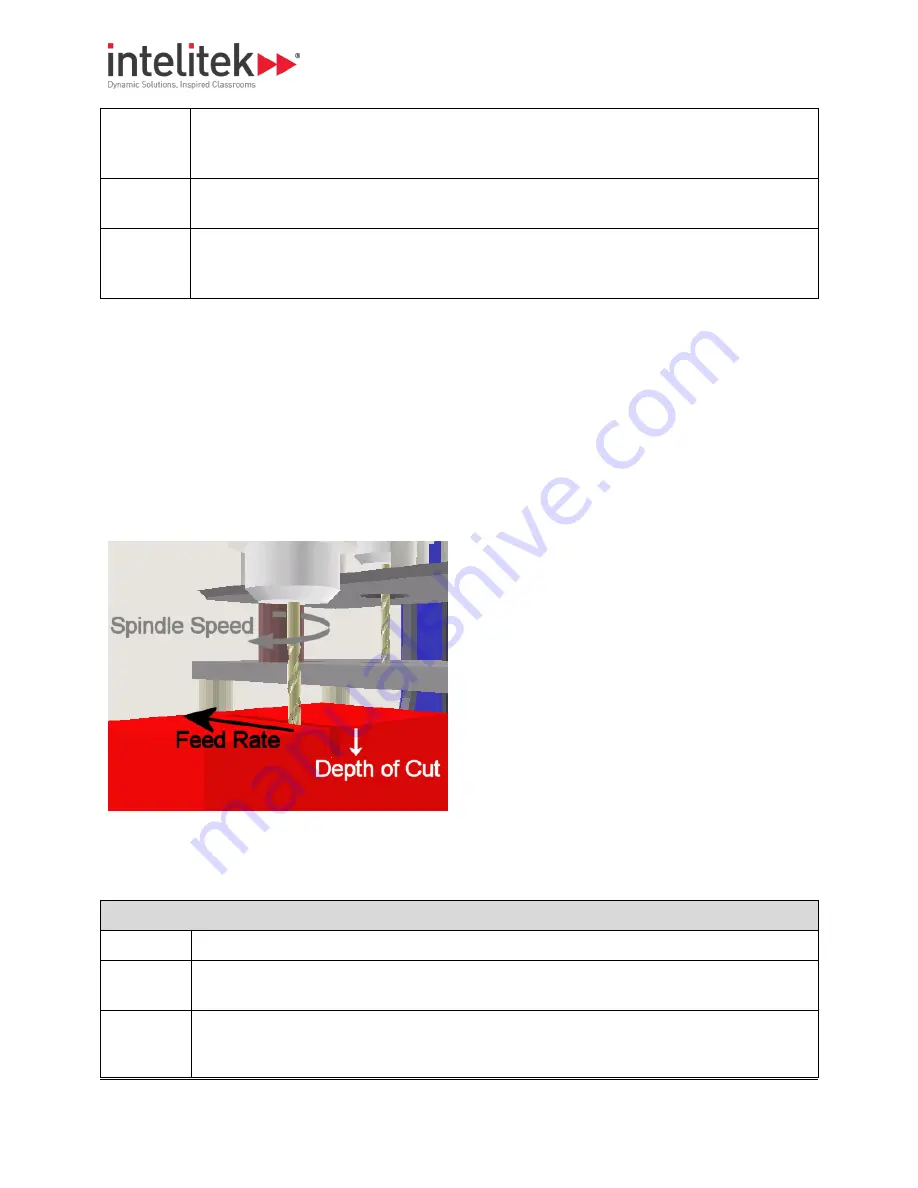
11 An Introduction to CNC Milling
11.3 Setting Feed Rate and Depth of Cut
162
Heat
production
High spindle speeds may produce excess heat which can cause the workpiece to expand. If
the workpiece expands, the cutting tool will rub rather than cut the material, resulting in a
poor surface finish.
Material
type
Some materials require higher spindle speeds to ensure a good finish.
Load on
spindle
motor
Heavy cuts at low speeds will make the motor run hotter than lighter cuts at higher
speeds. The selected feed rate and depth of cut should not cause the spindle motor to
greatly lose speed or cause the tool to chatter against the workpiece.
11.3.
SETTING FEED RATE AND DEPTH OF CUT
Feed rate (also known as feed), and depth of cut (also known as cut) are central terms in NC milling.
Milling involves removing material from the top surface or a side face of a workpiece. This is
accomplished by advancing the cutting tool into the workpiece by an appropriate amount (depth of cut).
The depth of cut is the vertical distance between the surface of the workpiece and the depth to which
the cutting tool enters the workpiece.
The feed rate is the speed at which the tool moves across the workpiece.
These concepts are illustrated in this image.
When selecting a feed rate and depth of cut, the factors listed in the table below must be taken into
account. You should consult your machinist’s handbook for selecting a feed rate based on spindle speed
and material type. Experience and experimentation will enable you to establish feed rates best suited to
particular applications.
Info Table: Feed Rate and Depth of Cut Factors
Factor
Description
Spindle
speed
The feed rate and depth of cut you choose must be suitable for the spindle speed chosen.
Material
used
Material properties may dictate maximum and minimum feed rates and depths of cut.
Surface finishes may suffer if machining parameters are not set appropriately for the