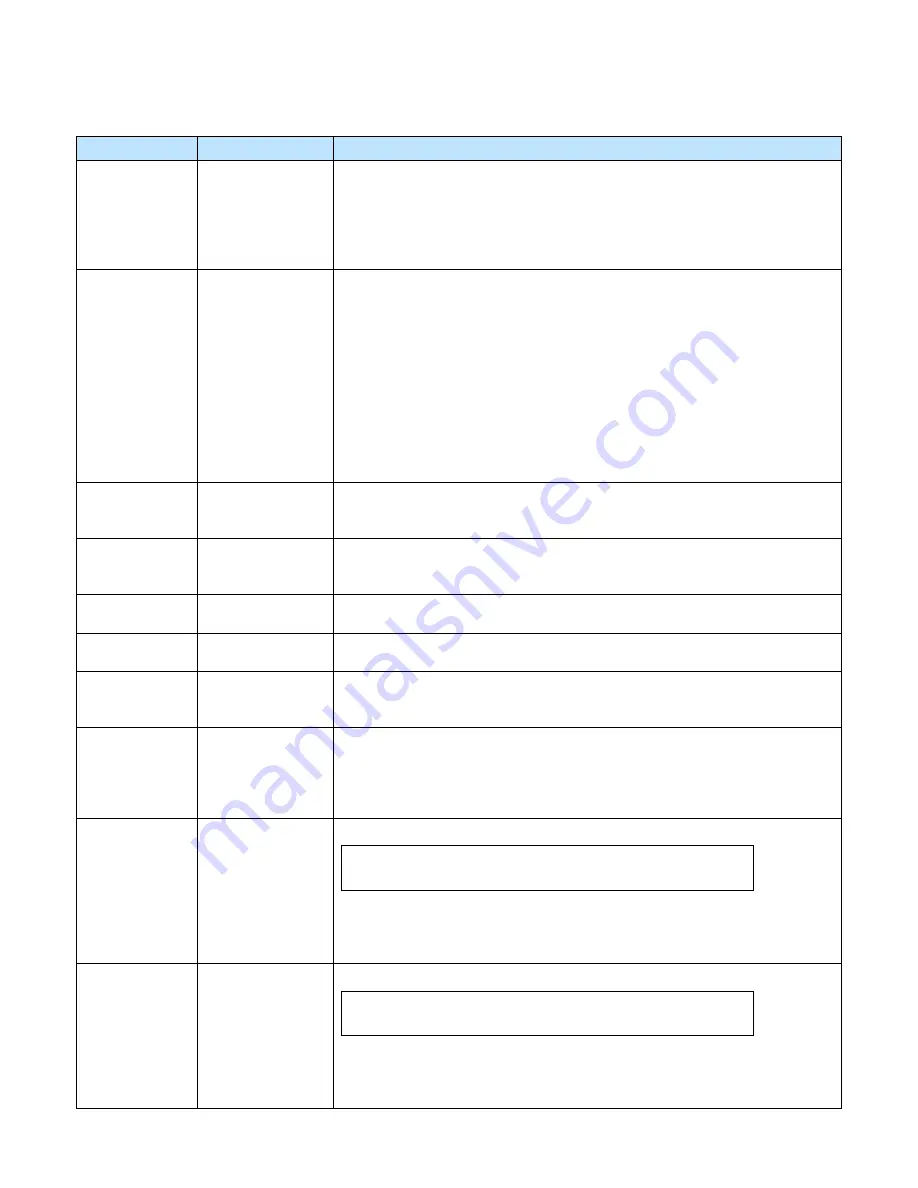
Intel® Server D50TNP Family Integration and Service Guide
91
System settings that are not configurable, because of security settings or configuration limits, will be grayed
out and are not accessible.
Table 3. BIOS Setup: Keyboard Command Bar
Key
Option
Description
<Enter>
Execute Command
The <Enter> key is used to:
•
Activate submenus when the selected feature is a submenu, or
•
Display a pick list if a selected option has a value field, or
•
Select a subfield for multi-valued features like time and date.
If a pick list is displayed, the <Enter> key selects the currently highlighted item,
undoes the pick list, and returns the focus to the parent menu.
<Esc>
Exit
The <Esc> key provides a mechanism for backing out of any field. When the
<Esc>
key is pressed while editing any field or selecting features of a menu, the
parent menu is re-entered.
When the
<Esc>
key is pressed in any submenu, the parent menu is re-entered.
When the
<Esc>
key is pressed in any major menu, the exit confirmation window
is displayed and the user is asked whether changes can be discarded.
If “No” is selected and the <Enter> key is pressed, or if the
<Esc>
key is pressed,
the user is returned to where they were before
<Esc>
was pressed, without
affecting any existing settings. If “Yes” is selected and the
<Enter>
key is pressed,
the setup is exited and the BIOS returns to the main System Options Menu
screen.
↑
Select Item
The up arrow is used to select the previous value in a pick list, or the previous
option in a menu item
’
s option list. The selected item must then be activated by
pressing the
<Enter>
key.
↓
Select Item
The down arrow is used to select the next value in a menu item
’
s option list, or a
value field
’
s pick list. The selected item must then be activated by pressing the
<Enter>
key.
← →
Select Menu
The left and right arrow keys are used to move between the major menu pages.
The keys have no effect if a sub-menu or pick list is displayed.
<Tab>
Select Field
The <Tab> key is used to move between fields. For example, <Tab> can be used
to move from hours to minutes in the time item in the main menu.
−
Change Value
The minus key on the keypad is used to change the value of the current item to
the previous value. This key scrolls through the values in the associated pick list
without displaying the full list.
+
Change Value
The plus key on the keypad is used to change the value of the current menu item
to the next value. This key scrolls through the values in the associated pick list
without displaying the full list. On 106-key Japanese keyboards, the plus key has
a different scan code than the plus key on the other keyboards but will have the
same effect.
<F9>
Setup Defaults
Pressing the
<F9>
key causes the following to display:
Load Optimized Defaults?
Yes No
If “Yes” is highlighted and
<Enter>
is pressed, all setup fields are set to their
default values. If “No” is highlighted and
<Enter>
is pressed, or if the
<Esc>
key is
pressed, the user is returned to where they were before
<F9>
was pressed
without affecting any existing field values.
<F10>
Save and Exit
Pressing the
<F10>
key causes the following message to display:
Save configuration and reset?
Yes No
If “Yes” is highlighted and
<Enter>
is pressed, all changes are saved and the
s
etup is exited. If “No” is highlighted and
<Enter>
is pressed, or the
<Esc>
key is
pressed, the user is returned to where they were before
<F10>
was pressed
without affecting any existing values.