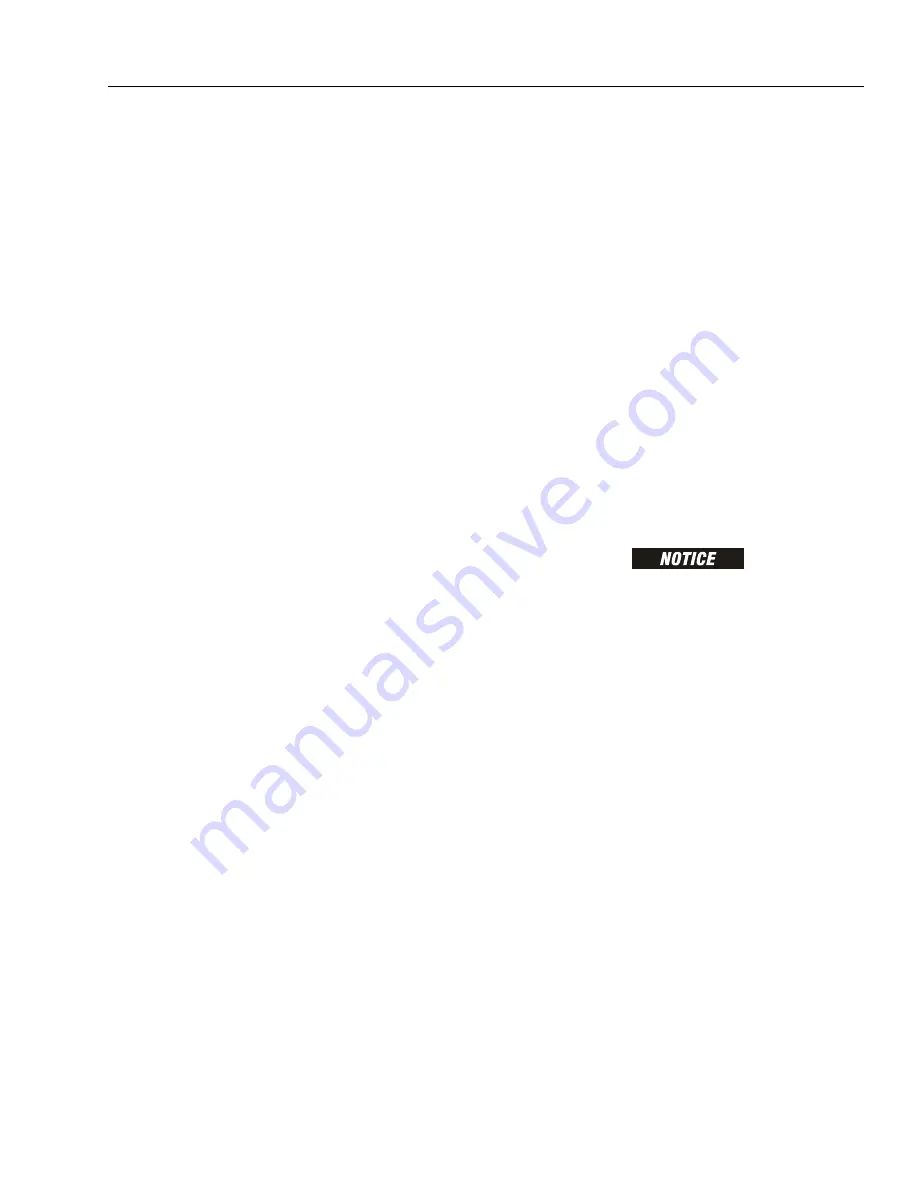
SECTION 4 - BOOM & PLATFORM
3121160
– JLG Lift –
4-13
7.
Using all applicable safety precautions, carefully lift
boom assembly clear of upright and lower to ground
or suitably supported work surface.
Disassembly
1.
Remove hardware securing telescope cylinder to aft
end of the base boom section.
2.
Remove hardware which secures the wear pads to
the base boom section; remove the wear pads from
the top, sides and bottom of the base boom section.
3.
Using overhead crane or suitable lifting device,
remove fly boom assembly from base section.
4.
Remove hardware from the telescope cylinder pin.
Using a suitable brass drift and hammer remove the
cylinder pin from fly boom section.
5.
Pull the telescope cylinder partially from aft end of
the fly boom section; secure the cylinder with a suit-
able sling and lifting device at approximately the
center of gravity.
6.
Carefully remove the telescope cylinder and place
telescope cylinder on a suitable trestle.
NOTE:
The Main Boom Telescope Cylinder can be removed
without the main boom disassembly by disconnect-
ing hydraulic lines, top attaching pin of main lift cylin-
der and telescope cylinders as directed above, and
pulling out the telescope cylinder from the rear, thru
the access plate opening of the upright.
7.
Remove hardware which secures the wear pads to
the aft end of fly boom section; remove the wear
pads from the top, sides and bottom of the fly boom
section.
Inspection
NOTE:
When inspecting pins and bearings Refer to Section
2, Pins and Composite Bearing Repair Guidelines.
1.
Inspect main boom pivot pin for wear, scoring, taper-
ing and ovality, or other damage. Replace pins as
necessary.
2.
Inspect telescope cylinder attach point for scoring,
tapering and ovality. Replace pins as necessary.
3.
Inspect upper lift cylinder attach pin for wear, scor-
ing, tapering and ovality, or other damage. Ensure
pin surfaces are protected prior to installation.
Replace pins as necessary.
4.
Inspect inner diameter of boom pivot bearing for
scoring, distortion, wear, or other damage. Replace
bearing as necessary. (See Section 5, Cylinder
Repair for bearing replacement).
5.
Inspect all wear pads for excessive wear, or other
damage. Replace pads when worn as specified in
Figure 4-12., Location And Thickness Of Wear Pads.
6.
Inspect all threaded components for damage such
as stretching, thread deformation, or twisting.
Replace as necessary.
7.
Inspect structural units of boom assembly for bend-
ing, cracking, separation of welds, or other damage.
Replace boom sections as necessary.
Assembly
NOTE:
When installing fly section wear pads, install same
number and thickness of shims as were removed
during disassembly.
1.
Measure inside dimensions of the base section to
determine the number of shims required for proper
fit.
2.
Install side, top and bottom wear pads to the aft end
of fly section; shim evenly to the measurements of
the inside of base boom section.
WHEN ASSEMBLING BOOM SECTIONS, ENSURE THAT THE BOOM
SLIDING TRAJECTORIES HAVE BEEN CLEARED OF CHAINS,
TOOLS, AND OTHER OBSTRUCTIONS.
3.
Secure the sling and lifting device at the telescope
cylinder’s approximate center of gravity, and lift the
cylinder to the aft end of the fly boom section.
4.
Slide telescope cylinder into the aft end of fly boom
section. Align attachment holes in fly boom section
with hole in rod end of telescope cylinder.
5.
Install telescope cylinder pin and secure with mount-
ing hardware.
6.
Secure the sling and lifting device at the fly boom
assembly approximate center of gravity.
7.
Slide fly boom assembly into the base boom sec-
tion. Shim boom, if necessary, for a total of 1/32 inch
(0.8 mm) clearance.
8.
Install wear pads into the forward position of the
base boom section. Shim boom, if necessary, for a
total of 1/32 inch (0.8 mm) clearance.
9.
Align the cylinder with the slots at aft end of base
boom section, then secure cylinder with mounting
hardware.
Summary of Contents for 740A
Page 1: ...Service and Maintenance Manual Models 740A 740AJ P N 3121160 January 8 2013 ...
Page 2: ......
Page 52: ...SECTION 2 GENERAL 2 12 JLG Lift 3121160 NOTES ...
Page 109: ...SECTION 3 CHASSIS TURNTABLE 3121160 JLG Lift 3 57 Figure 3 39 Swing Hub ...
Page 135: ...SECTION 3 CHASSIS TURNTABLE 3121160 JLG Lift 3 83 Figure 3 48 Rotary Coupling Port Location ...
Page 153: ...SECTION 3 CHASSIS TURNTABLE 3121160 JLG Lift 3 101 Figure 3 54 EFI Component Location ...
Page 156: ...SECTION 3 CHASSIS TURNTABLE 3 104 JLG Lift 3121160 Figure 3 55 ECM EPM Identification ECM EPM ...
Page 173: ...SECTION 3 CHASSIS TURNTABLE 3121160 JLG Lift 3 121 Figure 3 65 EMR2 Fault Codes Sheet 1 of 5 ...
Page 174: ...SECTION 3 CHASSIS TURNTABLE 3 122 JLG Lift 3121160 Figure 3 66 EMR2 Fault Codes Sheet 2 of 5 ...
Page 175: ...SECTION 3 CHASSIS TURNTABLE 3121160 JLG Lift 3 123 Figure 3 67 EMR2 Fault Codes Sheet 3 of 5 ...
Page 176: ...SECTION 3 CHASSIS TURNTABLE 3 124 JLG Lift 3121160 Figure 3 68 EMR2 Fault Codes Sheet 4 of 5 ...
Page 177: ...SECTION 3 CHASSIS TURNTABLE 3121160 JLG Lift 3 125 Figure 3 69 EMR2 Fault Codes Sheet 5 of 5 ...
Page 244: ...SECTION 4 BOOM PLATFORM 4 28 JLG Lift 3121160 Figure 4 14 Rotator Assembly HELAC ...
Page 286: ...SECTION 4 BOOM PLATFORM 4 70 JLG Lift 3121160 NOTES ...
Page 307: ...SECTION 5 HYDRAULICS 3121160 JLG Lift 5 21 Figure 5 17 Variable Displacement Pump Rexroth ...
Page 316: ...SECTION 5 HYDRAULICS 5 30 JLG Lift 3121160 NOTES ...
Page 319: ...SECTION 6 JLG CONTROL SYSTEM 3121160 JLG Lift 6 3 Figure 6 2 ADE Block Diagram ...
Page 328: ...SECTION 6 JLG CONTROL SYSTEM 6 12 JLG Lift 3121160 Figure 6 11 Control Module Location ...
Page 374: ...SECTION 6 JLG CONTROL SYSTEM 6 58 JLG Lift 3121160 NOTES ...
Page 406: ...SECTION 7 BASIC ELECTRICAL INFORMATION SCHEMATICS 7 32 JLG Lift 3121160 NOTES ...
Page 407: ......