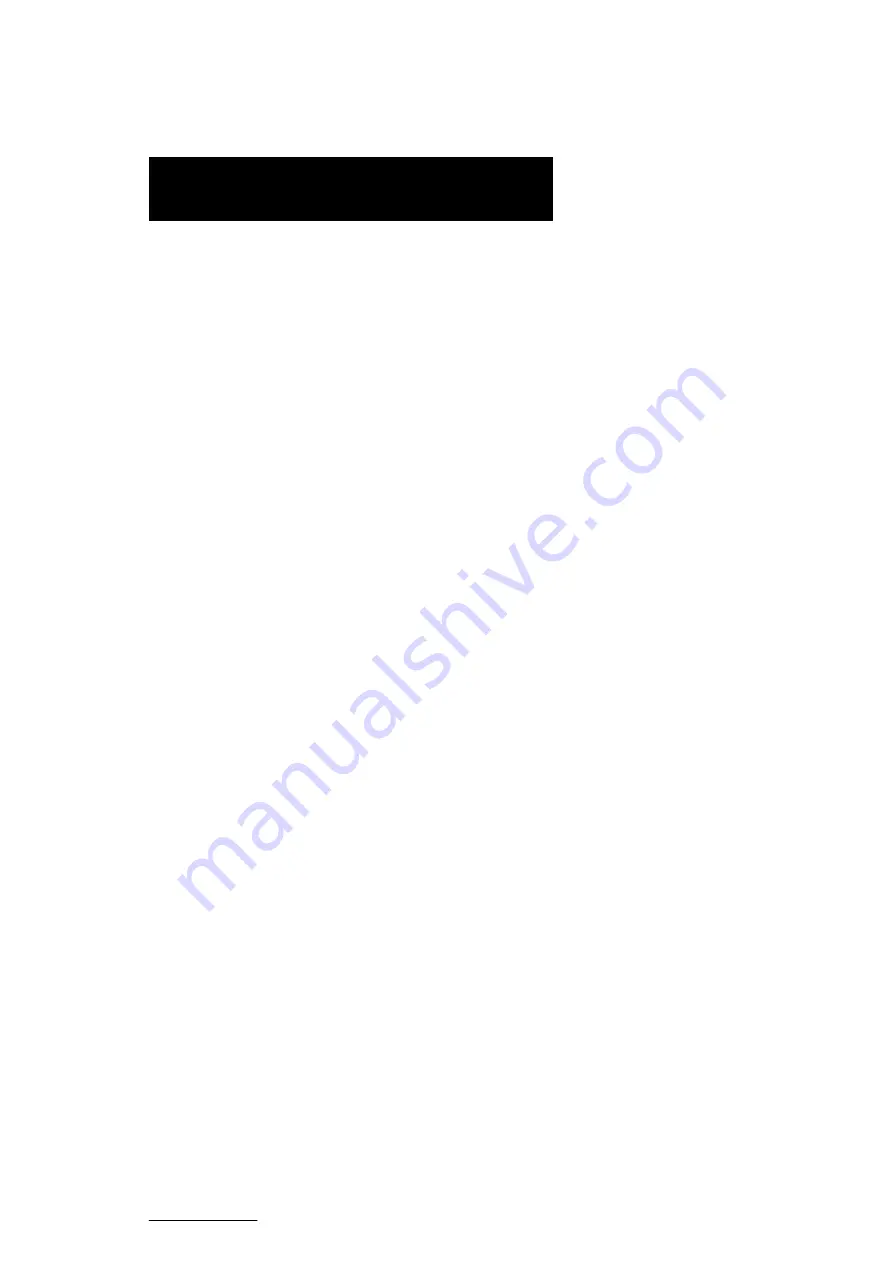
Operator Manual
Refrigerated Dryer
TG
No.: 901760 02 USE
Manufacturer:
KAESER KOMPRESSOREN SE
96410 Coburg • PO Box 2143 • GERMANY • Tel. +49-(0)9561-6400 • Fax +49-(0)9561-640130
www.kaeser.com
Summary of Contents for TG 450
Page 2: ...Original instructions KKW DTG 2 02 en Z1 SBA TROCKNER 20221118 115620...
Page 6: ...Contents iv Operator Manual Refrigerated Dryer TG No 901760 02 USE...
Page 8: ...List of Illustrations vi Operator Manual Refrigerated Dryer TG No 901760 02 USE...
Page 10: ...List of Tables viii Operator Manual Refrigerated Dryer TG No 901760 02 USE...