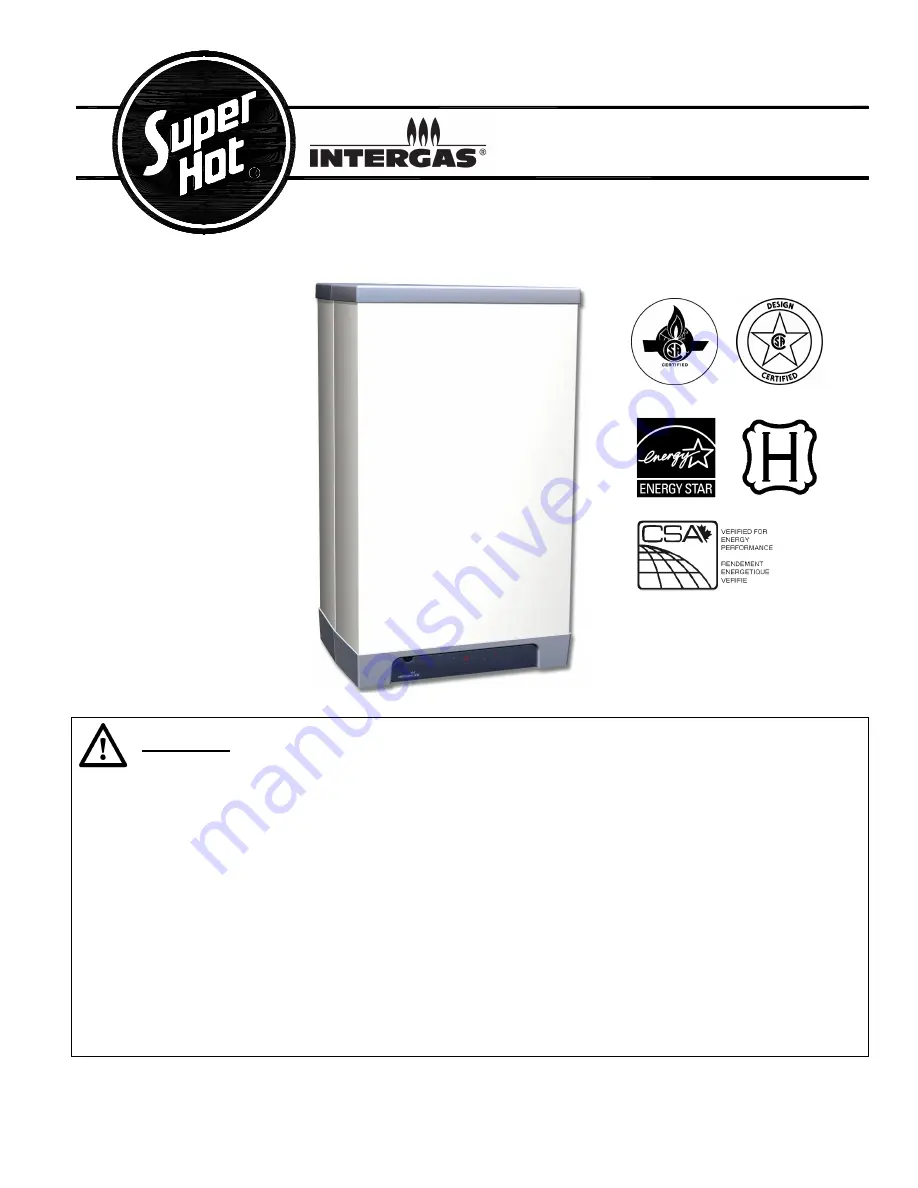
PN7331833
Model: HSE – 125 – N/P
Gas-fired Condensing Boiler and
Instantaneous Water Heater
INSTALLATION AND SERVICE MANUAL
Allied Engineering Company
Division of E-Z-Rect Manufacturing Ltd.
Manufacturers of Gas and Electric Boilers, Stainless Steel Tanks, Heat Exchangers and Electric Boosters.
94 Riverside Drive, North Vancouver, BC V7H 2M6
•
Tel: (604) 929-1214
•
www.alliedboilers.com
WARNING
If the information in this manual is not followed exactly, a fire or explosion may result causing
property damage, personal injury or loss of life.
•
Do not store or use gasoline or other flammable vapors and liquids in the vicinity of this or any
other appliance.
•
WHAT TO DO IF YOU SMELL GAS
- Do not try to light any appliance.
- Do not touch any electrical switch; do not use any phone in your building.
- Immediately call your gas supplier from a neighbor’s phone. Follow the gas supplier’s
instructions.
- If you cannot reach your gas supplier, call the fire department.
•
Installation and service must be performed by a qualified installer, service agency or the gas
supplier.
•
Improper, installation, adjustment, alteration, service or maintenance can cause property damage,
personal injury or loss of life. Read all instructions before installation or service.
•
Save this manual for future reference.
EEV
246473