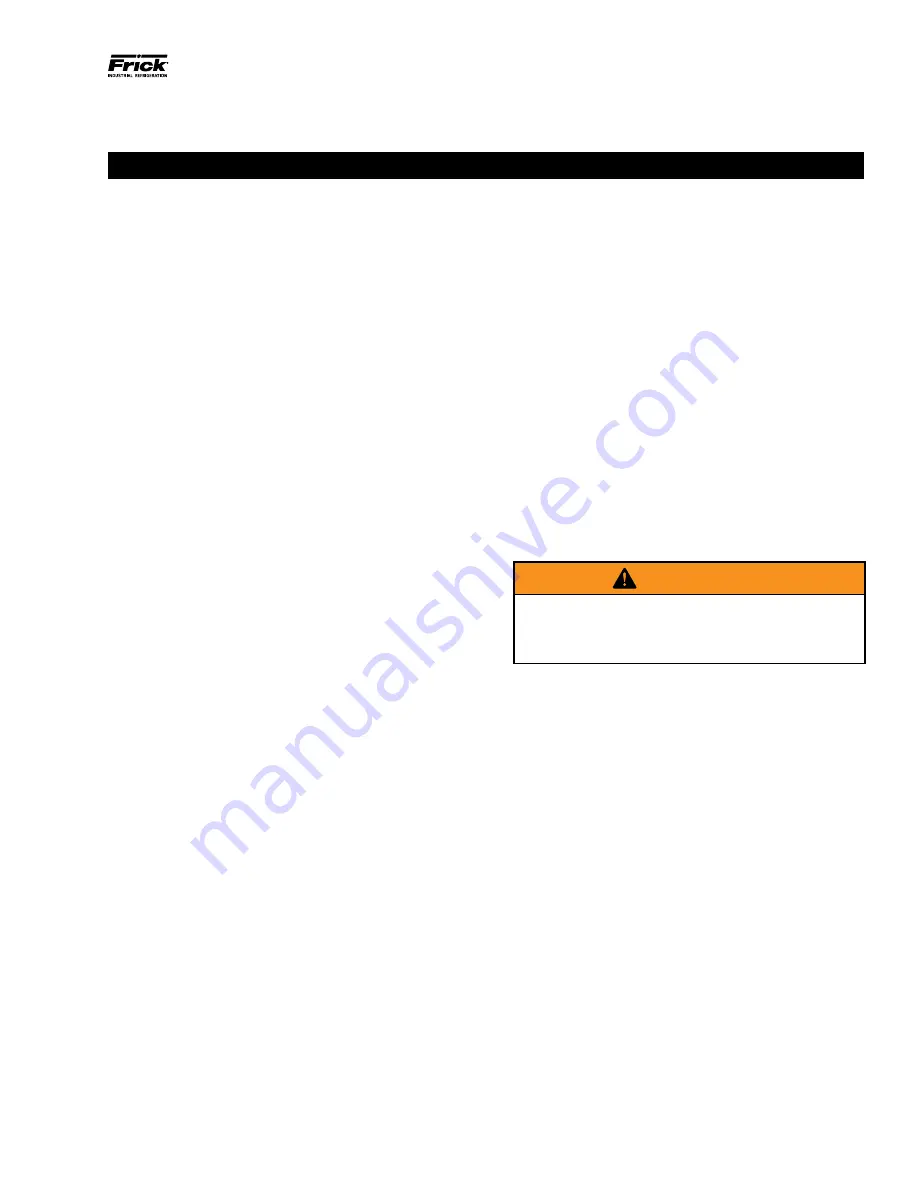
070.550-IOM (JUN 2016)
Page 3
NGC GAS ROTARY SCREW COMPRESSOR
INSTALLATION - OPERATION - MAINTENANCE
PREFACE
This manual has been prepared to acquaint the owner and
serviceman with the INSTALLATION, OPERATION, and
MAINTENANCE procedures as recommended by Johnson
Controls-Frick for NGC Rotary Screw Compressors.
It is most important that these compressors be properly
applied to an adequately controlled gas system. Your
authorized Johnson Controls-Frick representative should
be consulted for his expert guidance in this determination.
Proper performance and continued satisfaction with these
units is dependent upon:
CORRECT INSTALLATION
PROPER OPERATION
REGULAR, SYSTEMATIC MAINTENANCE
To ensure correct installation and application, the equipment
must be properly selected and connected to a properly
designed and installed system. The Engineering plans,
piping layouts, etc. must be detailed in accordance with the
best practices and local codes, such as those outlined in
ASHRAE literature.
COMPRESSOR BASICS
A screw compressor is a VAPOR PUMP. To be certain that it
is not being subjected to pumping liquid it is necessary
that:
1. Controls are carefully selected and in good operating
condition.
2. Piping is properly sized and traps, if necessary, are
correctly arranged.
3. Suction line has an accumulator or slugging protection.
4. Load surges are known and provisions are made for
control.
5. Operating cycles and stand-still periods are reasonable.
6. High side components are sized within system and
compressor design limits.
DESCRIPTION
NGC COMPRESSOR
The Johnson Controls - Frick NGC rotary screw compressor
utilizes mating asymmetrical profile helical rotors to provide
a continuous flow of vapor and is designed for both high-
pressure and low-pressure applications. The compressor
incorporates the following features:
1. High capacity roller bearings to carry radial loads at both
the inlet and outlet ends of the compressor.
2. Heavy duty, four-point contact ball or angular-contact
bearings are mounted at the discharge end of the
compressor to carry axial loads.
3. Balance pistons located in the inlet end of the compressor
reduce axial loads on the male axial bearings to increase
bearing life.
4. Moveable slide valve to provide fully modulating capacity
control from 100% to minimum capacity. See Table 1.
5.
VOLUMIZER® volume ratio control to allow infinitely
variable volume ratio from 2.2 to 5.0 for all NGC models
(except the NGC 300: 2.0 – 4.1 and the NGC 450: 2.4 – 4.5)
during compressor operation.
6. A hydraulic cylinder to operate the slide stop and slide
valve.
7. Housings designed for discharge pressures as noted in
Table 2, GENERAL SPECIFICATIONS.
8. All bearing and control oil vented to closed thread in the
compressor instead of suction pressure to avoid
performance penalties from superheating and displacing
suction gas.
9. Shaft seal housing is designed to maintain operating
pressure on seal well below discharge pressure for increased
seal life.
10. Oil injected into the rotors to maintain good volumetric
and adiabatic efficiency even at very high compression
ratios.
11. Shaft rotation clockwise facing compressor, suitable for
all types of drives.
SEE FOLLOWING WARNING.
WARNING
Compressor rotation is clockwise when facing the
compressor drive shaft. The compressor should never
be operated in reverse rotation, as bearing damage
will result.
12. Suction and discharge flanges are ANSI B16.1 Class 300
for all models except the NGC 300 which has ANSI B16.1
Class 150 flanges.
13. Integral suction strainers are provided for all models
except the NGC 400/450. The NGC 400/450 models must be
fitted with a suitable strainer, #60 mesh X .0065” diameter
stainless steel wire or better, to prevent damage to the
compressor from particles entering the suction area.
14. Integral gearbox available with 4 different gear ratios for
all models except the NGC 400/450 which have 6 ratios
available.
15. Integral internal driven seal-less oil pump.
COMPRESSOR LUBRICATION SYSTEM
The lubrication system on an NGC screw compressor unit
performs several functions:
1. Provides lubrication to bearings and seal.
2. Provides a cushion between the rotors to minimize noise
and vibrations.
3. Helps keep the compressor cool and prevents overheating.
4. Provides an oil supply to hydraulically actuate the slide
valve and slide stop.
5. Provides oil pressure to the balance piston to help increase
bearing life.
6. Provides an oil seal between the rotors to prevent rotor
contact or gas bypassing.
THE INFORMATION CONTAINED IN THIS DOCUMENT IS SUBJECT TO CHANGE
WITHOUT NOTICE
General Information