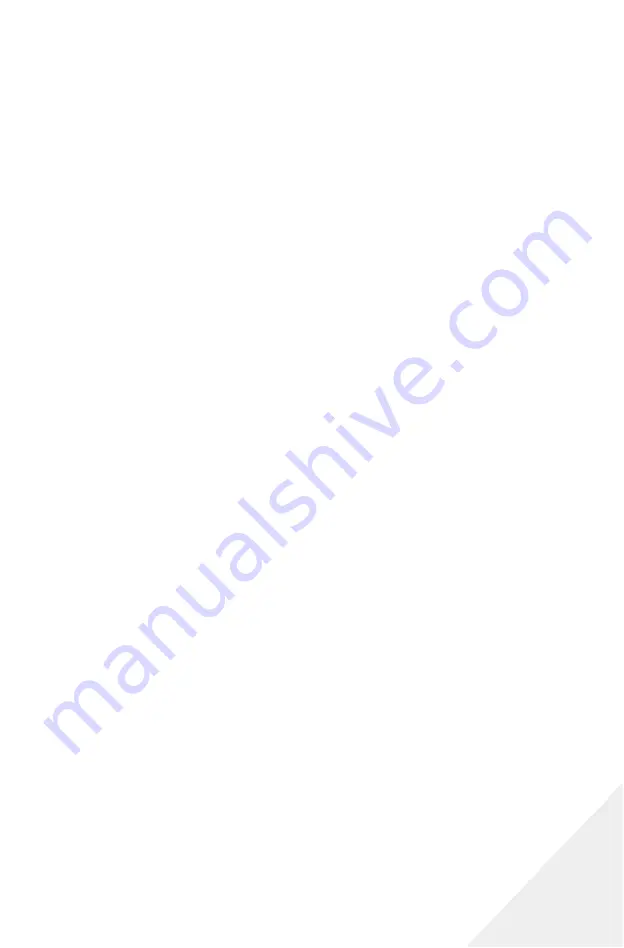
17
PI-078
June 2021
Section 4: Setup
4.0 CONNECTING ROTOMAG X22
Prior to installing the Rotomag X22 onto the rigid lance or hose, flush the
system to clear any debris.
For 22,500 psi operation (9/16” MP FML Inlet)
1. Apply anti-seize compound to the threads and cone on the 3/4” MP
male connection.
2. Install the Rotomag X22 and tighten to 90 lbs. ft.
For 15,000 psi operation (NPT FML Inlet)
Use a female NPT to male 3/4” MP adapter for 15,000 psi operation.
1. Apply 3-4 wraps of Teflon thread sealant tape to the male connection
thread (NOT adapter).
2. Apply anti-seize compound over the sealant tape for protection
against galling in connection threads.
3. Tighten the connection 1-1/2 to 2 turns past hand tight. All NPT
pipe connections should have a minimum thread engagement of (4)
threads.
4. Apply anti-seize compound to the threads and cone on the male end
of the adapter.
NOTE:
Do not use Teflon tape.
5. Install the Rotomag X22 onto the adapter and tighten to 90 lbs. ft.
4.1 Prior to installing nozzles in the Rotomag X22, turn on pump and run
at low pressure to flush debris from the system. Refer to nozzle charts in
Appendix B for the proper flow rates for your application.
NOTE:
It is strongly recommended the Rotomag X22 be used with a
BALANCED (same size nozzles) combination of nozzles. Failing to do so
may reduce the life of the tool. Configurations of 2, 4, 6, or 8 nozzles are
available using the different combinations of nozzles and plugs. When
nozzles are installed in both the 90 degree and 45 degree ports the
Rotomag X22 will spin faster. There are two sets of radial ports marked
‘HS’ for high speed and ‘LS’ for low speed.