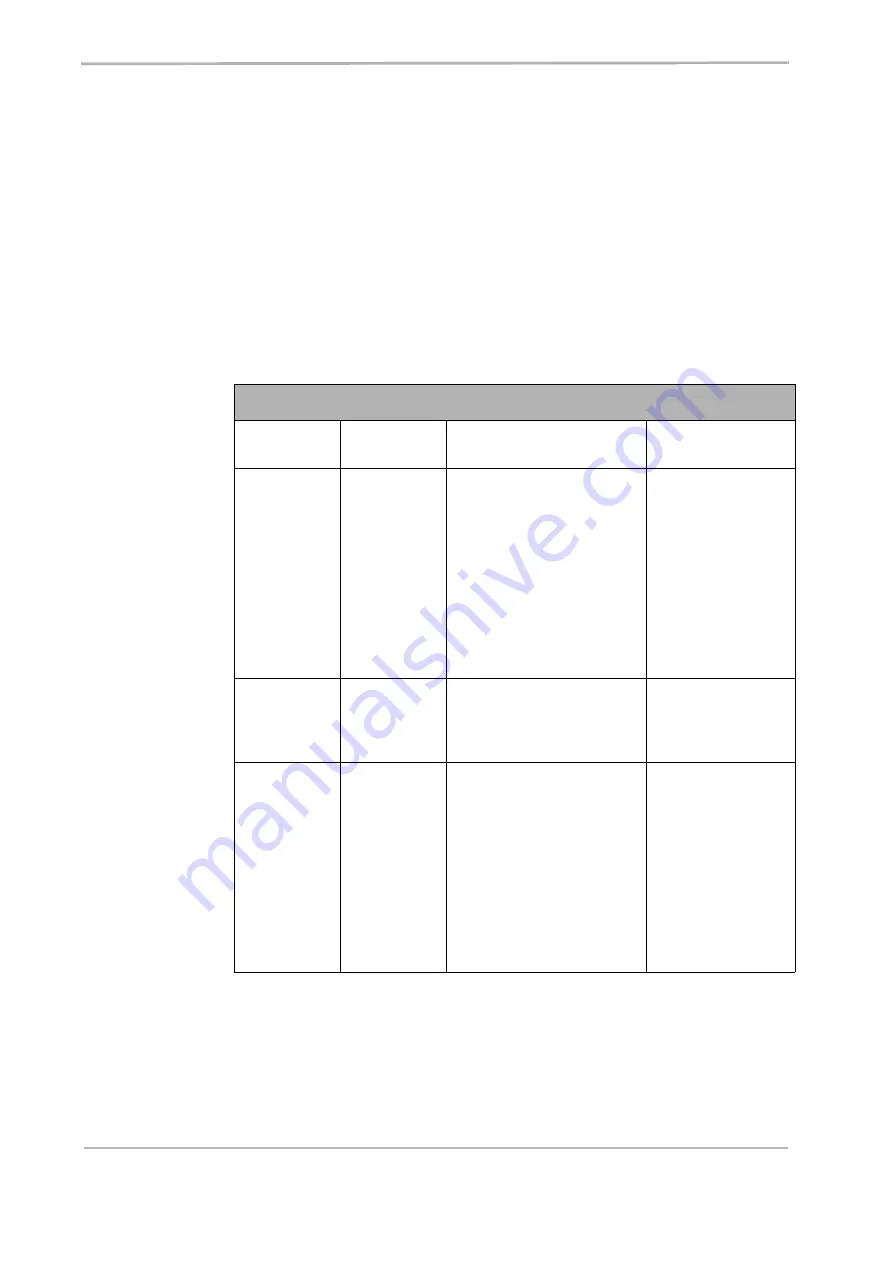
7 Description of Connections
74
Jetter AG
7.7.2
Enable input with Option -S1
(Safe Torque Off)
Specification of terminal X73 / X83
• 3-pin screw clamping terminal (type MC 1.5/ 3-ST-3.81)
• Cross-sectional area of connecting cable: 0.14 ... 1.5 mm
2
(AWG 26 - AWG 16)
with bootlace ferrules in a plastic sleeve: 0.25 ... 0.5 mm
2
(AWG 24 - AWG 20)
• Bladed screw-driver: 0.4 x 2.5 mm
• Stud torque for the screw clamping terminal: 0.22 Nm (1.95 lbf-inch)
Please refer to chapter 11 "Option -S1: STO", page 91
Connections see “Connection Diagrams”, page 87.
7.8
JX2 System Bus
Inputs for Enable: X73 / X83
Terminals
X73 / X 83
Signal
Description
Specification
ENABLE1
Hardware
enable for
the power
supply of the
motor
(Input)
• At this input, a high
signal is necessary for
power supply of the
motor. This signal must
have been applied
before carrying out the
software enable.
• A low signal de-
energizes the motor
after 1 ms (OSSD
filtering).
• DC 24 V
• max. 50 mA
• Operating point:
< 6 V low,
> 15 V high
COM
Common
ground
The ground reference of the
inputs for enable is
potentially isolated from the
ground of the controller.
Ground for the
enable-inputs
ENABLE2
Hardware
enable for
the power
supply of the
motor (input)
• At this input, a high
signal is necessary for
power supply of the
motor. This signal must
have been applied
before carrying out the
software enable.
• A low signal de-
energizes the motor
after 1 ms (OSSD
filtering).
• DC 20 ... 30 V
• 50 mA max.
• Operating point:
< 6 V low,
> 15 V high
Summary of Contents for JetMove D203
Page 1: ...User Manual JM D203 230 Digital Servoamplifier 60870727 We automate your success...
Page 10: ...Table of Contents 10 Jetter AG...
Page 36: ...4 Physical Dimensions 36 Jetter AG...
Page 46: ...5 Technical Data 46 Jetter AG...
Page 92: ...11 Option S1 STO 92 Jetter AG...
Page 133: ...JetMove D203 Appendix Jetter AG 133 Appendices...
Page 134: ...Appendices 134 Jetter AG...