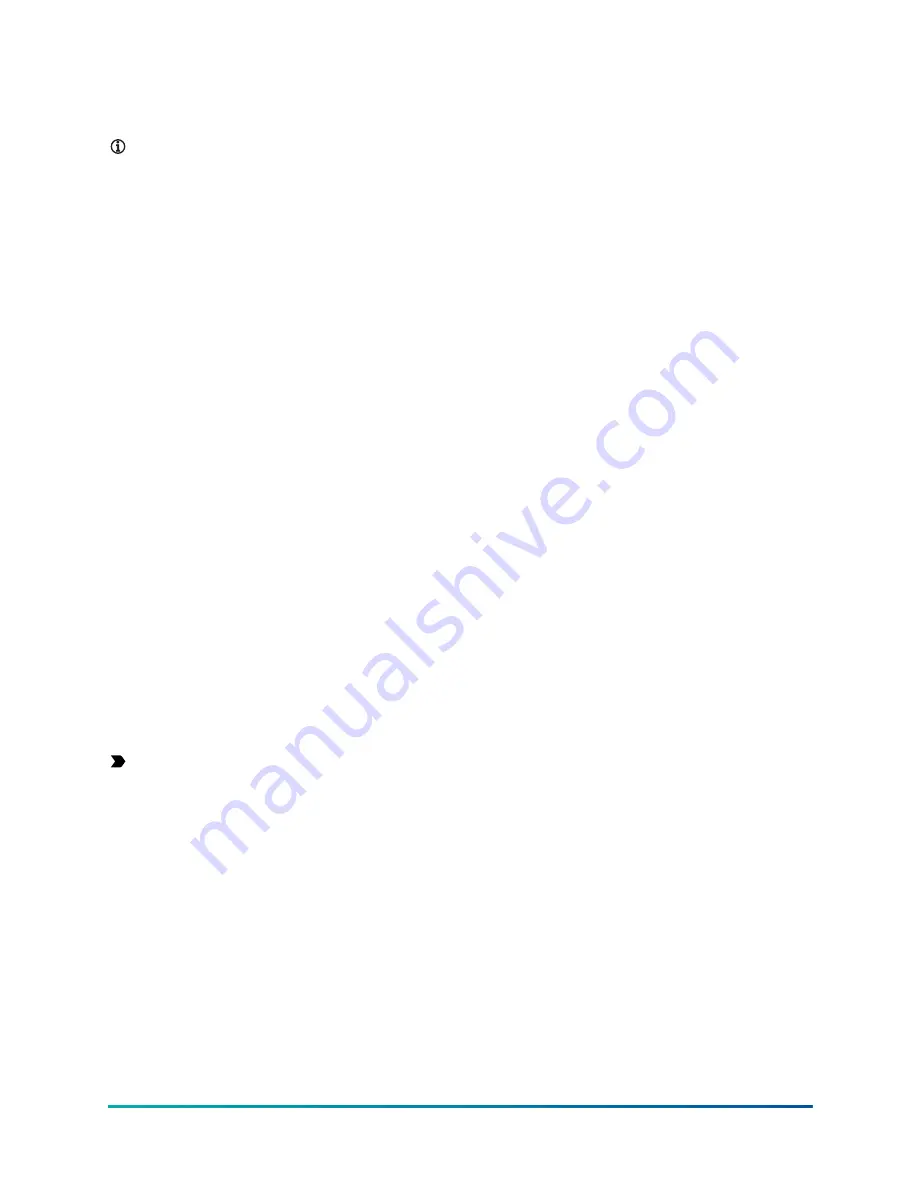
Cleaning Environment Guard Premium MCHX coils
About this task:
Note:
Environment Guard Premium coils are coated with black epoxy coating.
Environment Guard Premium microchannel coils must be cleaned following this procedure at least
once every quarter or every 3 months to ensure that the integrity of the coils and the warranty
of the coils are maintained. In environments where there are high levels of pollution or corrosive
elements, use a monthly cleaning procedure to remove debris, rinse with water, and dry, in
addition to the quarterly cleaning using approved cleaning solutions.
1. Use a vacuum cleaner with a soft brush attachment to remove surface debris such as dirt,
leaves, insects, or fibers. When brushing debris off the face of the coil, you can also use a
soft bristle brush. Do not use a wire brush. Do not scrape the coil with the vacuum nozzle, air
nozzle, or any other hard tool.
2. Rinse the coil with potable tap water. Use a gentle spray from a spray nozzle with a plastic
end. Do not contact the coil with the hose nozzle. Rinse the coil by running water through
every passage in the heat exchanger surface until it is clean.
3. Apply a coil cleaning solution approved by Johnson Controls. Details of solutions approved for
use are documented in product manuals.
4. To remove the cleaning solution, repeat the water rinse.
5. Apply a salt reducer solution approved by Johnson Controls. Details of solutions approved for
use are documented in product manuals.
6. To remove the salt reducer solution, repeat the water rinse. The final rinse must be thorough
to ensure that all cleaning solution and salt reducer solution is removed from the coils.
7. It is important to remove any excess water trapped in the coils immediately after the final
water rinse.
a.
To fully dry the coils, run the condenser fans on the chiller after the final water rinse.
b.
To remove any excess water, blow air through the coils with a hand-held blower or
vacuum.
Electrical controls
Perform annual checks to ensure that all electrical connections are tight and that connectors are
secure.
Important:
Do not change the factory settings of operation and safety controls. If the settings
are changed without Johnson Controls approval, the warranty will be jeopardized.
Unit heater operation verification
The YVAM chiller uses various heaters to protect all of the devices that are susceptible to low
ambient temperature limits. As part of the commissioning process of the chiller, it is important to
verify the operation of these heaters to ensure reliability of these various components. Verification
of heater operation must be logged using the current values for each heater in
Form 160.88-CL2
during chiller commissioning. Refer to
160.88-PW2
for power connection wires to be measured for
each device.
YVAM Control Center
140
Summary of Contents for YORK YVAM 0350
Page 2: ...2 YVAM Control Center...
Page 10: ...Figure 4 Variable speed drive nomenclature YVAM Control Center 10...
Page 15: ...Figure 8 System piping and instrumentation diagram P ID 15 YVAM Control Center...
Page 154: ...Figure 62 Sample printout status or history YVAM Control Center 154...
Page 155: ...Figure 63 Sample printout status or history continued 155 YVAM Control Center...
Page 156: ...Figure 64 Sample printout setpoints YVAM Control Center 156...
Page 157: ...Figure 65 Sample printout setpoints continued 157 YVAM Control Center...
Page 158: ...Figure 66 Sample printout schedule YVAM Control Center 158...
Page 159: ...Figure 67 Sample printout sales order 159 YVAM Control Center...
Page 160: ...Figure 68 Sample printout security log report YVAM Control Center 160...