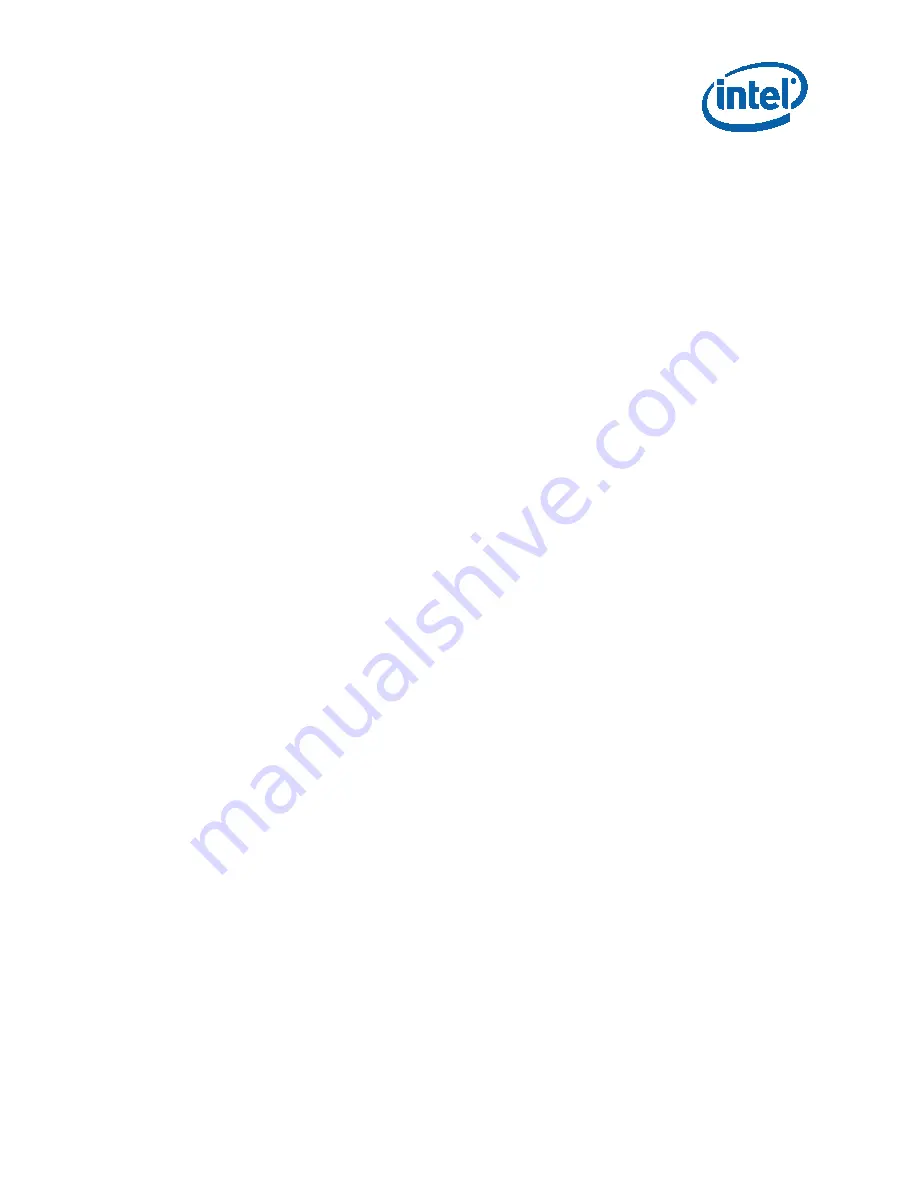
Thermal Metrology
Thermal and Mechanical Design Guidelines
27
Assume the TDP, as listed in the datasheet, is 100 W and the maximum case
temperature from the thermal profile for 100 W is 67° C. Assume as well that the
system airflow has been designed such that the local ambient temperature is 38° C.
Then, the following could be calculated using equation 1 from above:
Ψ
CA
= (T
C,
−
T
A
) / TDP = (67 – 38) / 100 = 0.29° C/W
To determine the required heatsink performance, a heatsink solution provider would
need to determine
Ψ
CS
performance for the selected TIM and mechanical load
configuration. If the heatsink solution were designed to work with a TIM material
performing at
Ψ
CS
≤
0.10° C/W, solving for equation 2 from above, the performance of
the heatsink would be:
Ψ
SA
=
Ψ
CA
−
Ψ
CS
= 0.29
−
0.10 = 0.19° C/W
3.2
Processor Thermal Solution Performance
Assessment
Thermal performance of a heatsink should be assessed using a thermal test vehicle
(TTV) provided by Intel. The TTV is a stable heat source that the user can make
accurate power measurement, whereas processors can introduce additional factors
that can impact test results. In particular, the power level from actual processors
varies significantly, even when running the maximum power application provided by
Intel, due to variances in the manufacturing process. The TTV provides consistent
power and power density for thermal solution characterization and results can be
easily translated to real processor performance. Accurate measurement of the power
dissipated by an actual processor is beyond the scope of this document.
Once the thermal solution is designed and validated with the TTV, it is strongly
recommended to verify functionality of the thermal solution on real processors and on
fully integrated systems. The Intel maximum power application enables steady power
dissipation on a processor to assist in this testing. This maximum power application is
provided by Intel.
3.3
Local Ambient Temperature Measurement
Guidelines
The local ambient temperature T
A
is the temperature of the ambient air surrounding
the processor. For a passive heatsink, T
A
is defined as the heatsink approach air
temperature; for an actively cooled heatsink, it is the temperature of inlet air to the
active cooling fan.
It is worthwhile to determine the local ambient temperature in the chassis around the
processor to understand the effect it may have on the case temperature.
T
A
is best measured by averaging temperature measurements at multiple locations in
the heatsink inlet airflow. This method helps reduce error and eliminate minor spatial
variations in temperature. The following guidelines are meant to enable accurate
determination of the localized air temperature around the processor during system
thermal testing.
Summary of Contents for CELERON PROCESSOR E3000 - THERMAL AND MECHANICAL DESIGN
Page 24: ...Processor Thermal Mechanical Information 24 Thermal and Mechanical Design Guidelines ...
Page 80: ...Heatsink Clip Load Metrology 80 Thermal and Mechanical Design Guidelines ...
Page 82: ...Thermal Interface Management 82 Thermal and Mechanical Design Guidelines ...
Page 108: ...Fan Performance for Reference Design 108 Thermal and Mechanical Design Guidelines ...