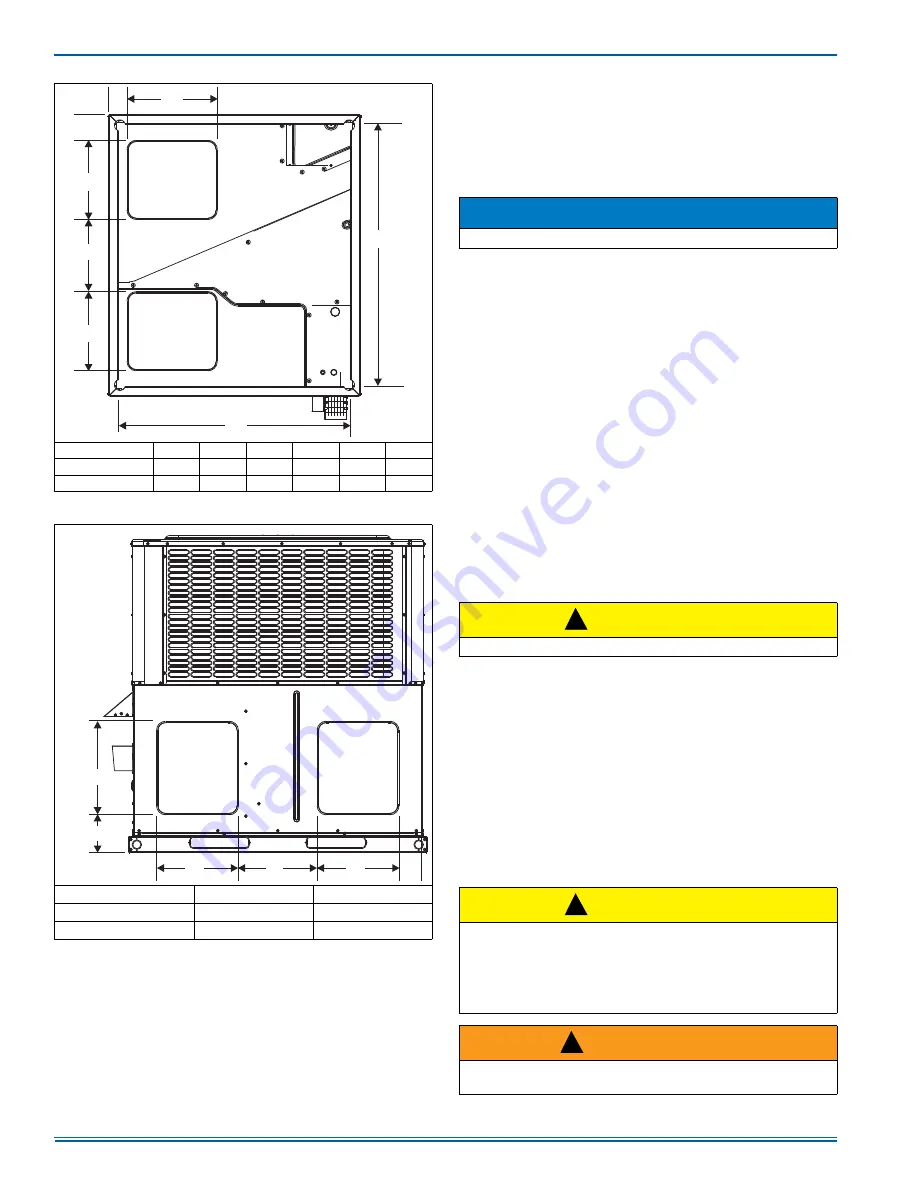
1183746-UIM-D-1015
6
Johnson Controls Unitary Products
DUCTWORK
These units are adaptable to downflow use as well as rear supply and
return air duct openings. To convert to downflow, use the following
steps:
1.
Remove the duct covers found in the bottom return and supply air
duct openings.
2.
Install the duct covers (removed in step one) to the rear supply and
return air duct openings.
3.
Seal duct covers with silicone caulk.
Duct work should be designed and sized according to the methods of
the Air Conditioning Contractors of America (ACCA), as set forth in their
Manual D.
A closed return duct system shall be used. This shall not preclude use
of economizers or ventilation air intake. Flexible joints are recom-
mended to be used in the supply and return duct work to minimize the
transmission of vibration and noise.
Refer to Figures 5 and 6 for information concerning rear and bottom
supply and return air duct openings.
FILTERS
Proper filter size is very important. Filter size, type and pressure drop
should always be considered during duct system design.
Single phase units are shipped without a filter or filter racks. It is the
responsibility of the installer to secure a filter in the return air ductwork
or install a Filter/Frame Kit.
A filter rack and high velocity filters are standard on three phase units.
Filters must always be used and must be kept clean. When filters
become dirt laden, insufficient air will be delivered by the blower,
decreasing your units efficiency and increasing operating costs and
wear-and-tear on the unit and controls.
Filters should be checked monthly; this is especially important since this
unit is used for both heating and cooling.
CONDENSATE DRAIN
A condensate trap must be installed in the condensate drain. The
plumbing must conform to local codes.
DO NOT use Teflon tape or Pipe thread compound.
SERVICE ACCESS
Access to all serviceable components is provided at the following loca-
tions:
• Coil guards
• Unit top panel
• Corner posts
• Blower access panel
• Control access panel
• Indoor coil access panel
• Compressor access panel
• Heat exchanger access panel
Refer to Figure 4 for location of these access locations and minimum
clearances in Table 4.
Refer to Figure 14 for the R-410A Quick Reference Guide.
Model
A
B
C
D
E
F
24, 30, 36, 42
10
21.5
5
4.5
47.5
32
48, 60
14
13.5
5
3.5
47.5
42
FIGURE 4:
Bottom Duct Dimensions (inches)
Model
A
B
24, 30, 36, 42
9.6
22
48, 60
13.6
14
FIGURE 5:
Rear Duct Dimensions (inches)
D
16
C
A
B
A
A0298-001
SUPPLY
AIR DUCT
RETURN
AIR DUCT
F
E
15.6
A
B
A
4.3
A0299-001
6
SUPPLY
AIR DUCT
RETURN
AIR DUCT
NOTICE
Be sure to note supply and return openings.
CAUTION
Hand tighten only.
CAUTION
This system uses R-410A Refrigerant which operates at higher pres-
sures than R-22. No other refrigerant may be used in this system.
Gage sets, hoses, refrigerant containers and recovery systems must
be designed to handle R-410A. If you are unsure, consult the equip-
ment manufacturer. Failure to use R-410A compatible servicing
equipment may result in property damage or injury.
WARNING
Wear safety glasses and gloves when handling refrigerants. Failure
to follow this warning can cause serious personal injury.
!
!
!