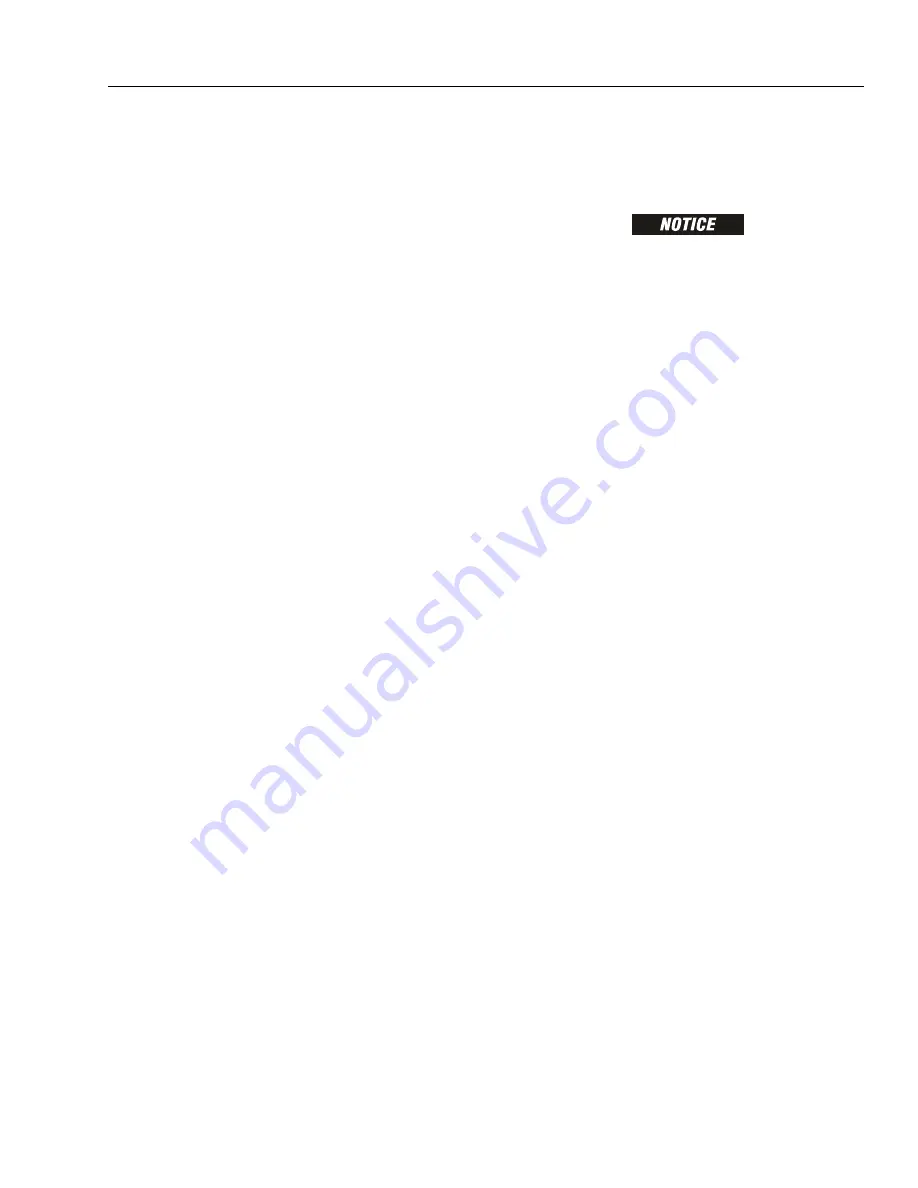
SECTION 5 - BASIC HYDRAULIC INFOR
M
ATION AND SCHE
M
ATICS
3121160
5-3
5.2
VALVES - THEORY OF OPERATION
Solenoid Control Valve - Rexroth
Control valves used are four-way three-position solenoid
valves of the sliding spool design. When a circuit is activated
and the control valve solenoid energizes, the spool is shifted
and the corresponding work port opens to permit oil flow to
the component in the selected circuit with the opposite work
port opening to reservoir. Once the circuit is deactivated (con-
trol returned to neutral) the valve spool returns to neutral
(center) and oil flow is then directed through the valve body
and returns to reservoir. A typical control valve consist of the
valve body, sliding spool, and two solenoid assemblies. The
spool is machine fitted in the bore of the valve body. Lands on
the spool divide the bore into various chambers, which when
the spool is shifted, align with corresponding ports in the
valve body open to common flow. At the same time other
ports would be blocked to flow. The spool is spring loaded to
center position, therefore when the control is released, the
spool automatically returns to neutral, prohibiting any flow
through the circuit.
Relief Valves
Relief valves are installed at various points within the hydraulic
system to protect associated systems and components against
excessive pressure. Excessive pressure can be developed when
a cylinder reaches its limit of travel and the flow of pressurized
fluid continues from the system control. The relief valve pro-
vides an alternate path for the continuing flow from the pump,
thus preventing rupture of the cylinder, hydraulic line or fit-
ting. Complete failure of the system pump is also avoided by
relieving circuit pressure. The relief valve is installed in the cir-
cuit between the pump outlet (pressure line) and the cylinder
of the circuit, generally as an integral part of the system valve
bank. Relief pressures are set slightly higher than the load
requirement, with the valve diverting excess pump delivery
back to the reservoir when operating pressure of the compo-
nent is reached.
5.3
HOLDING VALVE CHECKS
1.
Start the machine and warm the hydraulic system to
operating temperature.
PERFORM ALL HOLDING VALVE CHECKS FROM THE GROUND CONTROL STA-
TION WITH AN EMPTY PLATFORM.
2.
Check the Upright level cylinder rod side holding valve
as follows:
a.
Fully retract and fully lower the main boom and
tower boom assemblies.
b.
Power the main boom lift down function into the
turntable boom rest by holding the function switch
down between 10 and 20 seconds.
c.
Verify the upright remains perpendicular to the
turntable and that the Upright Monitoring System
alarms have not been activated.
3.
Check the Upright level cylinder barrel side holding
valve function as follows:
a.
Fully retract and fully lower the main boom and
tower boom assemblies. Raise the tower boom
between 2 ft. and 5 ft. (0.6 m and 1.5 m).
b.
Pull and hold the re-leveling knob between 20 and
30 seconds.
c.
Verify the upright remains perpendicular to the
turntable and that the Upright Monitoring System
alarms have not been activated.
4.
Check the Tower lift cylinder barrel side holding valve
function as follows:
a.
Fully raise and fully retract the tower boom. Fully
raise and fully extend the main boom.
b.
Using auxiliary power, fully lower the tower boom.
c.
Verify the upright remains perpendicular to the
turntable and that the Upright Monitoring System
alarms have not been activated.
Summary of Contents for 740AJ
Page 2: ......
Page 55: ...SECTION 3 CHASSIS TURNTABLE 3121160 3 3 This page left blank intentionally...
Page 116: ...SECTION 3 CHASSIS TURNTABLE 3 64 3121160 Figure 3 44 Swing Hub Prior to SN 0300074383...
Page 203: ...SECTION 3 CHASSIS TURNTABLE 3121160 3 151 Figure 3 77 EFI Component Location...
Page 206: ...SECTION 3 CHASSIS TURNTABLE 3 154 3121160 Figure 3 78 ECM EPM Identification ECM EPM...
Page 224: ...SECTION 3 CHASSIS TURNTABLE 3 172 3121160 Figure 3 83 Deutz EMR 2 Troubleshooting Flow Chart...
Page 228: ...SECTION 3 CHASSIS TURNTABLE 3 176 3121160 Figure 3 87 EMR 2 Engine Plug Pin Identification...
Page 229: ...SECTION 3 CHASSIS TURNTABLE 3121160 3 177 Figure 3 88 EMR 2 Vehicle Plug Pin Identification...
Page 230: ...SECTION 3 CHASSIS TURNTABLE 3 178 3121160 Figure 3 89 EMR2 Fault Codes Sheet 1 of 5...
Page 231: ...SECTION 3 CHASSIS TURNTABLE 3121160 3 179 Figure 3 90 EMR2 Fault Codes Sheet 2 of 5...
Page 232: ...SECTION 3 CHASSIS TURNTABLE 3 180 3121160 Figure 3 91 EMR2 Fault Codes Sheet 3 of 5...
Page 233: ...SECTION 3 CHASSIS TURNTABLE 3121160 3 181 Figure 3 92 EMR2 Fault Codes Sheet 4 of 5...
Page 234: ...SECTION 3 CHASSIS TURNTABLE 3 182 3121160 Figure 3 93 EMR2 Fault Codes Sheet 5 of 5...
Page 303: ...SECTION 4 BOOM PLATFORM 3121160 4 31 Figure 4 20 Rotator Assembly HELAC...
Page 460: ...SECTION 5 BASIC HYDRAULIC INFORMATION AND SCHEMATICS 5 116 3121160 NOTES...
Page 467: ...SECTION 6 JLG CONTROL SYSTEM 3121160 6 7 Figure 6 2 ADE Block Diagram...
Page 534: ...SECTION 6 JLG CONTROL SYSTEM 6 74 3121160 NOTES...
Page 580: ...SECTION 7 BASIC ELECTRICAL INFORMATION SCHEMATICS 7 46 3121160 NOTES...
Page 581: ......