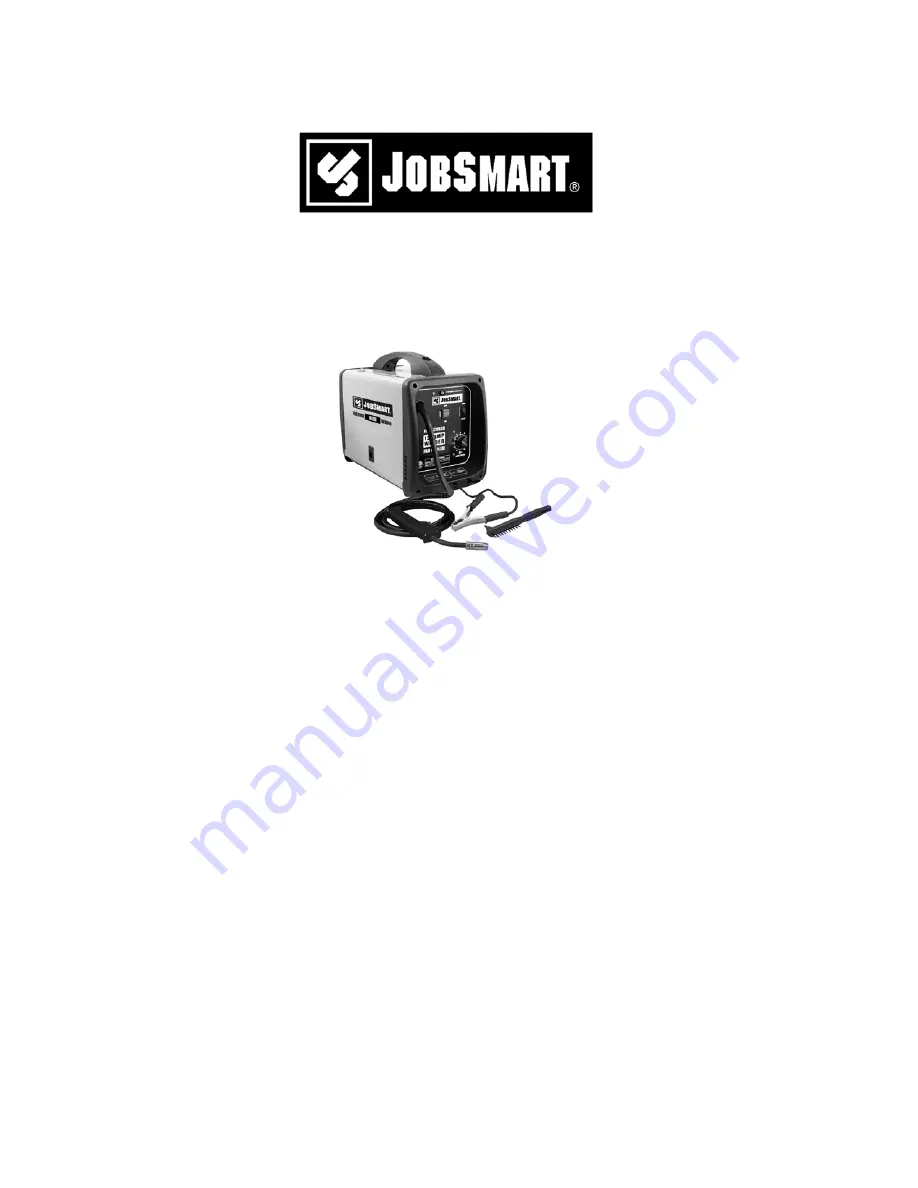
1128762
Flux-cored 125 Amp Welder
Assembly & Operating Instructions
READ ALL INSTRUCTIONS AND WARNINGS BEFORE USING THIS PRODUCT.
This manual provides important information on proper operation & maintenance. Every effort has been
made to ensure the accuracy of this manual. These instructions are not meant to cover every possible
condition and situation that may occur.
We reserve the right to change this product at any time
without prior notice.
IF THERE IS ANY QUESTION ABOUT A CONDITION BEING SAFE OR UNSAFE, DO
NOT OPERATE THIS PRODUCT!
HAVE QUESTIONS OR PROBLEMS? DO NOT RETURN THIS PRODUCT TO THE
RETAILER - CONTACT CUSTOMER SERVICE.
If you experience a problem or need parts for this product, call our customer support at
1-888-376-9601. A copy of the sales receipt is required.
FOR CONSUMER USE ONLY – NOT FOR PROFESSIONAL USE.
KEEP THIS MANUAL, SALES RECEIPT & APPLICABLE WARRANTY FOR FUTURE
REFERENCE.
Summary of Contents for 1128762
Page 23: ...23 Figure 21 Drive Assembly Figure 22 Torch Assembly...
Page 24: ...24 TABLE 5 TROUBLESHOOTING...
Page 25: ...25 MMIG125 WIRING DIAGRAM...
Page 27: ...27 1 888 376 9601...