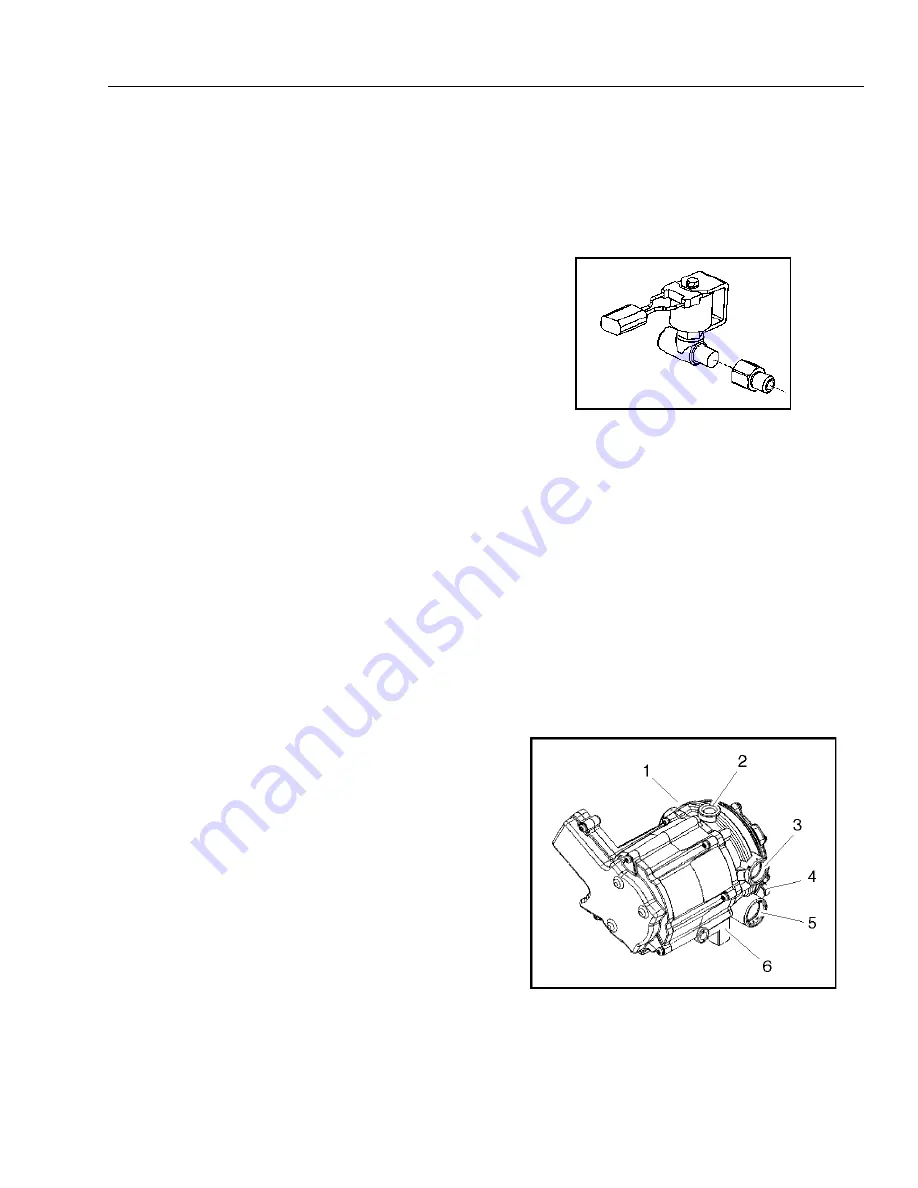
SECTION 3 - CHASSIS & TURNTABLE
3121234
3-187
3.27
GM ENGINE DUAL FUEL SYSTEM
The Dual Fuel system allows the operator to operate the vehi-
cle on either gasoline or LPG by positioning a selector switch
in the operator's platform. When the operator places the selec-
tor switch in the gasoline mode the gasoline fuel pump is
energized. While in the gasoline mode the LPG fuel lock-off is
isolated and will not energize. In addition the gasoline injector
circuit is enabled and injector pulses are provided to each
injector and the ECM calibration for gasoline is also enabled.
When the operator selects the LPG mode the Low Pressure
LPG lock-off is energized and fuel from the LPG tank flows to
the Electronic Pressure Regulator (EPR). The EPR receives an
electronic signal to position the secondary lever for the start or
run positions and when the engine begins to crank the mixer
air valve will rise and fuel will begin flowing to engine. During
this mode the gasoline fuel pump is isolated and will not be
activated. The primary components of the gasoline dual fuel
system are the gasoline tank, electric fuel pump and filter, fuel
supply line, injector rail and injectors and the fuel pressure
regulator. The primary components of the LPG dual fuel sys-
tem are the LPG fuel tank, in-fuel filter, LPG Low Pressure lock-
off, Electronic Pressure Regulator (EPR) and the fuel mixer
module. The LPG fuel system operates at pressures which
range from 14.0 in. (355.60 mm) of water column up to 312 psi
(21.5 bar).
Components which are shared by both systems include the
Electronic Throttle Control and the ECM. The ECM contains a
dual calibration; one controls the gasoline fuel system during
gasoline operation and one controls the LPG fuel system
during LPG operation.
Fuel Filter
Propane fuel like all other motor fuels is subject to contamina-
tion from outside sources. Refueling of the equipment’s tank
and removal of the tank from the equipment can inadver-
tently introduce dirt and other foreign matter into the fuel sys-
tem. It is therefore necessary to filter the fuel prior to entering
the fuel system components downstream of the tank. An
inline fuel filter has been installed in the fuel system to remove
the dirt and foreign matter from the fuel. The inline filter is
replaceable as a unit only. Maintenance of the filter is critical to
proper operation of the fuel system and should be replaced as
Section 1. In severe operating condition more frequent
replacement of the filter may be necessary.
Electric Lock Off
The Electric Lock Off device is an integrated assembly. When
energized the solenoid opens the valve and allows the Pro-
pane fuel to flow through the device. The valve opens during
cranking and run cycles of the engine. The lock off supply volt-
age is controlled by the engine control module (ECM).
EPR Assembly
The EPR assembly is a combination Low Pressure Regulator
and a Voice Coil Assembly. The Voice coil is an electronic actu-
ator which is controlled by an internal microprocessor. The
microprocessor provides output data to the ECM and receives
input data over a CAN BUS connection. The internal micropro-
cessor receives electrical signals from the Fuel Pressure Sensor
FPS and the Fuel Temperature Pressure FTP and communi-
cates the data to the ECM. The ECM uses the FPS and FTP data
to calculate the location of the secondary lever in the LPR and
sends that data back to the EPR via the CAN BUS. The internal
microprocessor in the EPR will then output a signal, which
causes the voice coil to move and position the secondary lever
to the correct location.
Figure 3-116. Electric Fuel Lock Off
1.
Pressure Regulator Section
2. Fuel Inlet
3. Coolant Passage
4. Primary Test Port
5. Secondary Test
Port
6. Voice Coil Section
Figure 3-117. EPR Assembly
Summary of Contents for 680S
Page 2: ......
Page 52: ...SECTION 2 GENERAL 2 14 3121234 NOTES...
Page 55: ...SECTION 3 CHASSIS TURNTABLE 3121234 3 3 This page left blank intentionally...
Page 89: ...SECTION 3 CHASSIS TURNTABLE 3121234 3 37 Figure 3 28 Assembly Tools Seal Pressing...
Page 139: ...SECTION 3 CHASSIS TURNTABLE 3121234 3 87 Figure 3 62 Swing Hub Prior to SN 0300134352...
Page 143: ...SECTION 3 CHASSIS TURNTABLE 3121234 3 91 Figure 3 64 Swing Brake...
Page 205: ...SECTION 3 CHASSIS TURNTABLE 3121234 3 153 This page left blank intentionally...
Page 208: ...SECTION 3 CHASSIS TURNTABLE 3 156 3121234 Figure 3 91 Generator Electrical Circuit Diagram...
Page 224: ...SECTION 3 CHASSIS TURNTABLE 3 172 3121234 Figure 3 103 EMR 2 Engine Side Equipment...
Page 225: ...SECTION 3 CHASSIS TURNTABLE 3121234 3 173 Figure 3 104 Deutz EMR 2 Troubleshooting Flow Chart...
Page 229: ...SECTION 3 CHASSIS TURNTABLE 3121234 3 177 Figure 3 108 EMR 2 Engine Plug Pin Identification...
Page 230: ...SECTION 3 CHASSIS TURNTABLE 3 178 3121234 Figure 3 109 EMR 2 Vehicle Plug Pin Identification...
Page 231: ...SECTION 3 CHASSIS TURNTABLE 3121234 3 179 Figure 3 110 EMR2 Fault Codes Sheet 1 of 5...
Page 232: ...SECTION 3 CHASSIS TURNTABLE 3 180 3121234 Figure 3 111 EMR2 Fault Codes Sheet 2 of 5...
Page 233: ...SECTION 3 CHASSIS TURNTABLE 3121234 3 181 Figure 3 112 EMR2 Fault Codes Sheet 3 of 5...
Page 234: ...SECTION 3 CHASSIS TURNTABLE 3 182 3121234 Figure 3 113 EMR2 Fault Codes Sheet 4 of 5...
Page 235: ...SECTION 3 CHASSIS TURNTABLE 3121234 3 183 Figure 3 114 EMR2 Fault Codes Sheet 5 of 5...
Page 264: ...SECTION 3 CHASSIS TURNTABLE 3 212 3121234 NOTES...
Page 285: ...SECTION 4 BOOM PLATFORM 3121234 4 21 This page left blank intentionally...
Page 333: ...SECTION 4 BOOM PLATFORM 3121234 4 69 Figure 4 25 Load Sensing Device...
Page 336: ...SECTION 4 BOOM PLATFORM 4 72 3121234 NOTES...
Page 416: ...SECTION 5 BASIC HYDRAULICS INFORMATION SCHEMATICS 5 80 3121234 NOTES...
Page 423: ...SECTION 6 JLG CONTROL SYSTEM 3121234 6 7 Figure 6 2 ADE Block Diagram...
Page 480: ...SECTION 6 JLG CONTROL SYSTEM 6 64 3121234 NOTES...
Page 528: ...SECTION 7 BASIC ELECTRICAL INFORMATION SCHEMATICS 7 48 3121234 NOTES...
Page 529: ......