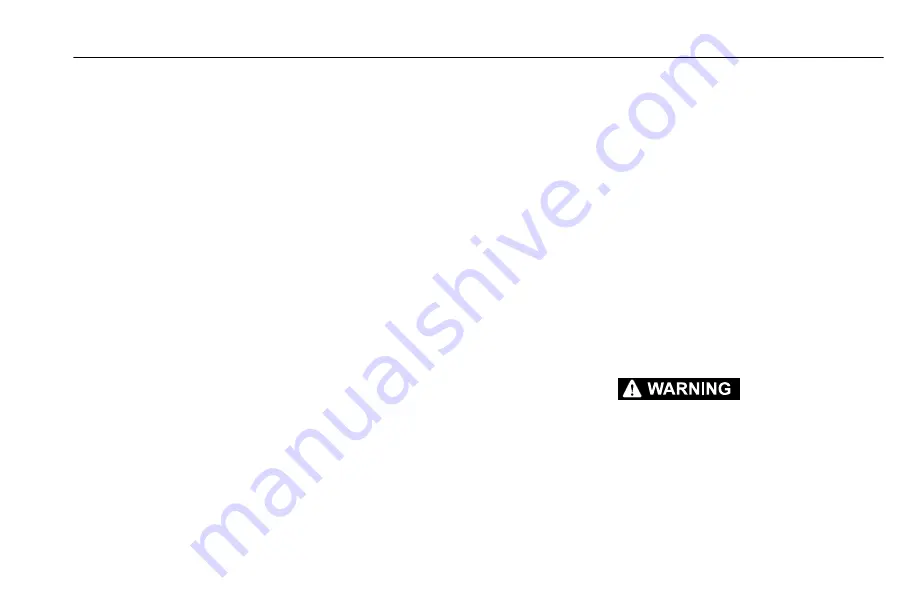
SECTION 5 - GENERAL SPECIFICATIONS AND OPERATOR MAINTENANCE
3121230
– JLG Lift –
5-9
5.3 OPERATOR MAINTENANCE
Battery
The OEM batteries are AGM sealed (VRLA) type so the electro-
lyte level cannot be serviced, however the battery terminals
should be checked periodically for corrosion and tightness.
The batteries are located under the top rear hood covers on
each side of the Ground Control Station.
Tires and Wheels
Tire Wear and Damage
Inspect tires periodically for wear or damage. Tires with worn
edges or distorted profiles require replacement. Tires with sig-
nificant damage in the tread area or side wall, require immedi-
ate evaluation before replacing the machine into service.
Wheel and Tire Replacement
Replacement wheels must have the same diameter and pro-
file as the original. Replacement tires must be the same size
and rating as the tire being replaced.
Wheel Installation
It is extremely important to apply and maintain proper wheel
mounting torque.
WHEEL LUG NUTS MUST BE INSTALLED AND MAINTAINED AT THE
PROPER TORQUE TO PREVENT LOOSE WHEELS, BROKEN LUG NUTS,
AND POSSIBLE SEPARATION OF WHEEL FROM THE AXLE. BE SURE TO
USE ONLY THE LUG NUTS MATCHED TO THE CONE ANGLE OF THE
WHEEL.
Summary of Contents for 15MSP Series
Page 80: ...SECTION 4 EMERGENCY PROCEDURES 4 2 JLG Lift 3121230 NOTES...
Page 102: ...SECTION 5 GENERAL SPECIFICATIONS AND OPERATOR MAINTENANCE 5 22 JLG Lift 3121230 NOTES...
Page 106: ......
Page 107: ......