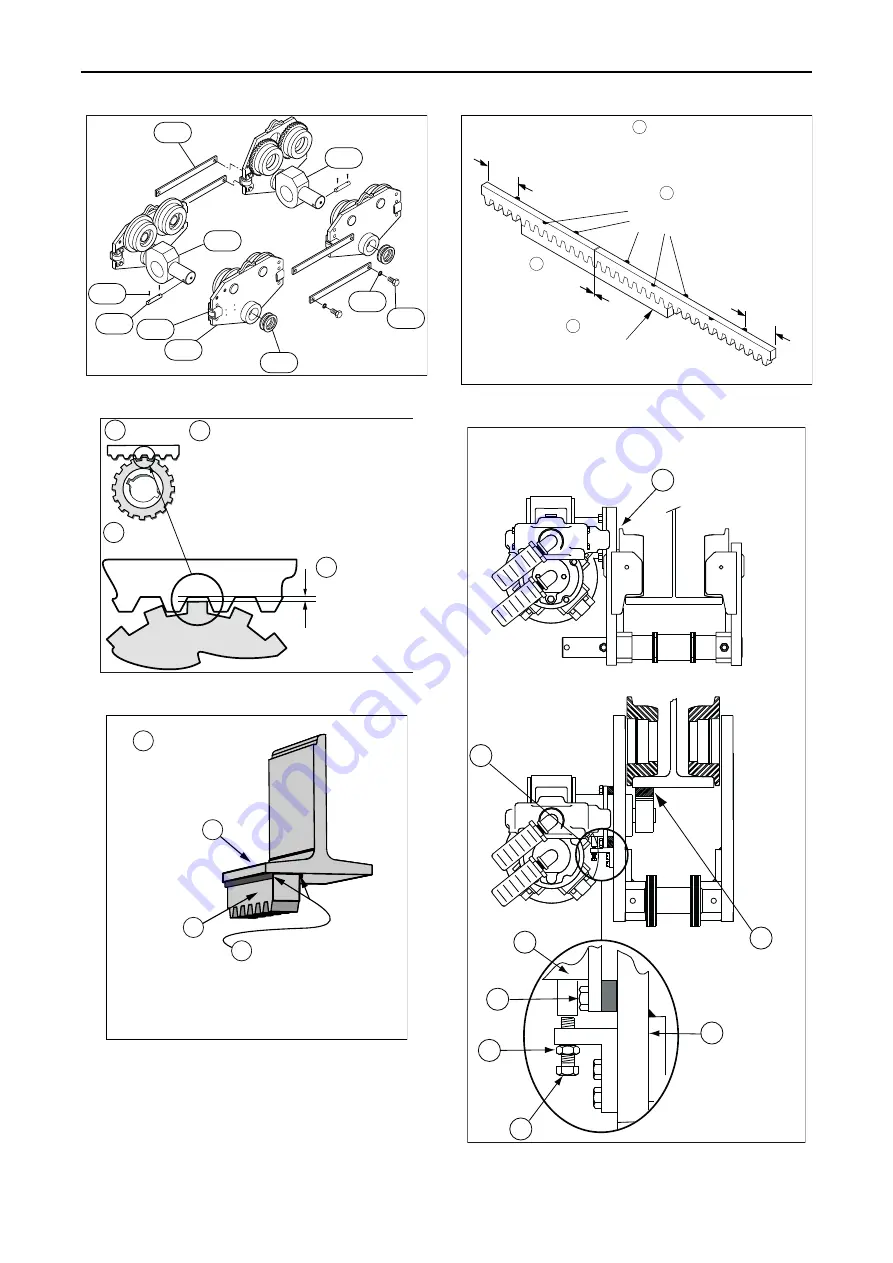
17
Figure 5. MHP0352
159
170
158
156
150
165
173
174
157
170
Figure 6. MHP1177
Maintain clearance between rack and
pinion teeth of 0.06 inch (minimum) to
0.10 inch (maximum) [1.5 to 2.5 mm] to
prevent pinion binding during operation.
Measure gap between outside
diameter of drive pinion and root of
rack segment.
Note: 0.08 inch feeler gauge use is
recommended.
Rack
Pinion
0.06 to 0.10 inch
(1.5 to 2.5 mm)
A
B
C
D
Figure 7. MHP1178
Rack
Segment
Lower Beam
Flange
A
Hoist Trolley
Drive Assembly
Mounted This Side.
Fillet Weld:
• Allow 1/4 inch (6.5 mm)
clearance between edge
of lower flange and rack
segment.
• Apply weld to both sides
of rack segment.
B
C
D
Figure 8. MHP3016
B
C
D
6 inches
(152 mm)
6 inches
(152 mm)
Stagger welds
along rack
A
(Not to scale)
Use rack guide for
correct track positioning
Check clearance
between racks
0.08” (2 mm)
Figure 9. MHP1605
A
Normal trolley drive mounded
above supported bean between
trolley wheels
Located behind
motor housing
Reducer
Adapter
Mounting
Capscrew
Jam Nut
Side Plate
Adjustment
Capscrew
Trolley rack drive
mounted below
support beam
B
G
H
D
C
E
F