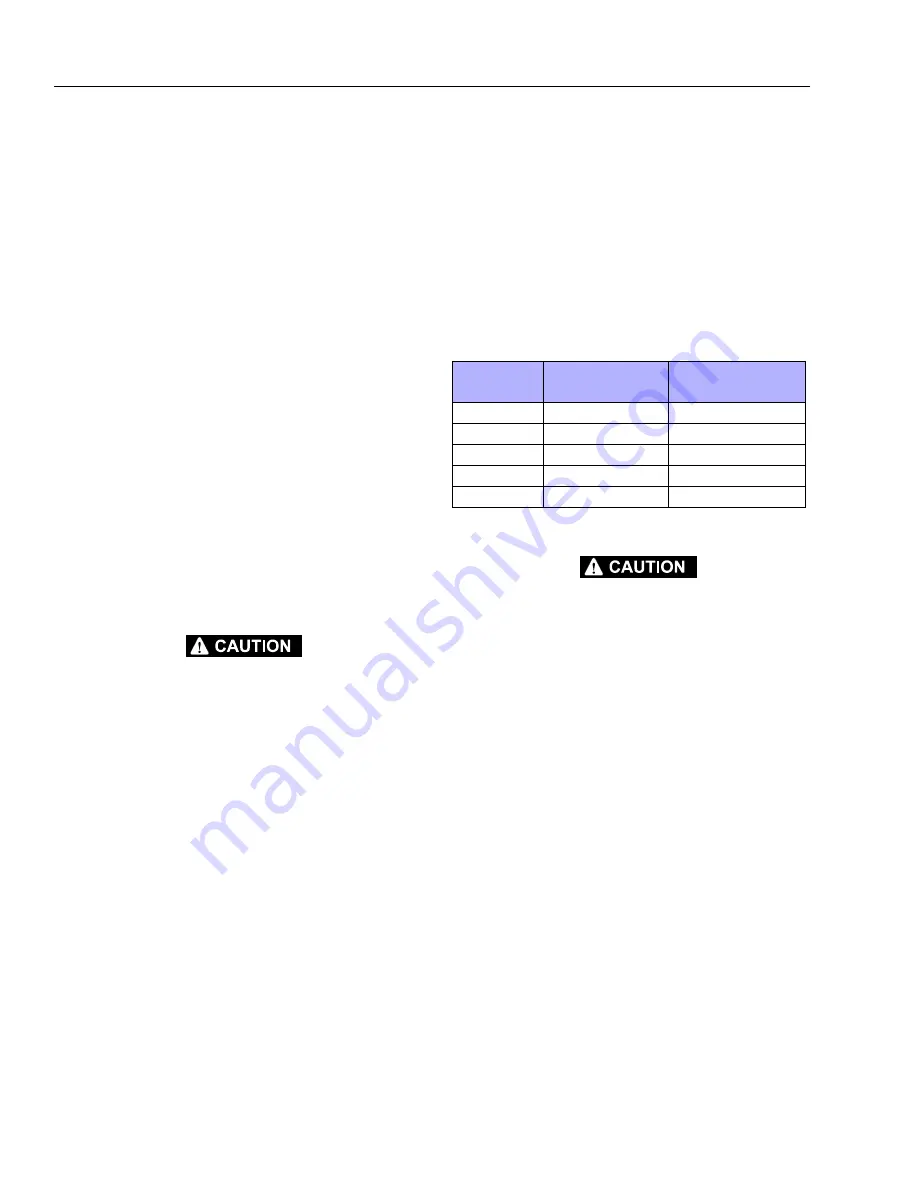
SECTION 3 - CHASSIS & TURNTABLE
3-24
3121234
Spindle Brake Sub-Assembly
NOTE:
Refer to Figure 3-17., Spindle Brake Sub-Assembly.
NOTE:
This procedure applies only to units with integral input
brake (2).
NOTE:
For this procedure, use the Brake Assembly Drawing (Figure
3-17.), which will show the proper balloon numbers for the
individual brake components. In the following instructions,
if the number has a “-” between two numbers, it refers to
the Brake Assembly Drawing only and NOT the Drive Hub
Assembly Drawing.
NOTE:
The Pressure Plug (12) requires a special tool for installa-
tion. It is not recommended to remove this plug unless it is
leaking. The plug is called a Koenig Expander. The installa-
tion tool is not supplied by Fairfield manufacturing, but
can be supplied by the manufacturer of the Koenig
Expander, Sherex Industries, or one of their distributors.
1.
Install Pressure Plug (12) into Spindle (1A) using follow-
ing procedure:
a.
Clean hole in spindle using appropriate Loctite
spray.
b.
Dip collar of plug in Loctite 290 or 680 (keep
unplugged portion of hole free of Loctite).
c.
Using appropriate tool, install plug flush with sur-
face of spindle.
SAFETY GLASSES MUST BE WORN DURING THE NEXT STEP.
2.
Place Spindle (1A) such that the splined end is facing
down. Using appropriate tool (See back of manual),
install Retaining Ring (2-1) into the spindle groove
within the splines.
3.
Place Washer (2-10) on top of Retaining Ring (2-1).
4.
Place Stator (2-9) on top of Washer (2-10).
5.
Place Rotor (2-12) on top of Stator (2-9).
6.
Repeat steps 3 & 4 until there are a total of 8 Stators (2-9)
and 7 Rotors (2-12) installed.
7.
Place Piston (2-8) such that the smaller O.D. end is facing
upward.
8.
Grease the large Backup Ring (2-3) and install in the
large-diameter groove at the bottom of the Piston (2-8).
9.
Grease the large O-Ring (2-2) and install in the large-
diameter groove at the bottom of the Piston (2-8), on
top of the large Backup Ring (2-3).
10.
Grease the small O-Ring (2-5) and install in the small-
diameter groove near the top of the Piston (2-8). Make
sure the o-ring is seated on the bottom of the groove.
11.
Grease the small Backup Ring (2-4) and install in the
small-diameter groove near the top of the Piston (2-8),
on top of the small O-Ring (2-5).
NOTE:
If piston comes pre-assembled with shipping bolts (2-11),
skip to Step 15.
12.
Insert Piston (2-8) into Spindle (1A) until it contacts the
Stator (2-9).
13.
Insert the appropriate number of Springs (2-13) into Pis-
ton (2-8) counterbore. Use the brake spring chart below
and a bill of materials for your particular model number
to determine the number of springs.
14.
Place Pressure Plate (2-7) on top of Springs (2-13).
SAFETY GLASSES MUST BE WORN DURING THE NEXT TWO STEPS.
15.
Using snap ring pliers, install Retaining Ring (2-6) into
groove in Spindle (1A) and on top of Pressure Plate (2-7).
Make sure that Retaining Ring (2-6) is seated properly in
the groove.
16.
Remove Shipping Bolts (2-11) in brake pressure plate to
release springs in brake. Before removing bolts, use the
Coupling (9) (See Assembly Drawing at back of manual)
to center and align the Brake Rotors (2-12) with the Spin-
dle (1A).
BRAKE
CODE
BRAKE P/N
NUMBER
OF SPRINGS
A
902337
12
B
902341
10
C
902342
8
D
902343
6
E
902345
9
Summary of Contents for 680S
Page 2: ......
Page 52: ...SECTION 2 GENERAL 2 14 3121234 NOTES...
Page 55: ...SECTION 3 CHASSIS TURNTABLE 3121234 3 3 This page left blank intentionally...
Page 89: ...SECTION 3 CHASSIS TURNTABLE 3121234 3 37 Figure 3 28 Assembly Tools Seal Pressing...
Page 139: ...SECTION 3 CHASSIS TURNTABLE 3121234 3 87 Figure 3 62 Swing Hub Prior to SN 0300134352...
Page 143: ...SECTION 3 CHASSIS TURNTABLE 3121234 3 91 Figure 3 64 Swing Brake...
Page 205: ...SECTION 3 CHASSIS TURNTABLE 3121234 3 153 This page left blank intentionally...
Page 208: ...SECTION 3 CHASSIS TURNTABLE 3 156 3121234 Figure 3 91 Generator Electrical Circuit Diagram...
Page 224: ...SECTION 3 CHASSIS TURNTABLE 3 172 3121234 Figure 3 103 EMR 2 Engine Side Equipment...
Page 225: ...SECTION 3 CHASSIS TURNTABLE 3121234 3 173 Figure 3 104 Deutz EMR 2 Troubleshooting Flow Chart...
Page 229: ...SECTION 3 CHASSIS TURNTABLE 3121234 3 177 Figure 3 108 EMR 2 Engine Plug Pin Identification...
Page 230: ...SECTION 3 CHASSIS TURNTABLE 3 178 3121234 Figure 3 109 EMR 2 Vehicle Plug Pin Identification...
Page 231: ...SECTION 3 CHASSIS TURNTABLE 3121234 3 179 Figure 3 110 EMR2 Fault Codes Sheet 1 of 5...
Page 232: ...SECTION 3 CHASSIS TURNTABLE 3 180 3121234 Figure 3 111 EMR2 Fault Codes Sheet 2 of 5...
Page 233: ...SECTION 3 CHASSIS TURNTABLE 3121234 3 181 Figure 3 112 EMR2 Fault Codes Sheet 3 of 5...
Page 234: ...SECTION 3 CHASSIS TURNTABLE 3 182 3121234 Figure 3 113 EMR2 Fault Codes Sheet 4 of 5...
Page 235: ...SECTION 3 CHASSIS TURNTABLE 3121234 3 183 Figure 3 114 EMR2 Fault Codes Sheet 5 of 5...
Page 264: ...SECTION 3 CHASSIS TURNTABLE 3 212 3121234 NOTES...
Page 285: ...SECTION 4 BOOM PLATFORM 3121234 4 21 This page left blank intentionally...
Page 333: ...SECTION 4 BOOM PLATFORM 3121234 4 69 Figure 4 25 Load Sensing Device...
Page 336: ...SECTION 4 BOOM PLATFORM 4 72 3121234 NOTES...
Page 416: ...SECTION 5 BASIC HYDRAULICS INFORMATION SCHEMATICS 5 80 3121234 NOTES...
Page 423: ...SECTION 6 JLG CONTROL SYSTEM 3121234 6 7 Figure 6 2 ADE Block Diagram...
Page 480: ...SECTION 6 JLG CONTROL SYSTEM 6 64 3121234 NOTES...
Page 528: ...SECTION 7 BASIC ELECTRICAL INFORMATION SCHEMATICS 7 48 3121234 NOTES...
Page 529: ......