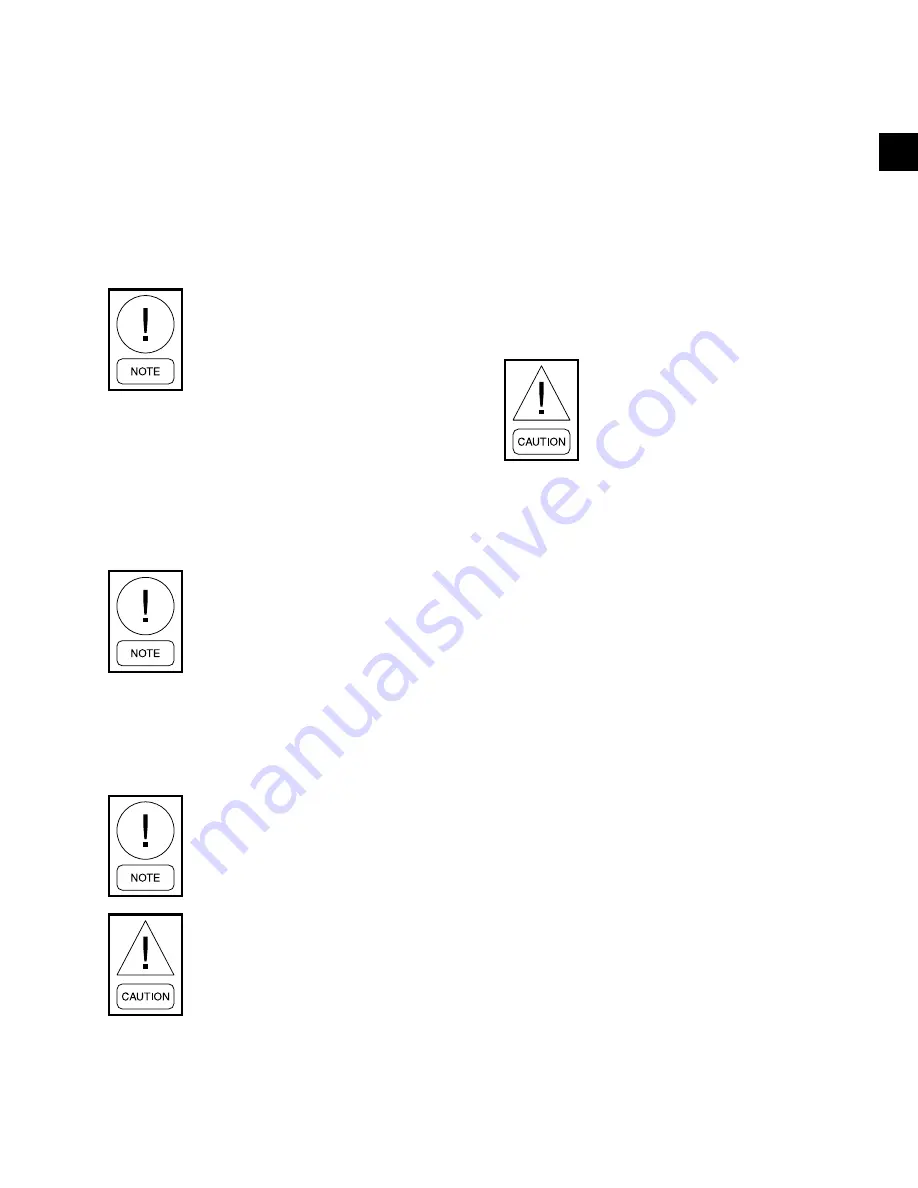
JOHNSON CONTROLS
23
SECTION 2 - INSTALLATION
FORM 160.69-N2
ISSUE DATE: 7/31/2015
2
CONTROL WIRING
On units shipped disassembled, after installation of the
control center, control wiring must be completed be-
tween unit components and control center, solid state
starter, or variable speed drive, when used, using wir-
ing harness furnished. Refer to Form 160.69-N3.
Field wiring connections for commonly encountered
control modifications (by others) if required, are shown
on Form 160.69-PW1.
No deviations in unit wiring from that
shown on drawings furnished shall be
made without prior approval of the John-
son Controls representative.
POWER WIRING
Oil Pump – 3 Phase Starter
Separate wiring or a fused disconnect switch should
be supplied by the installer and connected to the vari-
able speed oil pump panel. DO NOT make final power
connections to the chiller until approved by a Johnson
Controls representative.
Remote Electro-Mechanical starters for
the chiller must be furnished in accor-
dance with Johnson Controls Standard
(Product Drawing Form 160.69-PA1)
to provide the features necessary for
the starter to function properly with the
YORK control system.
Each chiller unit is furnished for a specific electrical
power supply as stamped on the Unit Data Plate, which
also details the motor connection diagrams.
To insure proper motor rotation the starter
power input and starter to motor connec-
tions must be check with a phase sequence
indicator in the presence of the Johnson
Controls representative.
DO NOT cut wires to final length or make
final connections to motor terminals or
starter power input terminals until ap-
proved by the Johnson Controls repre-
sentative.
YD Motors (Electro-Mechanical Starter)
shows the power wiring hook-
up for Motor Connections. (Refer to Wiring Labels in
Motor Terminal Box for hook-up to suit motor voltage
and amperage.) Motor leads are furnished with a crimp
type connection having a clearance hole for a 3/8" bolt,
motor terminal lugs are not furnished.
The YD Chiller has two motors which must be con-
nected to the proper starter. When viewed from the
chiller control panel, motor #1 is on the left and motor
#2 is on the right.
INSULATION
DO NOT field insulate until the unit has
been leak tested under the supervision of
a Johnson Controls representative.
Insulation of the type specified for the job, or mini-
mum thickness to prevent sweating of 30°F (-1°C)
surfaces should be furnished (by others) and applied
to the evaporator shell, end sheets, liquid feed line to
flow chamber, compressor suction connection, and
evaporator liquid heads and connections. The liquid
head flange insulation must be removable, to allow
head removal for the tube maintenance.
Units are furnished factory anti-sweat insulated on or-
der at additional cost. This includes all low tempera-
ture surfaces except the two (2) cooler liquid heads.