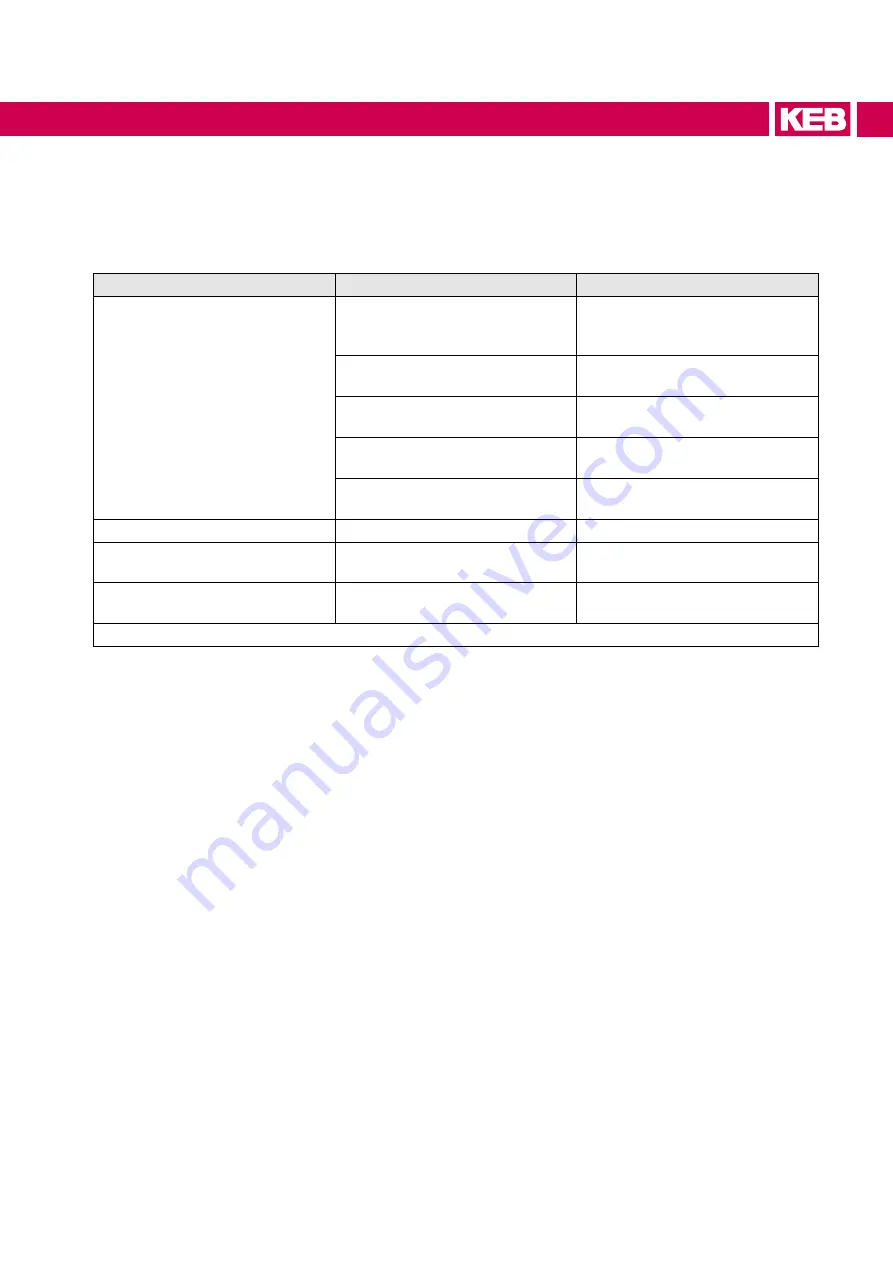
37
TrOUBLESHOOTING
8 Troubleshooting
The following table shows some causes and solutions of malfunctions during brake op-
eration. If this does not solve the problem or if other malfunctions occur, please contact
our service department.
Malfunction
cause
Measures
Brake does not close
Incorrect voltage
Only operate the brake with the
correct voltage
(=> Magnet marking )
Air gap too large, maximum air
gap reached
Replace the brake
Foreign objects between armature
and magnet
Remove the foreign objects
Magnet coil or connecting cable
defective
Replace the magnet
Excessive heating
Install a high-speed circuit breaker
(for example, KEB Powerbox)
No braking function
Friction surfaces contaminated
Replace the brake
Brake does not open
Foreign objects between hub and
armature
Remove the foreign objects
Brake engages with delay, long
delay time
Brake is switched on the AC side
Switch the brake on DC side
Table 9:
Troubleshooting