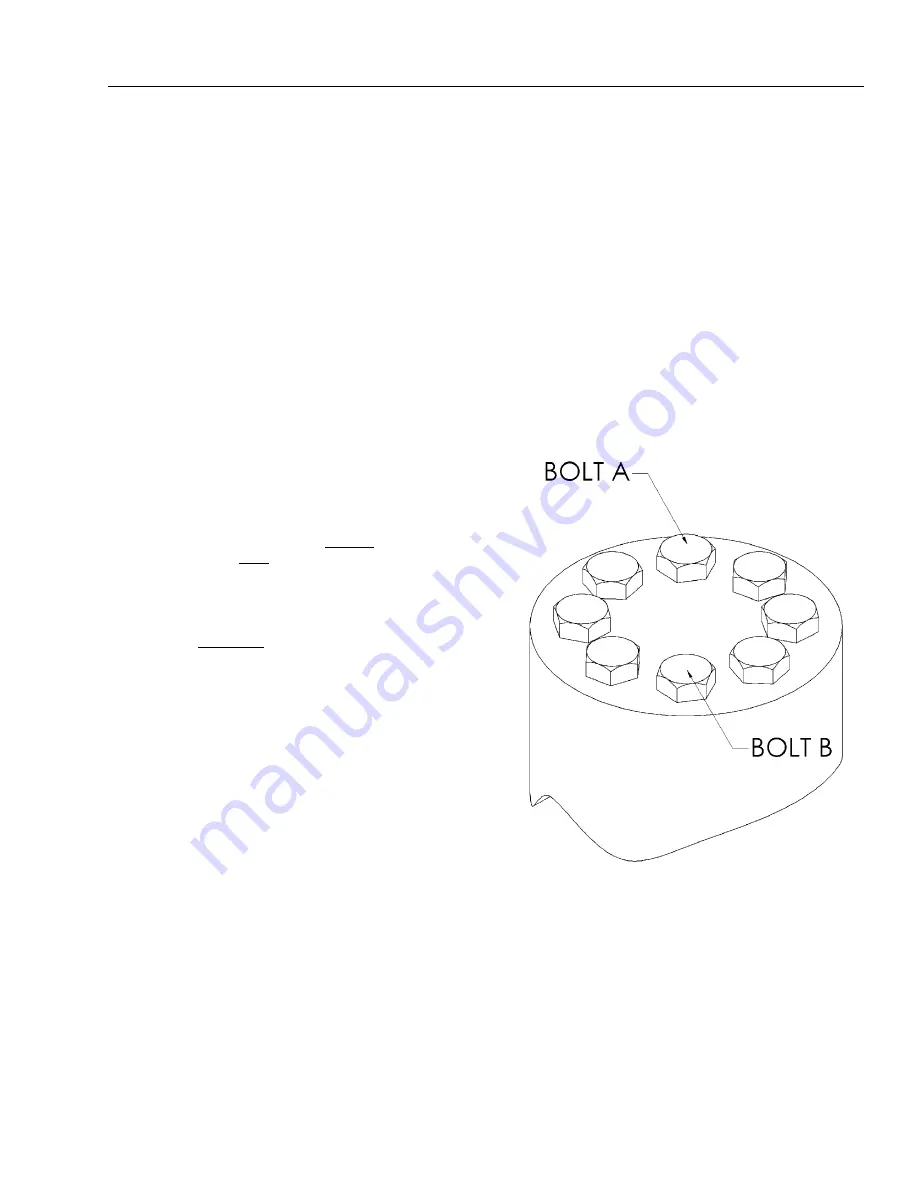
SECTION 3 - CHASSIS & TURNTABLE
3121234
3-13
3.6
DRIVE HUB (4WD MACHINES W/ INTEGRAL
BRAKE)
Roll, Leak and Brake Testing
Drive Hub units should always be roll and leak tested before
disassembly and after assembly to make sure that the unit's
gears, bearings and seals are working properly. The following
information briefly outlines what to look for when performing
these tests.
NOTE:
The brake must be released before performing the roll test.
This can be accomplished by either pressurizing the brake
using the Brake Leak Test procedure below or by tightening
the bolts into the piston through the end plate (See Brake
Disassembly Procedure).
NOTE:
Bolts must be removed while performing brake release test.
THE ROLL TEST
The purpose of the roll test is to determine if the unit's gears
are rotating freely and properly. You should be able to rotate
the gears in your unit by applying constant force to the roll
checker. If you feel more drag in the gears only at certain
points, then the gears are not rolling freely and should be
examined for improper installation or defects. Some gear
packages roll with more difficulty than others. Do not be con-
cerned if the gears in your unit seem to roll hard as long as
they roll with consistency.
THE LEAK TEST (MAIN UNIT)
The purpose of a leak test is to make sure the unit is air tight.
You can tell if your unit has a leak if the pressure gauge read-
ing on your leak checking fitting starts to fall after the unit has
been pressurized and allowed to equalize. Leaks will most
likely occur at the pipe plugs, the main seal or wherever
o-rings or gaskets are located. The exact location of a leak can
usually be detected by brushing a soap and water solution
around the main seal and where the o-rings or gaskets meet
on the exterior of the unit, then checking for air bubbles. If a
leak is detected in a seal, o-ring or gasket, the part must be
replaced, and the unit rechecked. Leak test at 10 psi for 20
minutes.
THE BRAKE TEST
Input Brake - 1,850 in. lbs. (208 Nm) Static,
225 psi (15.5 bar) Full Release,
3000 psi (207 bar) maximum o-ring check.
If brake does not release at these pressure values, brake has to
be inspected, repaired or replaced.
NOTE:
Failure to perform this test may result in damaged or inef-
fective brake parts.
Tightening and Torquing Bolts
If an air impact wrench is used to tighten bolts, extreme care
should be taken to ensure that the bolts are not tightened
beyond their specified torque.
The following steps describe how to tighten and torque bolts
or socket head capscrews in a bolt circle.
1.
Tighten (but do not torque) bolt “A" until snug.
2.
Go to the opposite side of the bolt circle and tighten
bolt "B" until equally snug.
3.
Crisscross around the bolt circle and tighten remaining
bolts.
4.
Now use a torque wrench to apply the specified torque
to bolt "A".
5.
Using the same sequence, crisscross around the bolt cir-
cle and apply an equal torque to the remaining bolts.
Summary of Contents for 680S
Page 2: ......
Page 52: ...SECTION 2 GENERAL 2 14 3121234 NOTES...
Page 55: ...SECTION 3 CHASSIS TURNTABLE 3121234 3 3 This page left blank intentionally...
Page 89: ...SECTION 3 CHASSIS TURNTABLE 3121234 3 37 Figure 3 28 Assembly Tools Seal Pressing...
Page 139: ...SECTION 3 CHASSIS TURNTABLE 3121234 3 87 Figure 3 62 Swing Hub Prior to SN 0300134352...
Page 143: ...SECTION 3 CHASSIS TURNTABLE 3121234 3 91 Figure 3 64 Swing Brake...
Page 205: ...SECTION 3 CHASSIS TURNTABLE 3121234 3 153 This page left blank intentionally...
Page 208: ...SECTION 3 CHASSIS TURNTABLE 3 156 3121234 Figure 3 91 Generator Electrical Circuit Diagram...
Page 224: ...SECTION 3 CHASSIS TURNTABLE 3 172 3121234 Figure 3 103 EMR 2 Engine Side Equipment...
Page 225: ...SECTION 3 CHASSIS TURNTABLE 3121234 3 173 Figure 3 104 Deutz EMR 2 Troubleshooting Flow Chart...
Page 229: ...SECTION 3 CHASSIS TURNTABLE 3121234 3 177 Figure 3 108 EMR 2 Engine Plug Pin Identification...
Page 230: ...SECTION 3 CHASSIS TURNTABLE 3 178 3121234 Figure 3 109 EMR 2 Vehicle Plug Pin Identification...
Page 231: ...SECTION 3 CHASSIS TURNTABLE 3121234 3 179 Figure 3 110 EMR2 Fault Codes Sheet 1 of 5...
Page 232: ...SECTION 3 CHASSIS TURNTABLE 3 180 3121234 Figure 3 111 EMR2 Fault Codes Sheet 2 of 5...
Page 233: ...SECTION 3 CHASSIS TURNTABLE 3121234 3 181 Figure 3 112 EMR2 Fault Codes Sheet 3 of 5...
Page 234: ...SECTION 3 CHASSIS TURNTABLE 3 182 3121234 Figure 3 113 EMR2 Fault Codes Sheet 4 of 5...
Page 235: ...SECTION 3 CHASSIS TURNTABLE 3121234 3 183 Figure 3 114 EMR2 Fault Codes Sheet 5 of 5...
Page 264: ...SECTION 3 CHASSIS TURNTABLE 3 212 3121234 NOTES...
Page 285: ...SECTION 4 BOOM PLATFORM 3121234 4 21 This page left blank intentionally...
Page 333: ...SECTION 4 BOOM PLATFORM 3121234 4 69 Figure 4 25 Load Sensing Device...
Page 336: ...SECTION 4 BOOM PLATFORM 4 72 3121234 NOTES...
Page 416: ...SECTION 5 BASIC HYDRAULICS INFORMATION SCHEMATICS 5 80 3121234 NOTES...
Page 423: ...SECTION 6 JLG CONTROL SYSTEM 3121234 6 7 Figure 6 2 ADE Block Diagram...
Page 480: ...SECTION 6 JLG CONTROL SYSTEM 6 64 3121234 NOTES...
Page 528: ...SECTION 7 BASIC ELECTRICAL INFORMATION SCHEMATICS 7 48 3121234 NOTES...
Page 529: ......