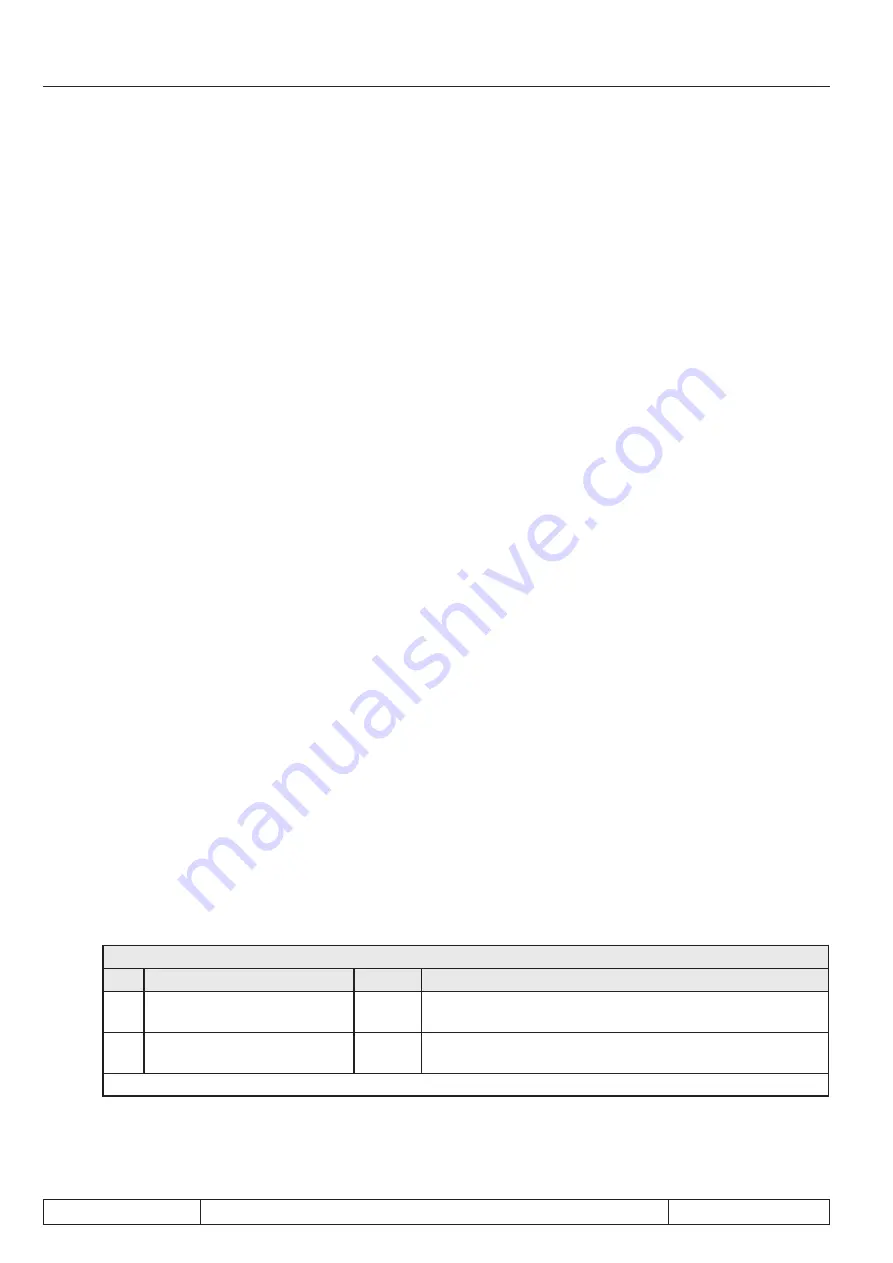
Page 7.5 - 32
COMBIVERT F5-A, -E, -H
© KEB, 2012-10
Motor data and controller adjustments of the asynchronous motor
Current control by measured / calculated currents
For the current control, either the measured currents or those calculated from the model can be used as actual
values. As a standard, the measured currents are used for control since only this assures direct control over
the real currents.
Using the calculated currents is advantageous only in high frequency applications: The delay (detection of the
actual current until the output of the voltages as response to the current measurement) is noticeable in these
applications. For control based on calculated current, this time is minimised.
Observer / motor model, observer effect / motor model
The observer causes an equalisation between the measured currents and the currents calculated from the
motor model. This is useful for some high frequency applications.
The
reciprocal of amplification of the observer is
set with the parameter "observer effect / motor model" (ds.23).
Voltage output for HF applications
At high output frequencies, the voltage vector must be calculated and output in a shorter time pattern. This is
possible only at 8 and 16 kHz. Important for high frequency applications
7.5.2.4.4
KP/KI Speed calc. ASCL (dS.14, 15) and speed PT1-time ASCL (dS.17)
The KP (dS.14) and the KI (dS.15) of the speed calculation controller are calculated automatically during the
identification of the motor parameters and may not be changed.
Only the parameter dS.17 "ASCL speed PT1 time" can be
adapted to a specific
application. In non-dynamic
applications, a higher PT1 time (up to 32ms for large motors) leads to a steadier calculated speed, without
degradation of the control characteristics of the drive.
In contrast, a lower speed frequently permits a more dynamic setting of the speed control parameters.
If parameter dS.17 "ASCL speed PT1 time" is changed, a previously conducted adaption of the speed controller
must be checked.
If the automatic calculation of the speed control parameters is used, it must be reactivated.
7.5.2.5 Special function: Rotor adaption
In speed control with speed feedback, the motor model can be used to adapt the rotor time constant. The rotor
time constant is dependent on the rotor resistance, among others. Due to the temperature change of the motor
rotor, the rotor
resistance can change significantly compared to the identified
value. This also changes the rotor
time constant. This change leads to a less accurate torque display and an inferior performance of the drive.
The rotor adaption compensates for the temperature deviations of the resistance. It is activated by bit 1 in pa-
rameters dS.04 "Flux-/Rotor adaption mode".
ds.04: Flux / rotor adaption mode
Bit
Meaning
Value
Explanation
1
Rotor adaption (ASM)
0: off
2: on
Activation of the rotor adaption
2
Rotor adaption/
store (ASM)
0: no
4: yes
Storage of the last rotor adaption value obtained during ope-
ration
further on next side
Summary of Contents for COMBIVERT F5-A
Page 1: ...KEB COMBIVERT F5 A E H 4 4 APPLICATION MANUAL Mat No Rev 00F5AEA K440 1A...
Page 2: ...Page 1 1 2 COMBIVERT F5 A E H KEB 2008 02 Table of contents...
Page 4: ...Page 1 1 4 COMBIVERT F5 A E H KEB 2008 02 Table of contents...
Page 14: ...Page 1 1 14 COMBIVERT F5 A E H KEB 2008 02 Table of contents...
Page 20: ...Page 2 1 6 COMBIVERT F5 A E H KEB 2012 10 Product Overview...
Page 28: ...Page 3 1 8 COMBIVERT F5 A E H KEB 2012 10 Control Units...
Page 34: ...Page 4 1 6 COMBIVERT F5 A E H KEB 2012 10 Fundamentals...
Page 40: ...Page 4 2 6 COMBIVERT F5 A E H KEB 2012 10 Password input...
Page 42: ...Page 5 1 2 COMBIVERT F5 A E H KEB 2012 10 Selection of Operating Mode...
Page 46: ...Page 5 1 6 COMBIVERT F5 A E H KEB 2012 10 Selection of Operating Mode...
Page 70: ...Page 6 2 20 COMBIVERT F5 A E H KEB 2012 10 Start up...
Page 140: ...Page 7 3 44 COMBIVERT F5 A E H KEB 2012 10 Digital in and outputs...
Page 238: ...Page 7 7 12 COMBIVERT F5 A E H KEB 2012 10 Speed control...
Page 254: ...Page 7 8 16 COMBIVERT F5 A E H KEB 2012 10 Torque display and limiting...
Page 260: ...Page 7 9 6 COMBIVERT F5 A E H KEB 2012 10 Torque control...
Page 292: ...Page 7 11 26 COMBIVERT F5 A E H KEB 2012 10 Speed measurement...
Page 432: ...Page 7 14 14 COMBIVERT F5 A E H KEB 2012 10 Parameter sets...
Page 466: ...Page 7 15 34 COMBIVERT F5 A E H KEB 2012 10 Special functions...
Page 478: ...Page 7 16 12 COMBIVERT F5 A E H KEB 2012 10 CP Parameter definition...
Page 488: ...Page 8 1 10 COMBIVERT F5 A E H KEB 2012 10 Troubleshooting...
Page 496: ...Page 9 1 8 COMBIVERT F5 A E H KEB 2012 10 General design...
Page 538: ...Page 11 1 28 COMBIVERT F5 A E H KEB 2012 10 Parameter...
Page 540: ...Page 12 1 2 COMBIVERT F5 A E H KEB 2008 02 Annex 12 1 1 Index 12 1 3...