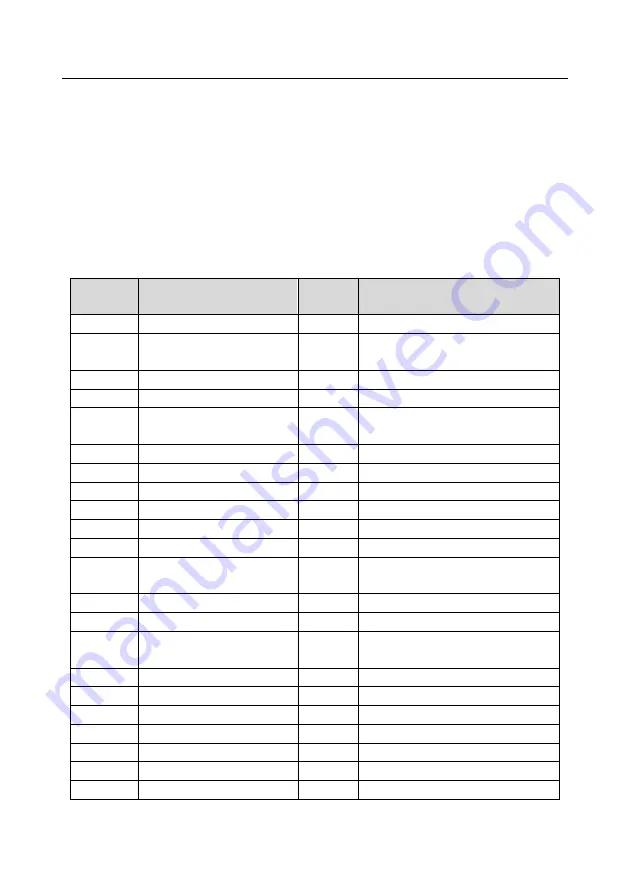
Goodrive350-19 series VFD for crane
Commissioning guidelines
-49-
the onsite function terminals are inconsistent with the terminals shown in the figure, adjust the input
and output terminal functions according to the actual wiring after selecting this application macro.
5.4.2 Commissioning procedure
1. Check the wiring and ensure the wiring is proper.
2. Set P00.18=1 to restore to default settings.
3. Set motor nameplate parameters in P02.
4. Set P90.00=4 to select the application macro for tower crane slewing.
5. Perform low-speed trial run.
5.4.3 Macro parameters (P90.00=4)
Function
code
Name
Setting
Remarks
P00.01
Channel of running commands
1
Terminal
P00.06
Setting channel of A frequency
command
6
Multi-step speed running
P00.11
ACC time 1
10.0s
Low-frequency ACC time
P00.12
DEC time 1
18.0s
Low-frequency DEC time
P01.01
Starting frequency of direct
start
1.50Hz
P01.15
Stop speed
1.00Hz
P05.03
Function of S3
7
Fault reset
P05.04
Function of S4
6
Coast to stop
P05.08
Input terminal polarity
0x08
NC when S4 uses coasting to stop.
P06.03
RO1 output
5
VFD in fault
P06.04
RO2 output
9
Running in zero speed
P06.05
Output terminal polarity
selection
0x4
RO1 is NC.
P08.00
ACC time 2
15.0s
High-frequency ACC time
P08.01
DEC time 2
13.0s
High-frequency DEC time
P08.19
Switching frequency of
ACC/DEC time
16.00Hz
If the running frequency is greater than
P08.19, switch to ACC/DEC time 2.
P10.04
Multi-step speed 1
16.0%
Corresponding to the max. frequency
P10.06
Multi-step speed 2
36.0%
Corresponding to the max. frequency
P10.08
Multi-step speed 3
60.0%
Corresponding to the max. frequency
P10.10
Multi-step speed 4
100.0%
Corresponding to the max. frequency
P25.01
Function of S5
16
Multi-step speed terminal 1
P25.02
Function of S6
17
Multi-step speed terminal 2
P25.03
Function of S7
18
Multi-step speed terminal 3