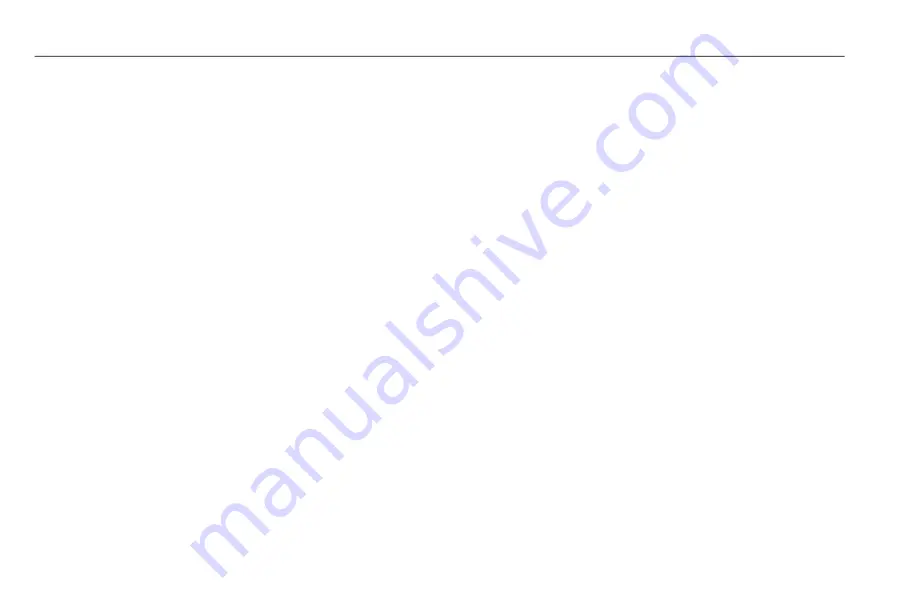
SECTION 1 - SAFETY PRECAUTIONS
1-10
3121789
1.5
MOVING, LIFTING AND REPOSITIONING
General
•
Never allow personnel in platform while moving, lifting or reposi
-
tioning the machine.
•
This machine shall not be towed by a vehicle.
•
Do not move assembled unit on wheels over soft or uneven sur
-
faces, or over obstructions, bumps, debris, etc.
•
Disassemble unit to transport over uneven or sloped ground, or in
a vehicle.
•
Ensure platform is fully retracted and completely empty of tools
prior to disassembly, lifting or hauling.
•
Refer to the Machine Operation section of this manual for lifting
information.
Additional Safety Information
•
Do not use machine as ground for welding.
1.6 MAINTENANCE
This sub-section contains general safety precautions which must be
observed during maintenance of this machine. Additional precau
-
tions to be observed during machine maintenance are inserted at
the appropriate points in this manual and in the Service and Mainte
-
nance section of this manual. It is of utmost importance that main
-
tenance personnel pay strict attention to these precautions to avoid
possible injury to personnel or damage to the machine or property.
A maintenance program must be established by a qualified person
and must be followed to ensure that the machine is safe.
Maintenance Hazards
•
Shut off power to all controls and ensure that all moving parts are
secured from inadvertent motion prior to performing any adjust
-
ments or repairs.
•
Never work under an elevated platform until it has been fully low
-
ered to the full down position, if possible, or otherwise supported
and restrained from movement with appropriate safety props,
blocking, or overhead supports.
•
DO NOT attempt to repair or tighten any hydraulic hoses or fittings
while the machine is powered on or when the hydraulic system is
under pressure.
Summary of Contents for 1030P
Page 6: ...FOREWORD d 3121789 REVISION LOG Original Issue A XX XX 2020...
Page 20: ...SECTION 1 SAFETY PRECAUTIONS 1 12 3121789 NOTES...
Page 28: ...SECTION 2 PREPARATION AND INSPECTION 2 8 3121789 NOTES...
Page 38: ...SECTION 3 MACHINE OPERATION 3 10 3121789 Transportation Diagram OAD00680...
Page 44: ...SECTION 4 EMERGENCY PROCEDURES 4 4 3121789 NOTES...
Page 52: ...SECTION 5 SPECIFICATIONS OPERATOR MAINTENANCE 5 8 3121789 NOTES...
Page 55: ......