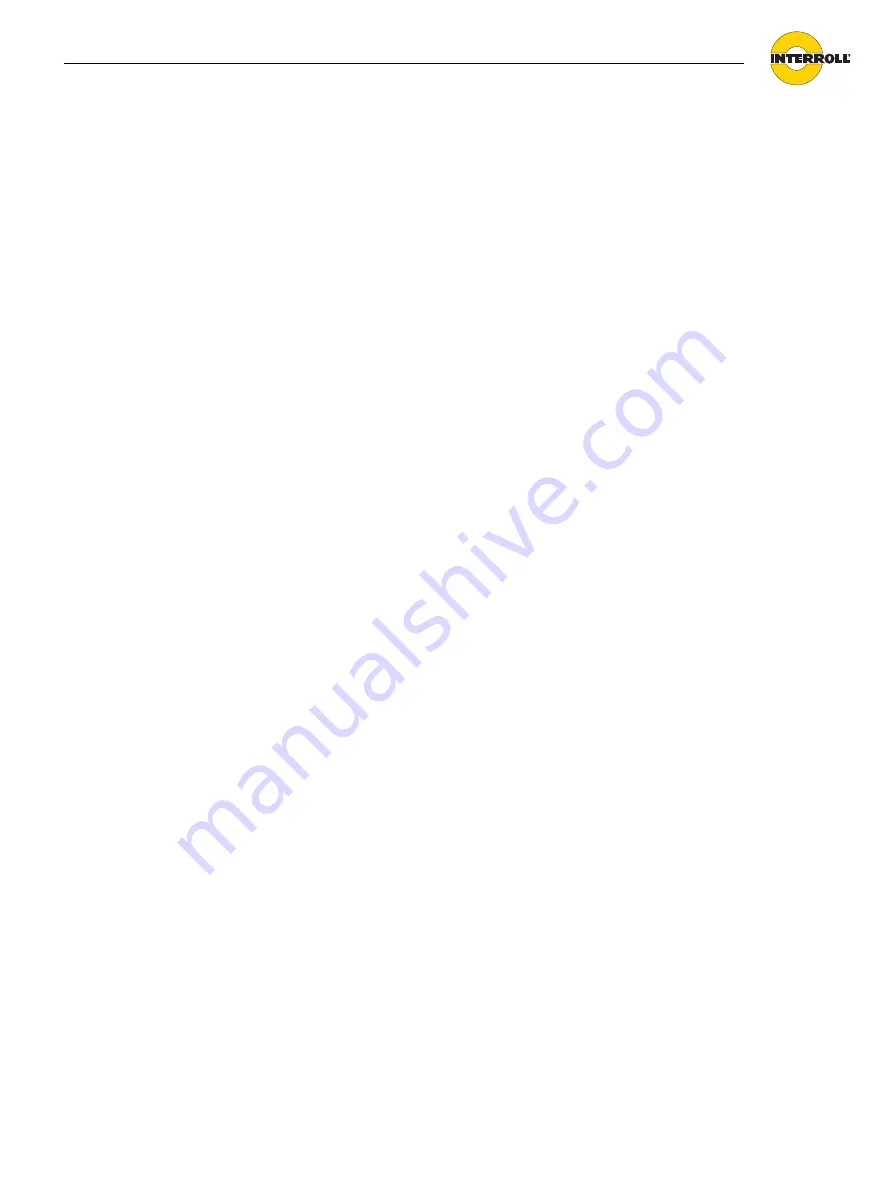
29
Version 3.0 (04/2013) en
Translation of the original instructions
RollerDrive EC100 / EC110
Appendix
Installation Declaration
in accordance with the EC Machinery Directive 2006/42/EC, Appendix II B
The manufacturer:
hereby declares with sole responsibility that the product range
•
RollerDrive EC1xx
is not a ready-to-use machine as defined by the EC Machinery Directive
and, therefore, does not fully comply with the requirements of this
directive. Initial start-up of these conveyor modules is not permitted until
conformity of the entire machine/system in which they are installed has
been declared via the EC Machinery Directive.
The health and safety requirements as stated in Appendix I have been applied.
The special technical documents as stated in Appendix VII B have been compiled
and will be sent to the responsible authority if necessary.
Person authorized to compile the technical documents: Georg Malina,
Interroll Engineering GmbH, Hoeferhof 16, D - 42929 Wermelskirchen
Applied EC directives:
•
Machinery Directive 98/37/EC with the amendment 98/79/EC
•
EMC Directive 2004/108/EC
•
RoHS Directive 2002/95/EC
Applied harmonized standards:
•
EN ISO 12100 Parts 1 and 2 "Safety of machinery - Basic concepts, general
principles for design" - Part 1: "Basic terminology, methodology" -
Part 2: "Technical principles"
Wermelskirchen, 31st March 2010
Armin Lindholm
(Managing Director)
(This declaration can be obtained at www.interroll.com, if needed.)
Interroll Engineering GmbH
Hoeferhof 16
D - 42929 Wermelskirchen
Germany