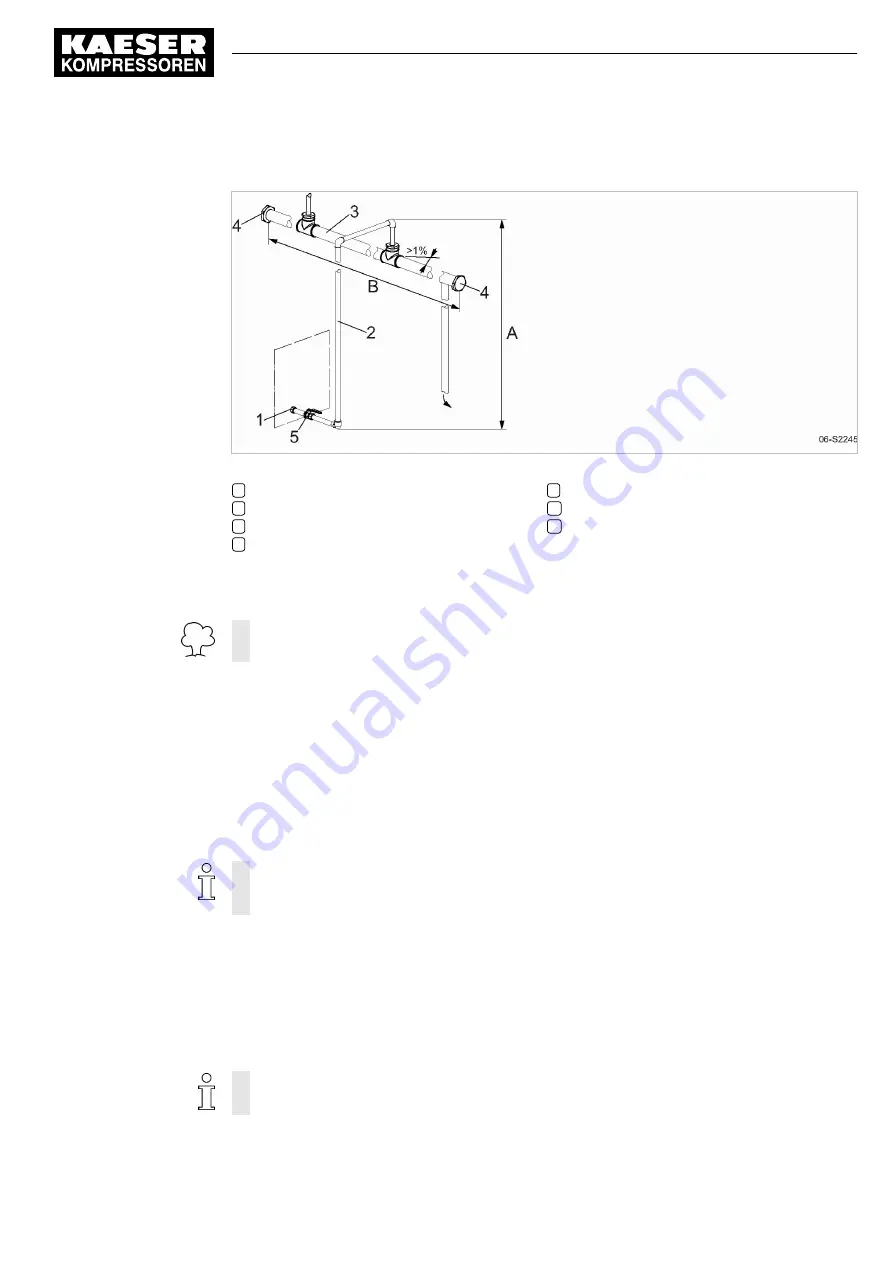
Connecting the condensate drain
Fig. 13 Connecting the condensate drain
1
Threaded connection
2
Condensate line
3
Condensate collecting line
4
Screw plug
5
Shut-off valve
A
Delivery head
B
Length of the condensate collecting line
Depending on the machine model, you may have several condensate drains.
➤ Directly connect every condensate drain to the condensate collecting line.
➤ Collect the condensate in a suitable container and dispose of in accordance with environ‐
mental regulations.
Further information The dimensional drawing in chapter 13.2 provides the size and position of the connection port.
6.5 Refrigerated dryer: Connecting the transformer according to the
power supply.
The refrigerated dryer transformer has tappings for various power supply voltages.
The pimary winding of the dryer transformer is not connected. The refrigerated dryer will not run
without connecting the control transformer according to the power supply.
Do only use terminal 0V–208V–230V–460V (primary winding of the transformer) for changing
the main voltage connection. Do not change the terminal 0V–230V. This terminal is readily
wired.
1. Check that the correct connections are made for the supply voltage provided for the machine.
2. If necessary, re-connect the transformer to match the power supply voltage.
Further information The electrical diagram in chapter 13.3 contains further details of the power supply connection.
6.6 Making the Power Supply Connection
The machine is not wired ready for operation!
This is a Tri-Voltage machine.
6
Installation
6.5
Refrigerated dryer: Connecting the transformer according to the power supply.
9_6917 34 USE
Operator Manual Screw Compressor
AIRTOWER 3C–7.5C Tri-Voltage
41