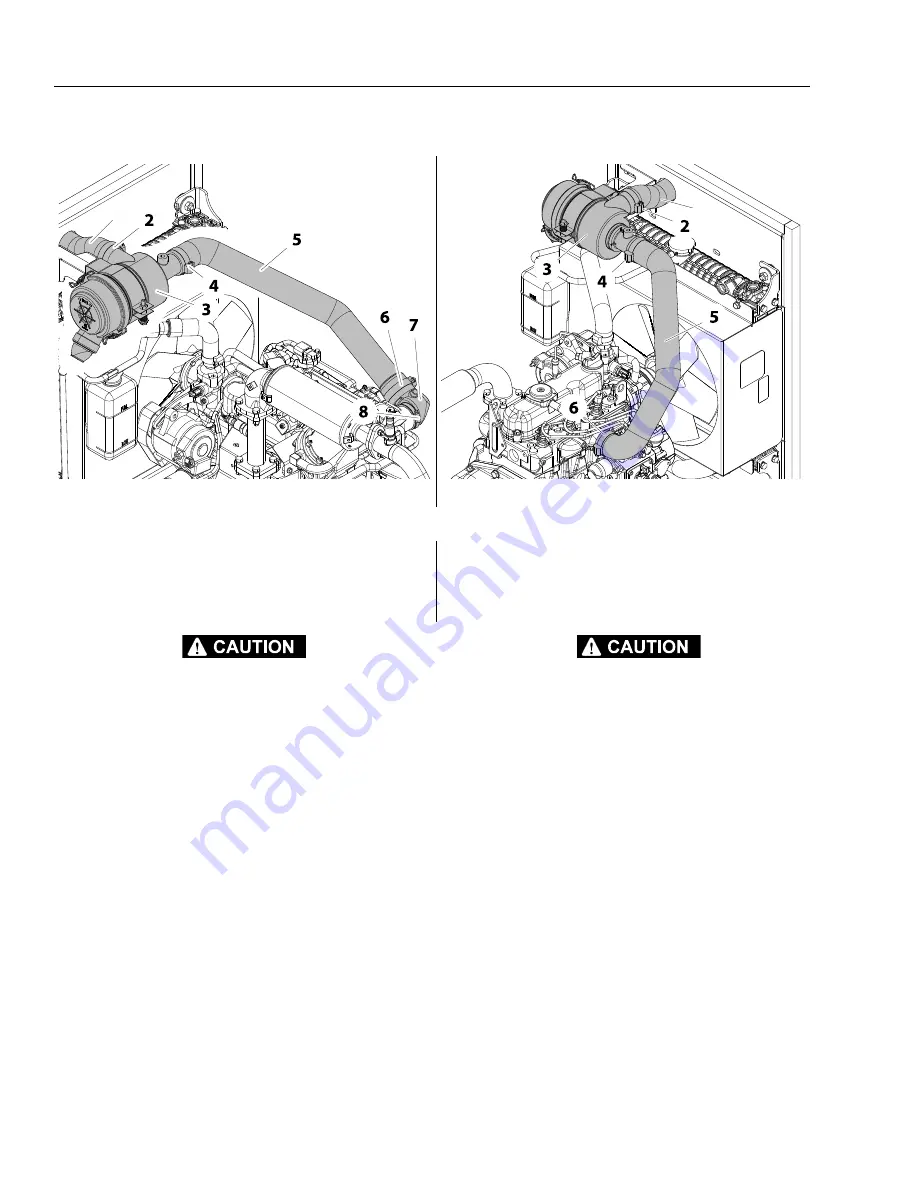
SECTION 3 - CHASSIS, PLATFORM, & SCISSOR ARMS
3-64
31215079
Air Cleaner System
ALLOW ENGINE AND COMPONENTS TO COOL DOWN BEFORE SERVIC-
ING.
REMOVAL
1. Disable machine operation. If necessary, swing
engine tray out for better access to components.
2. Loosen the clamp (4) and (8) attaching the intake
pipe to the air cleaner assembly (3) and engine
intake manifold. Disconnect the intake pipe from the
air cleaner assembly and remove the complete
intake pipe from the engine assembly.
3. To remove the air cleaner assembly (3) from the air
cleaner bracket clamp, Unscrew the main clamp
screw on the clamp until the air cleaner is loose in
the bracket. Release the latches on the end and
remove the end cap from the air cleaner assembly.
Slide the air cleaner assembly with inlet hose out of
the bracket clamp.
NOTE:
The filter element can be removed from the air
cleaner by releasing the latches on the end of the air
cleaner. Replace filter element as needed. See Section
2.5, Service Maintenance Components.
INSTALLATION
1. Follow Removal Steps in reverse.
ALLOW ENGINE AND COMPONENTS TO COOL DOWN BEFORE SERVIC-
ING.
REMOVAL
1. Disable machine operation. If necessary, swing
engine tray out for better access to components.
2. Loosen the clamp (4) and (6) attaching the intake
pipe to the air cleaner assembly (3) and engine
intake manifold. Disconnect the intake pipe from the
air cleaner assembly and remove the complete
intake pipe from the engine assembly.
3. To remove the air cleaner assembly (3) from the air
cleaner bracket clamp, Unscrew the main clamp
screw on the clamp until the air cleaner is loose in
the bracket. Release the latches on the end and
remove the end cap from the air cleaner assembly.
Slide the air cleaner assembly with inlet hose out of
the bracket clamp.
NOTE:
The filter element can be removed from the air
cleaner by releasing the latches on the end of the air
cleaner. Replace filter element as needed. See Section
2.5, Service Maintenance Components.
INSTALLATION
1. Follow Removal Steps in reverse.
Dual Fuel - Gas/LPG
Diesel
Figure 3-54. Air Cleaner System (Kubota Engine)
1. Inlet Hose
2. Clamp
3. Air Cleaner Assy.
4. Clamp
5. Intake Pipe
6. Clamp
7. 90° Elbow
8. Clamp
1. Inlet Hose
2. Clamp
3. Air Cleaner Assy.
4. Clamp
5. Intake Pipe
6. Clamp
1
1
Go
to
Discount-Equipment.com
to
order
your
parts