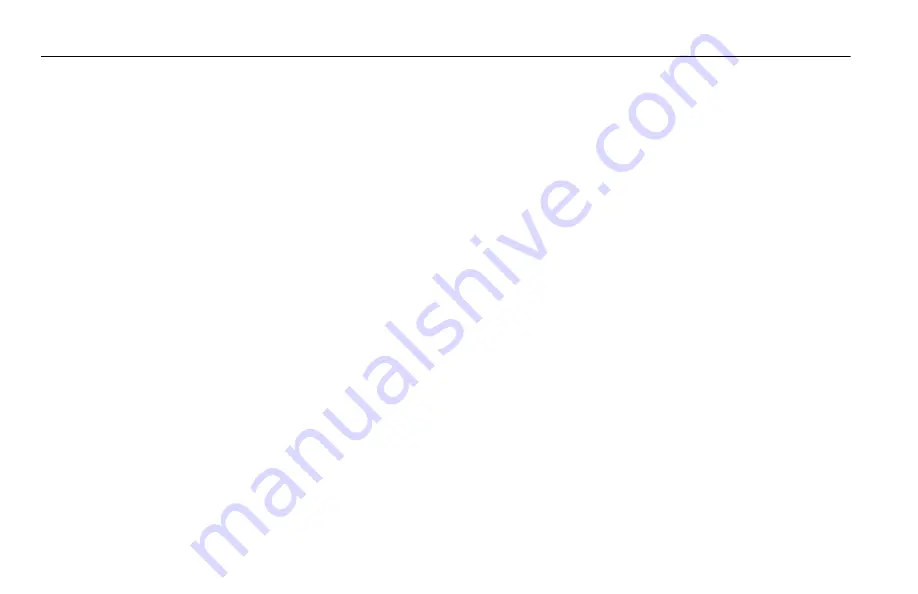
SECTION 1 - SAFETY PRECAUTIONS
1-2
– JLG Lift –
3121303
• An operator must not accept operating responsibilities
until adequate training has been given by competent and
authorized persons.
• Allow only those authorized and qualified personnel to
operate the machine who have demonstrated that they
understand the safe and proper operation and mainte-
nance of the unit.
• Read, understand, and obey all DANGERS, WARNINGS,
CAUTIONS, and operating instructions on the machine
and in this manual.
• Ensure that the machine is to be used in a manner which
is within the scope of its intended application as deter-
mined by JLG.
• All operating personnel must be familiar with the emer-
gency controls and emergency operation of the machine
as specified in this manual.
• Read, understand, and obey all applicable employer,
local, and governmental regulations as they pertain to
your utilization and application of the machine.
Workplace Inspection
• Precautions to avoid all hazards in the work area must be
taken by the user before operation of the machine.
• Do not operate or raise the platform from a position on
trucks, trailers, railway cars, floating vessels, scaffolds or
other equipment unless the application is approved in
writing by JLG.
• Before operation, check work area for overhead hazards
such as electric lines, bridge cranes, and other potential
overhead obstructions.
• Check floor surfaces for holes, bumps, drop-offs, obstruc-
tions, debris, concealed holes, and other potential haz-
ards.
• Check the work area for hazardous locations. Do not
operate the machine in hazardous environments unless
approved for that purpose by JLG.
• Ensure that the ground conditions are adequate to sup-
port the maximum tire load indicated on the tire load
decals located on the chassis adjacent to each wheel.
• Do not operate the machine when wind conditions exceed
12.5 m/s (28 mph).
• This machine can be operated in nominal ambient tem-
peratures of -15
o
C to 45
o
C (5
o
F to 113
o
F). Consult JLG to
optimize operation outside of this temperature range.
Summary of Contents for LIFTLUX 210-25
Page 2: ......
Page 22: ...SECTION 1 SAFETY PRECAUTIONS 1 12 JLG Lift 3121303 NOTES...
Page 32: ...SECTION 2 USER RESPONSIBILITIES MACHINE PREPARATION AND INSPECTION 2 10 JLG Lift 3121303 NOTES...
Page 82: ......
Page 83: ......