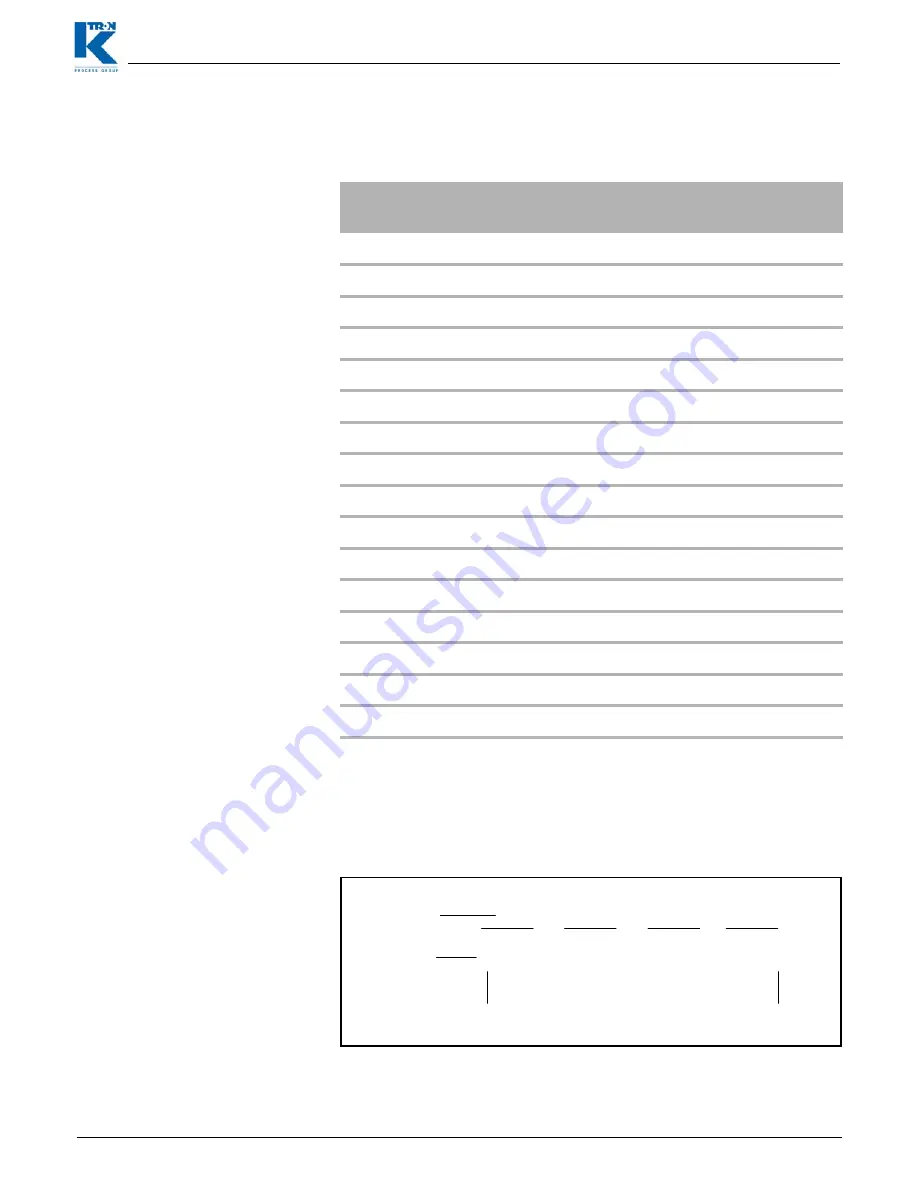
Docu-No.: 0590020601-EN Rev. 1.6.0
Page 99
Appendix 5
Status tables 5.4
5.4.5
SFT status table
This table shows the table of the possible Status displayed in the scale
menu at the variable SFT Status
Example:
0183= group mode, group leader, filter on, weight conversion
complete.
Fig. 5.10
SFT hex codes
Bit
Function
Hex
Code
0
1 = Group mode
0001
1
1 = Group leader
0002
2
Not used
0004
3
1 = Continuous mode
0008
4
1 = Error received
0010
5
1 = Baud Rate range error
0020
6
1 = Not used
0040
7
1 = Filter on
0080
8
1 = Weight conversion complete
0100
9
1 = EEPROM read or write error
0200
10
1 = K-FFP (Fast Frequency Processor) error
0400
11
1 = Ft - temperature frequency out of range
0800
12
1 = Fw - weight frequency out of range
1000
13
1 = Weight window range error
2000
14
1 = Temperature window range error
4000
15
1 = General alarm
8000
0000 0001 1000 0011
15
0
0 1 8 3
Hex
Bits