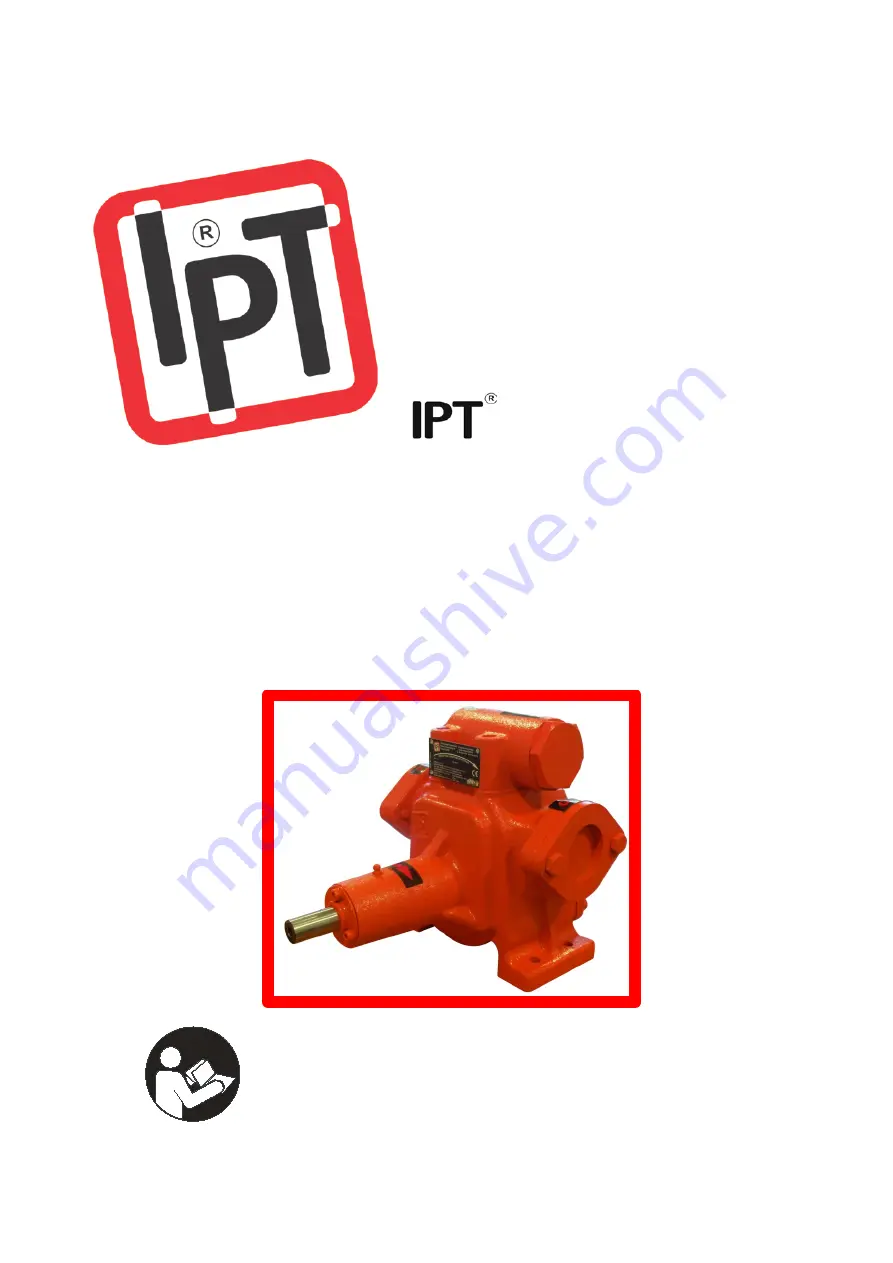
Published: 23.05.2008 Revised: 13.09.2019
*IPT reserves the right to change the construction and design of the products at any time without being
obliged to change previous models accordingly.
AKARYAKIT MALZ. PETROL
KIMYA SAN. ve TIC. LTD.STI.
ER 1134Y
FUEL PUMP
OPERATION AND MAINTENANCE MANUAL
DO NOT OPERATE OR MAINTENANCE THE PUMP BEFORE
READING THIS MANUAL.
Summary of Contents for ER 1134Y
Page 17: ...15 6 2 Disassembly Figure 17 Pump Disassembly ...
Page 24: ......