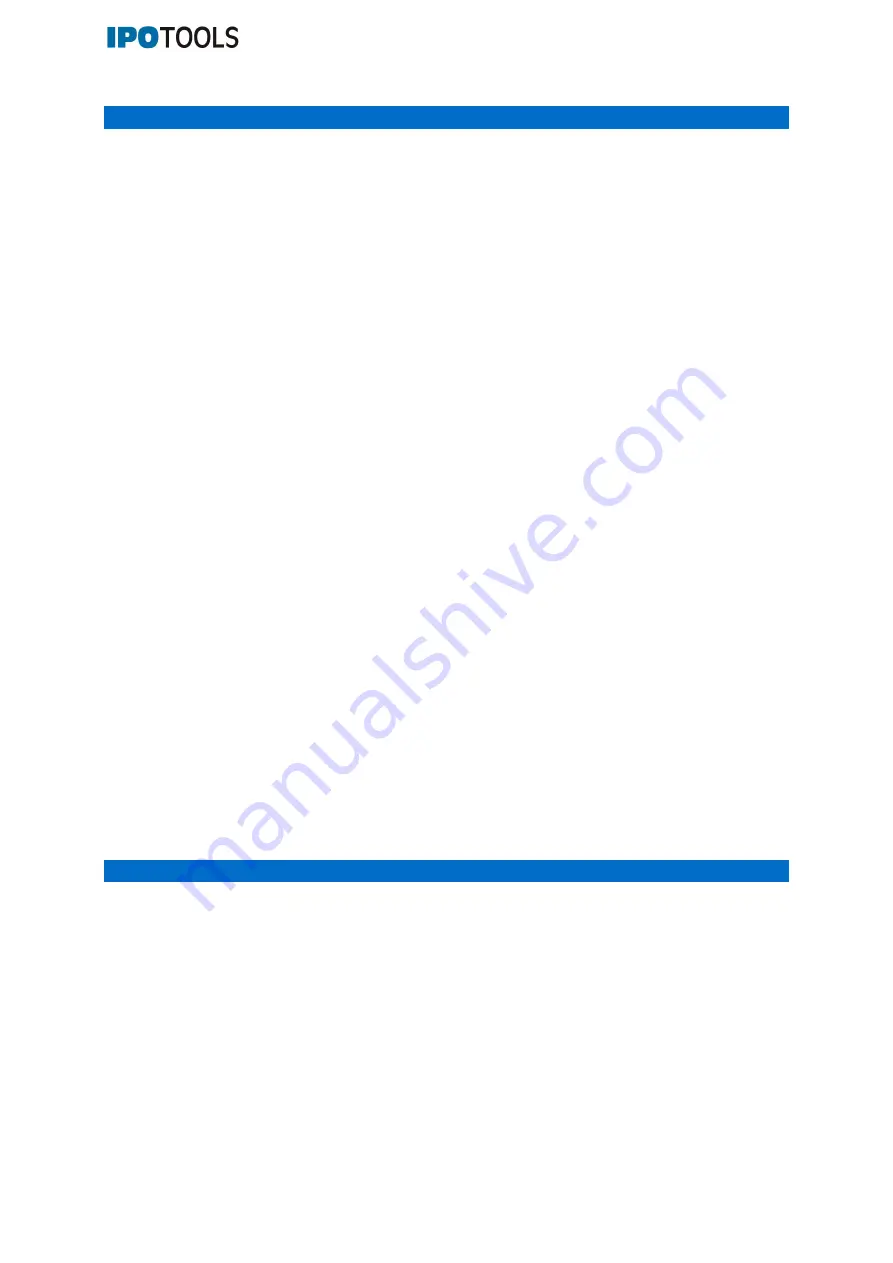
MIG-160ER
12
MIG MAG WELDING – WHICH WELDING WIRE?
A MIG welding wire is indispensable for arc welding because it is inserted into the construction during
welding and thus creates a strong connection. MIG welding wires are located on wire rolls and are
differentiated depending on the material, roll and wire diameter. When choosing the right MIG welding
wire, you must consider the material composition, the quality, and the suitable wire diameter for the
welding current. As a rule, the thicker the welding wire, the stronger the materials that can be welded
with it. However, the material composition, which depends on the application, is particularly important
when making the selection. The right choice depends on the material and material thickness that you
want to weld. The rule applies that the additional material is the same as the material of the workpiece.
You can choose from the following types of welding wire:
Solid wire - Solid wire refers to welding wires such as steel and stainless steel, which require a
protective gas to prevent oxidation during the welding process. The shielding gas guarantees a stable
arc and protects the liquid weld pool from the ingress of air from the atmosphere. This variant is used
by more than 80% of users because it produces less spatter, and the seams are of better quality than
those produced by welding without gas. Solid wires are also gentler on the wire feed in the device due
to their higher column cross-section strength, they are also stiffer and do not bend as easily. A gas
cylinder, a manometer and a wire feed roller with a V-groove are used for welding with solid wire. The
protective gas used for steel (82% argon and 18% CO2) and stainless steel (97.5% argon and 2.5%
CO2).
Cored Wire / FLUX / Gasless Wire - These wires consist of a thin metallic jacket that is filled with
powder and layered with metal compounds and then rolled into a cylinder to shape the finished wire. At
high temperatures, the FLUX wire creates an atmosphere with protective gas, which means that you do
not need a gas cylinder or manometer for use. The cored wire is softer than the solid wire and behaves
in a similar way to the aluminium wire when it is fed to the workpiece, which can mean less safety in
feeding and possible crushing of the wire when it exits the drive. For cored wire, you will find special
knurled wire feed rollers which have small teeth in the groove so that the wire is better gripped and thus
a better feed is created, but over time the surface of the welding wire will slowly erode, which can lead
to blockages in the wire guide A U-groove roller for cored wire can also be used, thanks to which one
can avoid a blockage at the price of lower feed quality. Compared to solid wire, cored wire welding has
the advantage that you do not need any accessories for gas, you can also do work outside, but there
are also disadvantages because this method creates more spatter, the slag must be removed, and the
quality of the seams is poorer than with inert gas welding. Shielding gas is not used for cored wire.
TROUBLESHOOTING
Our welding machines are always tested and calibrated before shipment. Any unauthorized
modification of the device is prohibited and has a negative effect on the guarantee!
The modifications can only be caried out by the technicians of the sales company!
The operating instructions must be read carefully to ensure that there are no unintended complications
that could endanger the user.
Before starting any repairs, it is necessary to switch off the welding machine!
If there is a problem with the device and there is no authorized specialist in your place of residence, it
is best to contact the seller.
For simple problems and errors on the welding machine, please follow the table below: