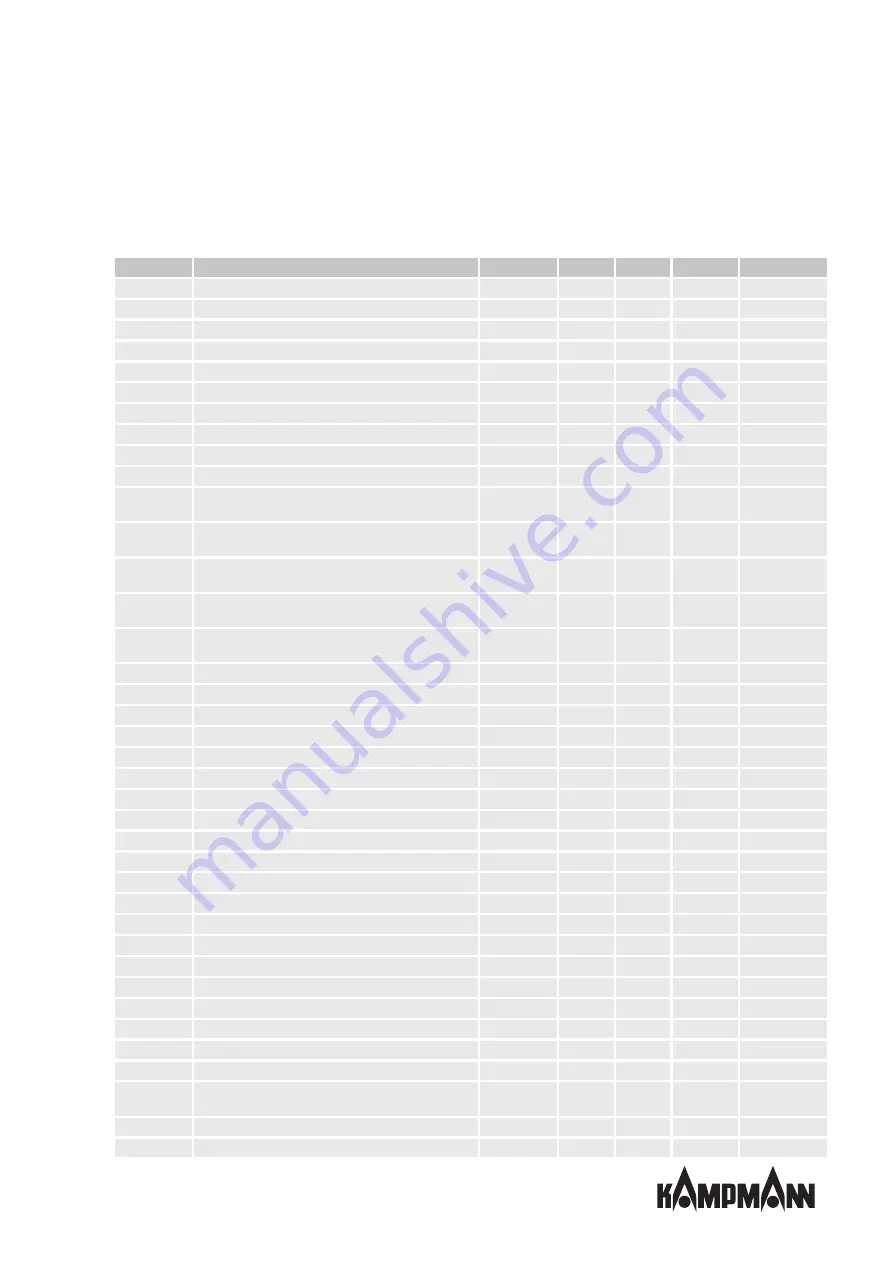
Venkon XL
Assembly, installation and operating instructions
59
11
List of KaControl parameters
11.1 Venkon XL parameter list
Parameter
Function
Standard
Min.
Max.
Unit
Venkon XL*
P000
Software version
24
0
255
-
24
P001
Basic setpoint for setpoint input ± 3K
22
8
32
°C
22
P002
Switch-on and switch-off hysteresis for valves
3
0
255
K/10
1
P003
Neutral zone in a 4-pipe system (only in automatic mode)
3
0
255
K/10
20
P004
Cooling without fan assistance (natural convection)
0
0
255
K/10
0
P005
Heating without fan assistance (natural convection)
5
0
255
K/10
0
P006
Fan On/Off hysteresis (only in ventilation mode)
5
0
255
K/10
5
P007
P-band, heating
20
0
100
K/10
25
P008
P-band, cooling
20
0
100
K/10
25
P009
Shifting to the basic setpoint for setpoint input ± 3K
3
0
10
C
3
P010
Contact sensor: temperature limit value to activate fan
stages 1 and 2 in heating mode
26
0
255
°C
26
P011
Contact sensor: temperature limit value to activate fan
stages 3 and 4 in heating mode
28
0
255
°C
28
P012
Contact sensor: temperature limit value to activate fan
stage 5 in heating mode
30
0
255
°C
30
P013
Contact sensor: hysteresis for limit temperatures
P010, P011, P012, P014
10
0
255
K/10
10
P014
Contact sensor: limit value temperature to activate fan
stages in cooling mode
18
0
255
°C
18
P015
Function of input AI1
0
0
19
-
0
P016
Function of input AI2
0
0
19
-
0
P017
Function of input AI3
0
0
9
-
0
P018
Temperature increase of cooling setpoint in Eco operation
30
0
255
K/10
30
P019
Temperature reduction of heating setpoint in Eco operation
30
0
255
K/10
30
P020
ADC limit coefficient
6
0
15
-
6
P021
ADC average coefficient
6
0
15
-
6
P022
Activation/deactivation of sun symbol in Comfort mode
0
0
1
-
0
P023
Difference for compensation when cooling
0
-99
127
K/10
0
P024
Coefficient for compensation when cooling
0
-20
20
1/10
0
P025
Difference for compensation when heating
0
-99
127
K/10
0
P026
Coefficient for compensation when heating
0
-20
20
1/10
0
P027
Fan setting: maximum run-time for manual fan mode
0
0
255
min.
0
P028
Rinsing function: fan stage during the rinsing function
2
1
5
-
2
P029
Activation of continuous fan mode
0
0
1
-
0
P030
Ventilation temperature activation
12
0
255
°C
12
P031
Ventilation interval
27
0
255
°C
27
P032
Rinsing function: maximum idle time of fan
15
0
255
min.
15
P033
Rinsing function: duration of the rinsing function
120
0
255
s
120
P034
Rinsing function: activation in operating modes
0
0
3
-
0
P035
Fan run-on time after an operating mode is switched to
stage 1
0
0
255
s
0
P036
Type of setpoint setting
0
0
1
-
0
P037
Display
1
0
7
-
1
Summary of Contents for Venkon XL
Page 2: ......