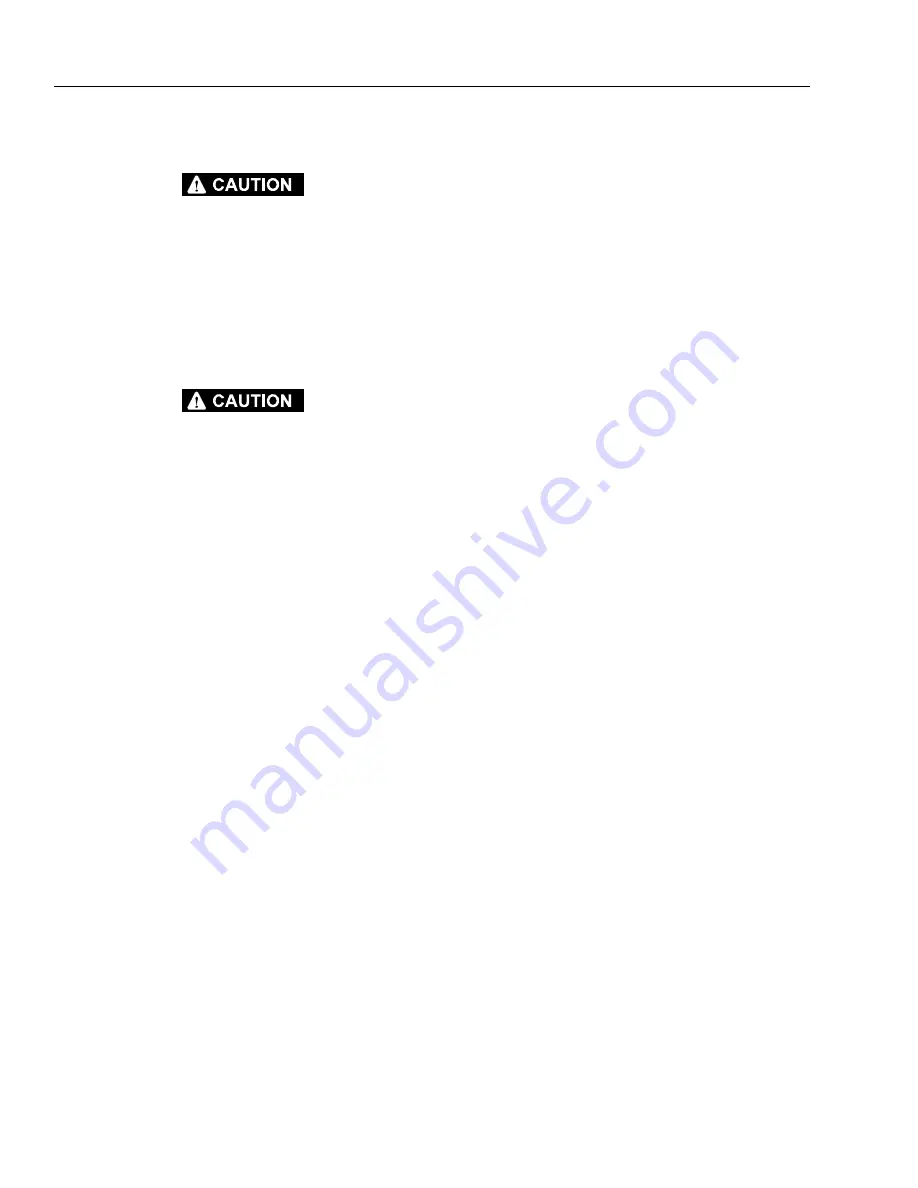
SECTION 3 - CHASSIS & TURNTABLE
3-90
– JLG Lift –
3121160
3.23 DUAL FUEL SYSTEM
IT IS POSSIBLE TO SWITCH FROM ONE FUEL SOURCE TO THE
OTHER WITHOUT ALLOWING THE ENGINE TO STOP. EXTREME
CARE MUST BE TAKEN AND THE FOLLOWING INSTRUCTIONS
MUST BE FOLLOWED.
Changing from Gasoline to LP Gas
1.
Start the engine from the ground control station.
2.
Open the hand valve on the LP gas supply tank by
turning counterclockwise.
BE SURE ALL GASOLINE IS EXHAUSTED BEFORE SWITCHING TO
LP GAS.
3.
While the engine is operating, place the two position
LPG/Gasoline switch at the platform control station
to the LP position. Allow the engine to operate with-
out load until the engine regains smoothness.
Changing from LP Gas to Gasoline
1.
With engine operating on LP under a no load condi-
tion, throw the LPG/Gasoline switch at the platform
control station to the “Gasoline” position. Allow the
engine to operate with no load until the engine
regains smoothness
2.
Close the hand valve on the LP gas supply tank by
turning clockwise.
3.24 EFI ENGINE
Performing Diagnostics
1.
Verify the complaint and determine if it is a deviation
from normal operation.
2.
Once the complaint has been verified, preliminary
checks can be done. Conduct a thorough visual
inspection, be alert for unusual sounds or odors,
and gather diagnostic trouble code information.
3.
Perform a system check that will verify the proper
operation of the system in question and check for
recent information updates.
4.
If a diagnostic trouble code (DTC) is stored, contact
a JLG distributor to make an effective repair.
5.
If no DTC is stored, select the symptom from the
symptom tables and follow the diagnostic path or
suggestions to complete the repair.
6.
After the repair has been made and validated for
proper operation, the old part should be momen-
tarily re-installed to verify that it was indeed the
source of the problem.
If no matching symptom is available, analyze the com-
plaint and develop a plan for diagnostics utilizing the wir-
ing diagrams, technical assistance, and repair history.
Intermittent conditions may be resolved by using a check
sheet to pinpoint the circuit or electrical system compo-
nent. Some diagnostic charts contain Diagnostic Aids
which give additional information about a system. Be sure
to use all of the information that is available to you.
VISUAL/PHYSICAL ENGINE INSPECTION
CHECK
Perform a careful visual and physical engine inspection
before performing any diagnostic procedure. Perform all
necessary repairs before proceeding with additional diag-
nosis, this can often lead to repairing a problem without
performing unnecessary steps. Use the following guide-
lines when performing a visual/physical inspection check:
• Inspect engine for modifications or aftermarket equip-
ment that can contribute to the symptom; verify that all
electrical and mechanical loads or accessory equip-
ment is "OFF" or disconnected before performing diag-
nosis.
• Inspect engine fluids for correct levels and evidence of
leaks.
• Inspect vacuum hoses for damage, leaks, cracks,
kinks and improper routing, inspect intake manifold
sealing surface for a possible vacuum leak.
• Inspect PCV valve for proper installation and operation.
• Inspect all wires and harnesses for proper connections
and routing; bent or broken connector pins; burned,
chafed, or pinched wires; and corrosion. Verify that
harness grounds are clean and tight.
• Inspect engine control module (ECM), sensors, and
actuators for physical damage.
• Inspect ECM grounds for cleanliness, tightness, and
proper location.
• Inspect fuel system for adequate fuel level, and fuel
quality (concerns such as proper octane, contamina-
tion, winter/summer blend).
• Inspect intake air system and air filter for restrictions.
• Inspect battery condition and starter current draw.
If no evidence of a problem is found after visual/physical
engine check has been performed, proceed to MIL DTC
retrieval procedure.
Summary of Contents for 740A
Page 1: ...Service and Maintenance Manual Models 740A 740AJ P N 3121160 January 8 2013 ...
Page 2: ......
Page 52: ...SECTION 2 GENERAL 2 12 JLG Lift 3121160 NOTES ...
Page 109: ...SECTION 3 CHASSIS TURNTABLE 3121160 JLG Lift 3 57 Figure 3 39 Swing Hub ...
Page 135: ...SECTION 3 CHASSIS TURNTABLE 3121160 JLG Lift 3 83 Figure 3 48 Rotary Coupling Port Location ...
Page 153: ...SECTION 3 CHASSIS TURNTABLE 3121160 JLG Lift 3 101 Figure 3 54 EFI Component Location ...
Page 156: ...SECTION 3 CHASSIS TURNTABLE 3 104 JLG Lift 3121160 Figure 3 55 ECM EPM Identification ECM EPM ...
Page 173: ...SECTION 3 CHASSIS TURNTABLE 3121160 JLG Lift 3 121 Figure 3 65 EMR2 Fault Codes Sheet 1 of 5 ...
Page 174: ...SECTION 3 CHASSIS TURNTABLE 3 122 JLG Lift 3121160 Figure 3 66 EMR2 Fault Codes Sheet 2 of 5 ...
Page 175: ...SECTION 3 CHASSIS TURNTABLE 3121160 JLG Lift 3 123 Figure 3 67 EMR2 Fault Codes Sheet 3 of 5 ...
Page 176: ...SECTION 3 CHASSIS TURNTABLE 3 124 JLG Lift 3121160 Figure 3 68 EMR2 Fault Codes Sheet 4 of 5 ...
Page 177: ...SECTION 3 CHASSIS TURNTABLE 3121160 JLG Lift 3 125 Figure 3 69 EMR2 Fault Codes Sheet 5 of 5 ...
Page 244: ...SECTION 4 BOOM PLATFORM 4 28 JLG Lift 3121160 Figure 4 14 Rotator Assembly HELAC ...
Page 286: ...SECTION 4 BOOM PLATFORM 4 70 JLG Lift 3121160 NOTES ...
Page 307: ...SECTION 5 HYDRAULICS 3121160 JLG Lift 5 21 Figure 5 17 Variable Displacement Pump Rexroth ...
Page 316: ...SECTION 5 HYDRAULICS 5 30 JLG Lift 3121160 NOTES ...
Page 319: ...SECTION 6 JLG CONTROL SYSTEM 3121160 JLG Lift 6 3 Figure 6 2 ADE Block Diagram ...
Page 328: ...SECTION 6 JLG CONTROL SYSTEM 6 12 JLG Lift 3121160 Figure 6 11 Control Module Location ...
Page 374: ...SECTION 6 JLG CONTROL SYSTEM 6 58 JLG Lift 3121160 NOTES ...
Page 406: ...SECTION 7 BASIC ELECTRICAL INFORMATION SCHEMATICS 7 32 JLG Lift 3121160 NOTES ...
Page 407: ......