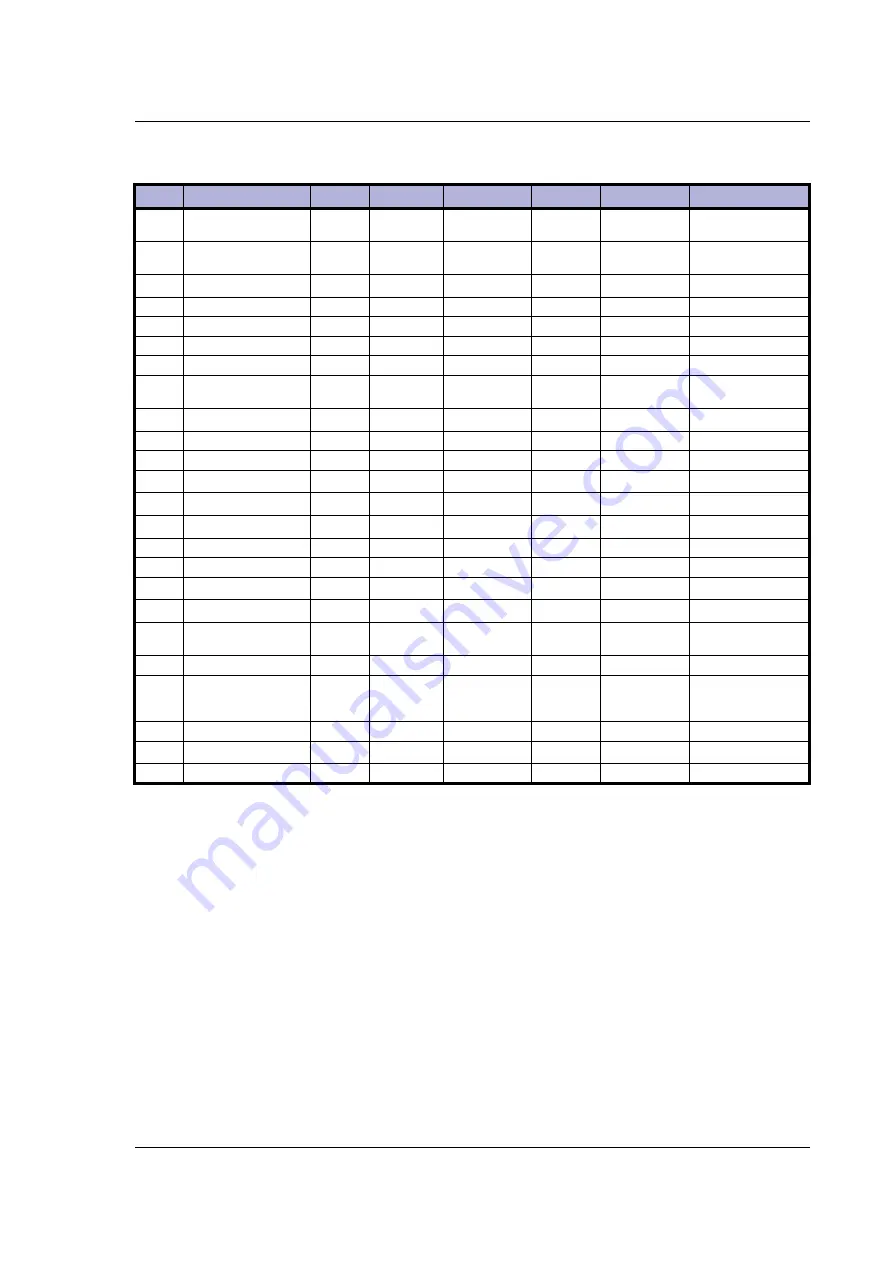
JVL Industri Elektronik A/S - User Manual - Integrated Stepper Motors MIS23x, 34x, 43x
117
8.2
MIS23x Registers
8.2.1
MIS23x and SMC75 Register Overview.
Reg
Name
Size
Access
Range
Default
Unit
MacTalk name
1
PROG_VERSION
16bit
R
-
*
Se detailed
description
“Status bar”
2
Mode_Reg
16bit
R/W
0,1,2,3,
13,14,15
0
-
Current Mode
3
P_SOLL
32bit
R/W
(-2
31
)-(2
31
-1)
0
steps
Position
5
V_SOLL
16bit
R/W
-1023-1023
250
RPM
Max velocity
6
A_SOLL
16bit
R/W
1-65535
131
9.54 RPM/s
Acceleration
7
RUN_CURRENT
16bit
0-511
511
5.87mA
Running Current
8
STANDBY_TIME
16bit
R/W
1-65535
500
ms
Standby Time
9
STANDBY_
CURRENT
16bit
R/W
0-511
128
5.87 mA
Standby Current
10
P_IST
32bit
R/W
(-2
31
)-(2
31
-1)
-
Steps
Actual Position
12
V_IST
16bit
R
0-1023
-
RPM
Actual Velocity
13
V_START
16bit
R/W
1-1023
100
RPM
Start Velocity
14
GEAR1
16bit
R/W
(-2
15
)-(2
15
-1)
1600
Steps
Output
15
GEAR2
16bit
R/W
(-2
15
)-(2
15
-1)
2000
Counts
Input
16
ENCODER_POS
32bit
R/W
(-2
31
)-(2
31
-1)
-
Steps
Encoder position
18
INPUTS
16bit
R
-
-
Special
Inputs
19
OUTPUTS
16bit
R/W
-
0
Special
Outputs
20
FLWERR
32bit
R
(-2
31
)-(2
31
-1)
-
Steps
Follow Error
22
FLWERRMAX
32bit
R/W
(-2
31
)-(2
31
-1)
0
Steps
Follow Error Max
24
COMMAND
16bit
R/W
0-127, 256,
257
0
-
N/A
25
STATUSBITS
16bit
R
-
-
Special
Run Status
26
TEMP
16bit
R
-2.27
uses
offset
Temperature
27
Reserved
-
-
-
-
-
28
MIN_P_IST
32bit
R/W
(-2
31
)-(2
31
-1)
0
Steps
Position Limit Min
Summary of Contents for MIS23 Series
Page 6: ...6 JVL Industri Elektronik A S User Manual Integrated Stepper Motors MIS23x 34x 43x ...
Page 29: ...JVL Industri Elektronik A S User Manual Integrated Stepper Motors MIS23x 34x 43x 27 ...
Page 56: ...54 JVL Industri Elektronik A S User Manual Integrated Stepper Motors MIS23x 34x 43x ...
Page 116: ...114 JVL Industri Elektronik A S User Manual Integrated Stepper Motors MIS23x 34x 43x ...
Page 188: ...186 JVL Industri Elektronik A S User Manual Integrated Stepper Motors MIS23x 34x 43x ...
Page 260: ...258 JVL Industri Elektronik A S User Manual Integrated Stepper Motors MIS23x 34x 43x ...
Page 335: ...JVL Industri Elektronik A S User Manual Integrated Stepper Motors MIS23x 34x 43x 333 ...
Page 341: ...JVL Industri Elektronik A S User Manual Integrated Stepper Motors MIS23x 34x 43x 339 ...