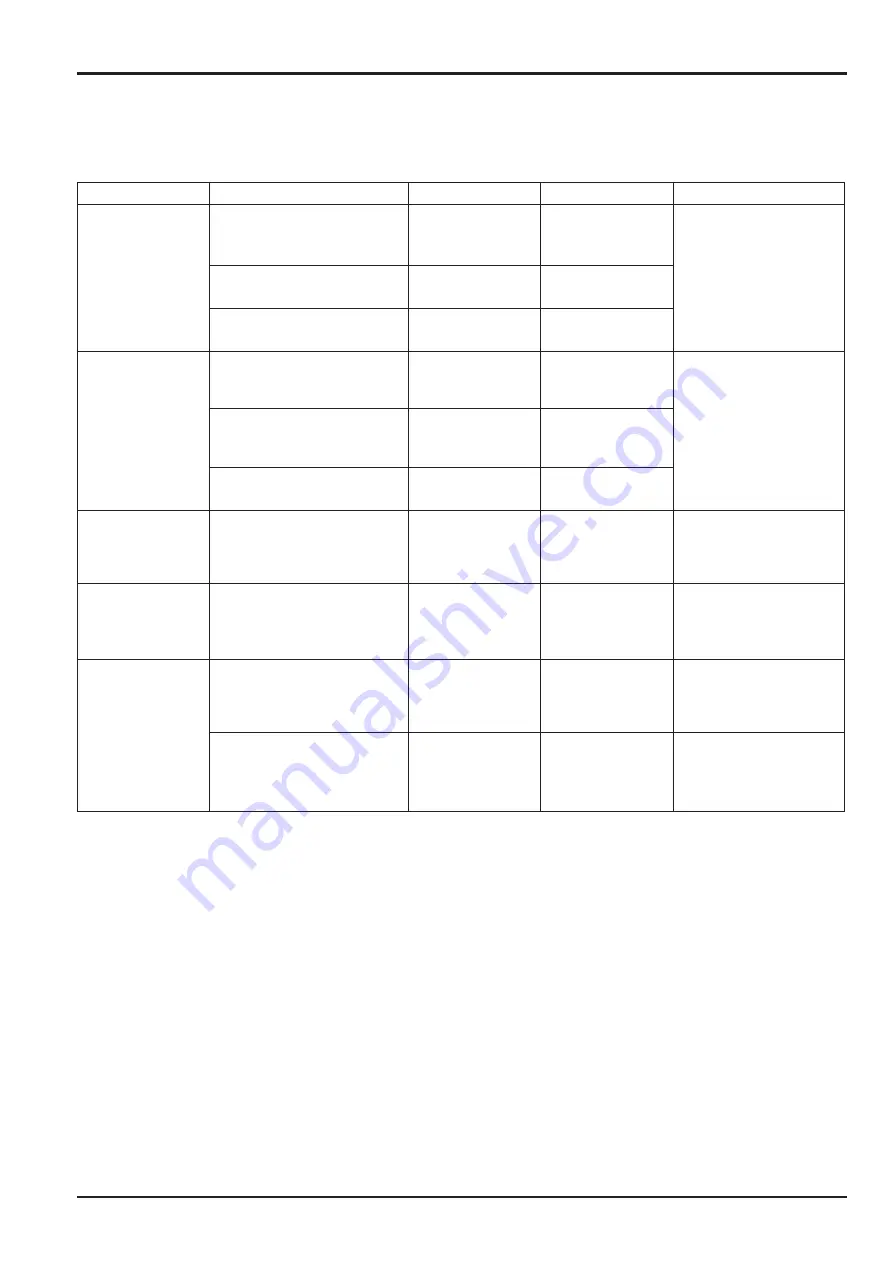
8 - 1
Section F
Transmission
9803/6400
Section F
8 - 1
Issue 2*
Motor
Maintenance Specifications
If the seals are disassembled, replace them even though no damage is observed.
Note 1
. Lap, using very fine grade paste.
Note 2
. Use very fine grade paste and lap with a steel ball.
Part Name
Appearance
Standard Value
Allowable Value
Replaceable Part
(6)
1.
Deeply scarred or rough
Cylinder block kit
Piston
surface is observed on
sliding area.
2.
The clearance to the
0.030
0.060
block bore is excessive.
3.
Backlash is excessive in
0.15
0.4
shoe ball section.
(4)
1.
Deeply scarred or rough
Roughness 0.2a
No seizure and
Cylinder block kit
Cylinder Block
surface is observed on
scar deeper
sliding area.
than 0.02mm
2.
The inside of the bore is
See note 1.
When scar
excessively worn.
cannot be completely
removed, replace.
3.
The engaged tooth is
abnormally worn or broken.
(5)
1.
Deeply scarred, thermally
Roughness 0.2a
0.8a No seizure
Cylinder block kit
Valve Plate
seized, unevenly worn or
and scar deeper
See note 1.
When scar
rough surface is observed
than 0.02mm
cannot be completely
on sliding area.
removed, replace.
(7)
1.
Deeply scarred, thermally
Roughness 0.2a
0.8a
Retainer plate kit
Retainer Plate
seized, unevenly worn or
(8)
rough surface is observed
Retainer Holder
on sliding area.
(9)
1.
Deeply scarred, thermally
Roughness 0.2a
0.8a No seizure
Swash plate steel ball
Swash Plate
seized, unevenly worn or
and scar deeper
See note 2.
When scar
rough surface is observed
than 0.02mm
cannot be completely
on sliding area.
removed, replace.
2.
Deeply pitted, thermally
Ball seating
Ball seating
Swash plate steel ball
seized on the contact
depth 14.3
depth 14.5
See note 2.
When scar
area with the steel ball.
cannot be completely
removed, replace.
*
*
*
*
*
*
*
*
Summary of Contents for JS 200 Series
Page 57: ...9 1 Section 3 Routine Maintenance 9803 6400 Section 3 9 1 Issue 2 Component Location Diagram...
Page 113: ......
Page 137: ...5 3 Section C Electrics 9803 6400 Section C 5 3 Issue 2 Pump Control FLOW CHART...
Page 201: ...10 7 Section C Electrics 9803 6400 Section C 10 7 Issue 1 CAPs II Diagnostic system K C...
Page 215: ...Section E Section E Hydraulics 9803 6400 Issue 2 3 2 3 2 Schematics...
Page 217: ...Section E Section E 9803 6400 Issue 2 3 3 3 3 Hydraulics Schematics...
Page 218: ...3 5 Section E Hydraulics 9803 6400 Section E 3 5 Issue 1 Schematics Shuttle Block JS200 JS240...
Page 232: ...10 1 Section E Hydraulics 9803 6400 Section E 10 1 Issue 1 Hydraulic Pump JS200 JS240...
Page 233: ...10 2 Section E Hydraulics 9803 6400 Section E 10 2 Issue 1 Hydraulic Pump JS200 JS240...
Page 234: ...10 3 Section E Hydraulics 9803 6400 Section E 10 3 Issue 1 Hydraulic Pump JS200 JS240...
Page 263: ...30 2 Section E Hydraulics 9803 6400 Section E 30 2 Issue 1 Control Valve JS200 JS240...
Page 264: ...30 3 Section E Hydraulics 9803 6400 Section E 30 3 Issue 1 Control Valve JS200 JS240...
Page 265: ...30 4 Section E Hydraulics 9803 6400 Section E 30 4 Issue 1 Control Valve JS200 JS240...
Page 266: ...30 5 Section E Hydraulics 9803 6400 Section E 30 5 Issue 1 Control Valve JS200 JS240...
Page 267: ...30 6 Section E Hydraulics 9803 6400 Section E 30 6 Issue 1 Control Valve JS200 JS240...
Page 268: ...30 7 Section E Hydraulics 9803 6400 Section E 30 7 Issue 1 Control Valve JS200 JS240...
Page 327: ...51 12 Section E Hydraulics 9803 6400 Section E 51 12 Issue 1 Solenoid Valve 8 spool...
Page 328: ...55 1 Schematic Section E Hydraulics 9803 6400 Section E 55 1 Issue 1 Shuttle Valve...
Page 330: ...55 3 Schematic Section E Hydraulics 9803 6400 Section E 55 3 Issue 1 Cushion Valves...
Page 481: ...7 15 Section F Transmission 9803 6400 Section F 7 15 Issue 2 Motor...
Page 482: ...7 16 Section F Transmission 9803 6400 Section F 7 16 Issue 1 Motor...